Rapid advancement in quality testing for large PV plants
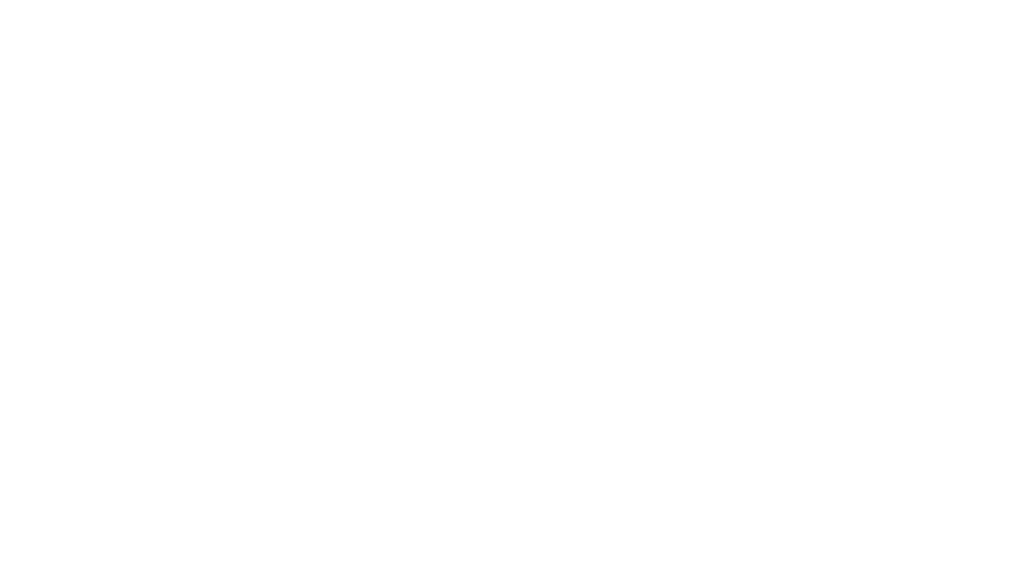
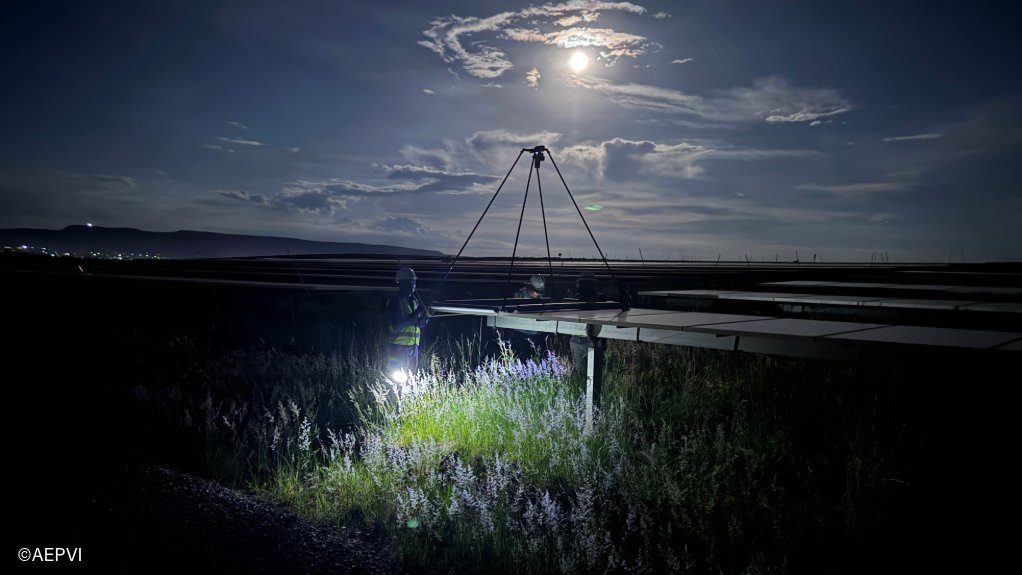
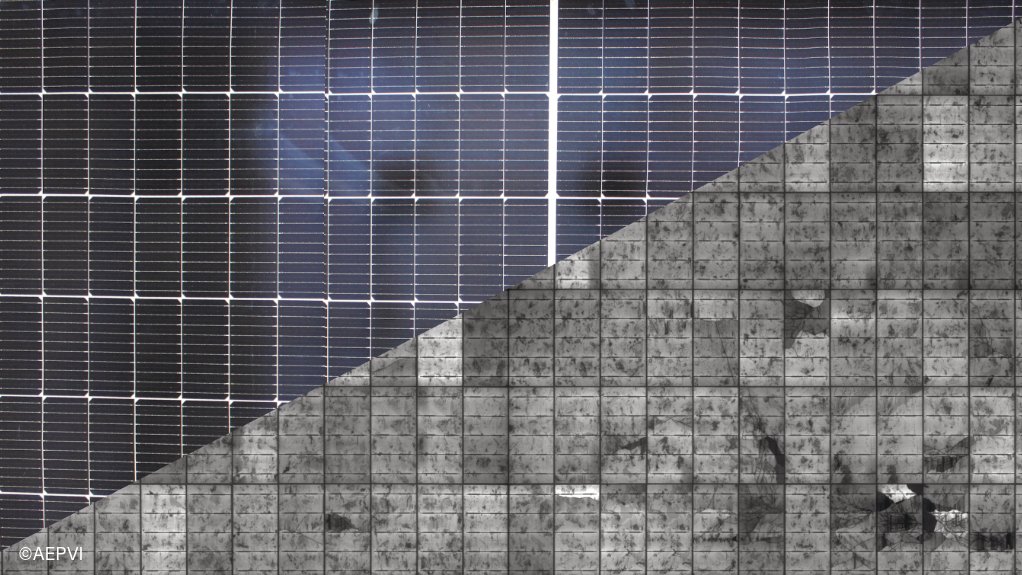
Electroluminescence imaging of PV panels is done at night
Photo by PVinsight
A PV module intersected with an electroluminescence image indicating cracks and defects that are not visible to the naked eye
Photo by PVinsight
The latest method of electroluminescence (EL) testing of solar photovoltaic (PV) panels for large plants is a game-changer for business and industry in South Africa, Heather Dugmore writes.
The growth in solar photovoltaic (PV) plants in South Africa in the commercial and industrial space is huge and many operations are finding their PV plants have large numbers of solar modules or solar panels, as they are commonly called, that are underperforming.
It is a significant financial investment and investors and insurers should require that independent testing is done as part of operations and maintenance contracts.
Solar modules should be independently tested pre-installation, on-site once installed, during the warranty period and over time.
Large PV plants have hundreds of thousands of modules, the majority of which are imported, mainly from China and Vietnam. For example, a large 70 MW PV plant would have about 300 000 modules, of which 300 to 500 modules need to be independently tested to give the buyer greater peace of mind that the PV modules are without defects or that they meet the manufacturer's specifications in terms of quality, power output and lifespan.
What is extraordinary is that millions are spent on PV plants while the tests cost in the thousands, but many companies, insurers and investors do not include independent testing in their contracts. Many are not aware that independent testing is available and why it is essential.
The EL imaging testing side is making great strides: “With our previous setup, we could test 100 modules per night and we can now do 500 to 800 per night, which is the best testing rate in South Africa, and the increase allows us to expand the sample size and provide statistically meaningful results to our clients,” explains Dr Jacqui Crozier McCleland who has a PhD in physics and is the quality and technical manager of PVinsight (PVi) – the only accredited mobile laboratory testing service in South Africa, offering in-lab and on-site PV testing services.
