Rockwell Automation underscores the importance of maintenance to improve asset availability
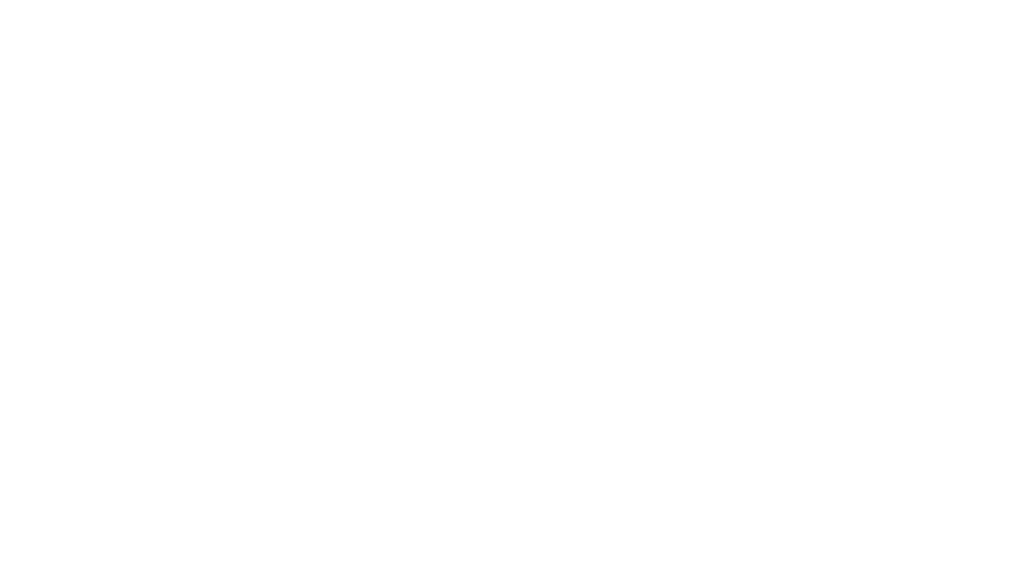
In this webinar recording, Rockwell Automation Information Solutions Leader: Africa Francois Du Toit discusses asset performance management for mining and metals
Considering that high-capital assets have such a huge impact on production, they cannot be under maintenance or downtime without production being affected to some extent.
Unscheduled downtime or maintenance in heavy asset industries, therefore, lead to a number of cost drivers within an industry, which directly affects the cost of goods sold, and may even result in difficulty in meeting contractual obligations.
Lost capacity filters down into labour costs, customer dissatisfaction, not meeting contractual requirements and a loss of profit, which, in the long term, drive up costs.
Taking all of these aspects into account, industrial automation service provider Rockwell Automation information solutions leader Francois du Toit emphasised that it was “critical to ensure that those assets are available as much as possible”.
Speaking during a webinar hosted by Rockwell on asset performance management in mining on August 17, he noted that a performance or asset maintenance strategy is “understanding that we need to know and understand how to monitor the assets to prevent unplanned downtime, or to do preventive maintenance before unplanned downtime arises”.
However, in order to understand how to get this level of availability out of an asset, one needs to understand that these various levels of maintenance practices currently exist in the market, though most organisations in the industrial sectors have a reactive maintenance schedule.
A reactive maintenance schedule, Du Toit explained, meant “running the asset until it fails, which then leads to unscheduled downtime, meaning that the asset needs to be repaired before it becomes available for use again”.
At a higher level, there are some organisations with critical assets that have a layer of preventive maintenance, which means that more regular maintenance is done than what is typically required, to ensure that unscheduled downtime does not occur.
Considering that the asset is then maintained more often than what is necessarily required, Du Toit remarked that this resulted in higher maintenance costs.
Many Rockwell clients, he added, had “a bigger focus on getting to that level of predictive or preventive maintenance”, though the question largely remained how this was achieved as an organisation, and what technologies and processes needed to be implemented in order to enable such a strategy.
About 55% of Rockwell’s heavy industry customers currently have computerised maintenance management systems (CMMS) in place, which support the maintenance strategy.
However, Du Toit advised that CMMS needed to be integrated properly to ensure an organisation could also plan for maintenance tasks that needed to be delivered.
“For example, if it is based on a preventive maintenance case, we know that we are about to throw about 2 000 running hours away from this asset being maintained. So, we need to schedule that maintenance and we need to have that integration in the schedule so that we've got the parts available to do the actual maintenance required.”
Following this, management and monitoring of the actual maintenance practitioners will be needed to ensure that the fix rates are efficient in-between repairs, and that they are fixing the asset correctly – all of which ultimately impact the asset’s uptime.
Specifically, in the reactive scenario, because maintenance is only scheduled after the asset has gone down, the time to repair increases dramatically, meaning a bigger loss of production.
“So, Rockwell provides an opportunity to tie in the technologies and the philosophies around management and maintenance of the asset in such a fashion that you work hand in hand to ensure the asset availability is as high as possible,” Du Toit commented.
Another, alternative route, he added, would be to implement a condition-based maintenance strategy, which requires critical information about the assets in order to understand their actual condition.