“We test the modules at night so that the EL camera can detect the emitted EL light without interference from other light sources. Testing at night also means the PV plant does not lose production during the day,” Crozier McCleland explains.
To advance testing in South Africa and achieve far higher volumes per night, the company has formed a strategic partnership with German company Aerial PV Inspection (AePVI) and invested in new EL cameras and other specialised equipment from them, which they started using in January this year on in situ inspections in South Africa.
Andreas Fladung, co-founder of AePVI, who joined PVi for the testing in January, says: “Today, innovative high-volume EL measurements in the field enable clear and meaningful quality analyses at cell level with regard to production, transport and installation loads, ageing processes and environmental events. No other measurement method currently offers this depth of analysis.”
The managing director and founder of PVi is professor of physics, Ernest van Dyk who established the company in 2017 after it was spun out of the Photovoltaics Research Group (PVRG) in the Department of Physics at Nelson Mandela University (NMU). “We have over 30 years of experience and knowledge of PV systems and device research,” explains Van Dyk.
“We test modules at all levels, from the utility-scale that feeds into the electricity grid to plants that power industries, companies and communities. Our testing is done according to the International Electrotechnical Commission standards and we are accredited as a testing laboratory with the South African National Accreditation System.”
PVi is run by a team of physicists and researchers from NMU and one of their key tests is the EL imaging test to see if the modules are damaged in any way. Damage can happen during the manufacturing process or when they are transported, handled and installed.
The light emitted by the modules during the EL imaging test is not in the visible spectrum and it picks up small defects that are invisible to the naked eye. Previously they had to take two images per module, but with the new camera they take one image per module, which considerably speeds up the process.
“With broken cells (which show up in the image as dark areas), the module won’t produce as much power as if they were all uniform. The decrease in power depends on the area of the module that is affected,” says Crozier McCleland. “There are also sometimes manufacturing defects that decrease the module’s performance.
“Defects can creep in at the manufacturer level, such as soldering or bus bar issues, or be caused by poor handling. Generally, if there are cracks in a module it is because at some point it was not transported properly or dropped or was handled incorrectly,” she explains.
“Cracks can also occur at the mounting stage if this is not done properly, and there have been numerous issues with rooftop installations where modules have been walked on during installation or when cleaned. Even small issues with the modules can lead to significant power loss.”
Which is why testing is essential. The tests can also be used in warranty claims. When clients are armed with an accredited module report, it greatly empowers them in terms of recourse with the manufacturer or project developer should any problems be detected.
The significant increase in large PV installations has resulted in an increase in the number of insurance claims, ranging from hail and handling damage to inferior quality modules to defective performance – there are all sorts of reasons.
Crozier McCleland explains that, when there is an insurance claim, some insurers require that every single module is tested, others require a percentage of modules. “This needs to be done in situ because if you remove them, you cannot say with absolute certainty where the damage occurred. What if they were damaged in transit to testing? A recent test PVi did was on all the modules inside a shipping container that had fallen over.”
All modules have certification at a factory level and large international companies do factory audits, but best practice is an independent, third-party assessment of the modules on arrival. What has worked well for companies is they have a pre- and post-installation contract with the manufacturer that they will have their modules independently tested before they are installed, and at 12 months, 24 months and annually after that.
“A lot of PV plants have ten-year warranties and if the manufacturer knows their modules will be tested, they have to make sure the quality is according to specification across the entire range of modules,” Crozier McCleland explains. “It’s possible that modules are constructed with a different Bill of Materials even though they are the same module type.
The PVi team’s close involvement in PV research at an international and South African university level, and their partnership with AePVI, ensures they keep abreast of the latest developments in manufacturing processes, solar module types and characterisation techniques. PVi collaborates with their sales partner GeoSUN in offering the service to the PV industry. GeoSUN is a 2012 spin-off company from Stellenbosch University.
As important as testing the new modules coming onto the market is to test the original utility-scale PV plants that are now ten years old, commissioned in 2014. Performance issues and degradation can naturally occur over time so it’s important to check these plants so that good decisions can be made about how to improve their performance or replace and update modules.
*Dugmore is a specialist writer in higher education.
Comments
Press Office
Announcements
What's On
Subscribe to improve your user experience...
Option 1 (equivalent of R125 a month):
Receive a weekly copy of Creamer Media's Engineering News & Mining Weekly magazine
(print copy for those in South Africa and e-magazine for those outside of South Africa)
Receive daily email newsletters
Access to full search results
Access archive of magazine back copies
Access to Projects in Progress
Access to ONE Research Report of your choice in PDF format
Option 2 (equivalent of R375 a month):
All benefits from Option 1
PLUS
Access to Creamer Media's Research Channel Africa for ALL Research Reports, in PDF format, on various industrial and mining sectors
including Electricity; Water; Energy Transition; Hydrogen; Roads, Rail and Ports; Coal; Gold; Platinum; Battery Metals; etc.
Already a subscriber?
Forgotten your password?
Receive weekly copy of Creamer Media's Engineering News & Mining Weekly magazine (print copy for those in South Africa and e-magazine for those outside of South Africa)
➕
Recieve daily email newsletters
➕
Access to full search results
➕
Access archive of magazine back copies
➕
Access to Projects in Progress
➕
Access to ONE Research Report of your choice in PDF format
RESEARCH CHANNEL AFRICA
R4500 (equivalent of R375 a month)
SUBSCRIBEAll benefits from Option 1
➕
Access to Creamer Media's Research Channel Africa for ALL Research Reports on various industrial and mining sectors, in PDF format, including on:
Electricity
➕
Water
➕
Energy Transition
➕
Hydrogen
➕
Roads, Rail and Ports
➕
Coal
➕
Gold
➕
Platinum
➕
Battery Metals
➕
etc.
Receive all benefits from Option 1 or Option 2 delivered to numerous people at your company
➕
Multiple User names and Passwords for simultaneous log-ins
➕
Intranet integration access to all in your organisation