“It’s not just the overall asset, but also any sort of moving parts within that asset that we understand picks up the most wear and tear. So, from the reactive maintenance, you can see that you've got uptime, you've got a failure, and then you've got the tools and management to repair the damage or do the maintenance tasks.
“Whereas the moment you start implementing digital technologies, you've now got your reliability tool set, which are those sensors that scan for the ability vibration analysis, or frequency analysis (depending on the type of asset),” Du Toit explained.
These reliability tools all ultimately provide the organisation with the necessary information so that it can start analysing to ascertain the condition of the asset, and then feed that condition-based information into some sort of machine learning model.
“Feeding that information automatically into your CMMS means that it will understand what assets need to be maintained, when and where in the organisation and what parts are required to do that. Through implementing digital technologies, you're not just focusing on the asset itself, but also optimising the maintenance task.”
Ultimately, this leads to a decrease in downtime that needs to be recouped and, thereby, increases the availability of the asset, because it takes a shorter period to do small maintenance tasks.
IMPLEMENTATION
Du Toit further advised that, should organisations implement an asset performance management strategy, they needed to be cognisant of framework, automation and customer requirements.
“Typically, what we've seen as Rockwell is that automation and working with our customers around some of these things means that this strategy starts with a smart sensor that ensures the outcome. We are trying to predict what needs to be fixed so that we can accomplish, or avoid, a specific outcome.
“Once this is identified, a decision is then made about what smart sensors or reliability tools are needed to provide the organisation with condition-based data so that the specific asset can be used in the predictive maintenance model.”
While this route usually ensured ethical equipment effectiveness, Du Toit remarked that “various industries have different ways of calculating their required outcomes”.
“It doesn’t really matter what that calculation looks like, but it is important to understand what the organisation is trying to measure, because this will influence the predictive maintenance model for that asset.”
There are a multitude of technologies available at a low or inexpensive cost that would enable organisations to potentially retrofit their critical assets with the required Internet-of-Things (IoT) sensors to enable easier communication between elements in the existing industrial network, Du Toit noted.
Additionally, an organisation can also consider using a third-party or enhanced data science to interpret the data and ensure that the data is correct.
Machine-learning challenges could include failure to correlate data to a specific asset, along with the cause or failure, to build a model as accurate as possible.
“The model building is not such a big thing, because there are a lot of tools that will allow analysis of data and will then propose a specific model based on the data set that must be set.”
For organisations that have not implemented a CMMS, Du Toit stressed the importance of understanding their asset performance management strategy and their asset’s maintenance – particularly considering that they would not necessarily have a “proper way” of scheduling the asset maintenance or equipping their maintenance technicians.
Simultaneously, they also need to have a handle on the image-based condition of the assets, which is then based on the preventive maintenance model that they have of the asset and the indicators they are provided with.
“These organisations need to understand when the asset will fail, what their inventory looks like and ensure they have the necessary parts on hand to advance lead times so that when maintenance is scheduled based on the predictive model, everything can be in place by the time the maintenance is required,” Du Toit explained.
Having visibility in existing asset performance is critical, he added, especially as this would influence maintenance activities, which had to be prioritised in order to ensure that critical assets were available as much as possible.
“It’s important for organisations to analyse their assets’ maintenance requirements and understand the strategy surrounding that so that there is no loss of production or revenue,” he commented, adding that this holistic view of all the assets, and being able to harmonise them, would increase performance across the entire production line and more effectively deploy the required maintenance.
Comments
Press Office
Announcements
What's On
Subscribe to improve your user experience...
Option 1 (equivalent of R125 a month):
Receive a weekly copy of Creamer Media's Engineering News & Mining Weekly magazine
(print copy for those in South Africa and e-magazine for those outside of South Africa)
Receive daily email newsletters
Access to full search results
Access archive of magazine back copies
Access to Projects in Progress
Access to ONE Research Report of your choice in PDF format
Option 2 (equivalent of R375 a month):
All benefits from Option 1
PLUS
Access to Creamer Media's Research Channel Africa for ALL Research Reports, in PDF format, on various industrial and mining sectors
including Electricity; Water; Energy Transition; Hydrogen; Roads, Rail and Ports; Coal; Gold; Platinum; Battery Metals; etc.
Already a subscriber?
Forgotten your password?
Receive weekly copy of Creamer Media's Engineering News & Mining Weekly magazine (print copy for those in South Africa and e-magazine for those outside of South Africa)
➕
Recieve daily email newsletters
➕
Access to full search results
➕
Access archive of magazine back copies
➕
Access to Projects in Progress
➕
Access to ONE Research Report of your choice in PDF format
RESEARCH CHANNEL AFRICA
R4500 (equivalent of R375 a month)
SUBSCRIBEAll benefits from Option 1
➕
Access to Creamer Media's Research Channel Africa for ALL Research Reports on various industrial and mining sectors, in PDF format, including on:
Electricity
➕
Water
➕
Energy Transition
➕
Hydrogen
➕
Roads, Rail and Ports
➕
Coal
➕
Gold
➕
Platinum
➕
Battery Metals
➕
etc.
Receive all benefits from Option 1 or Option 2 delivered to numerous people at your company
➕
Multiple User names and Passwords for simultaneous log-ins
➕
Intranet integration access to all in your organisation