Rubber companies urged to go green
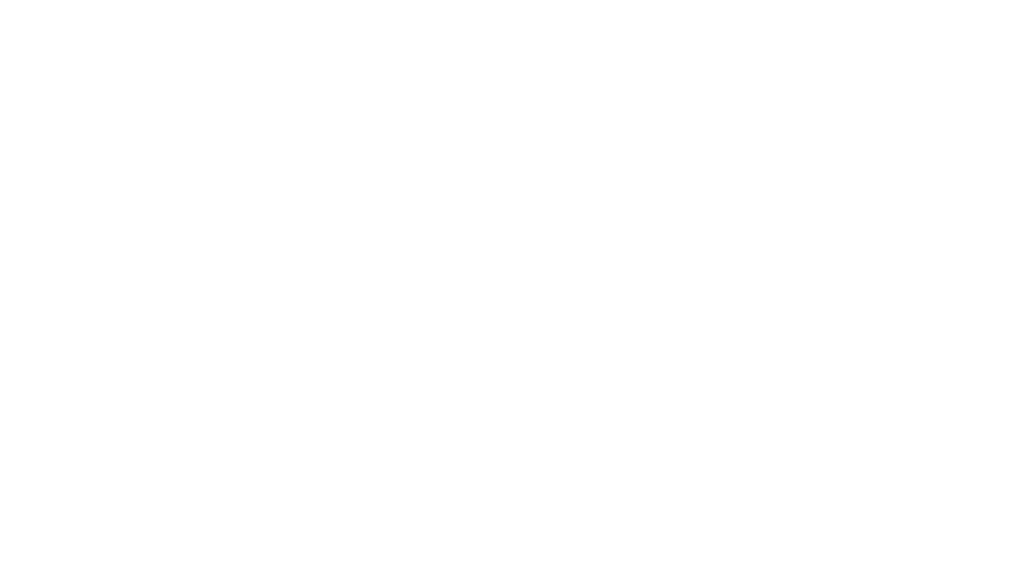
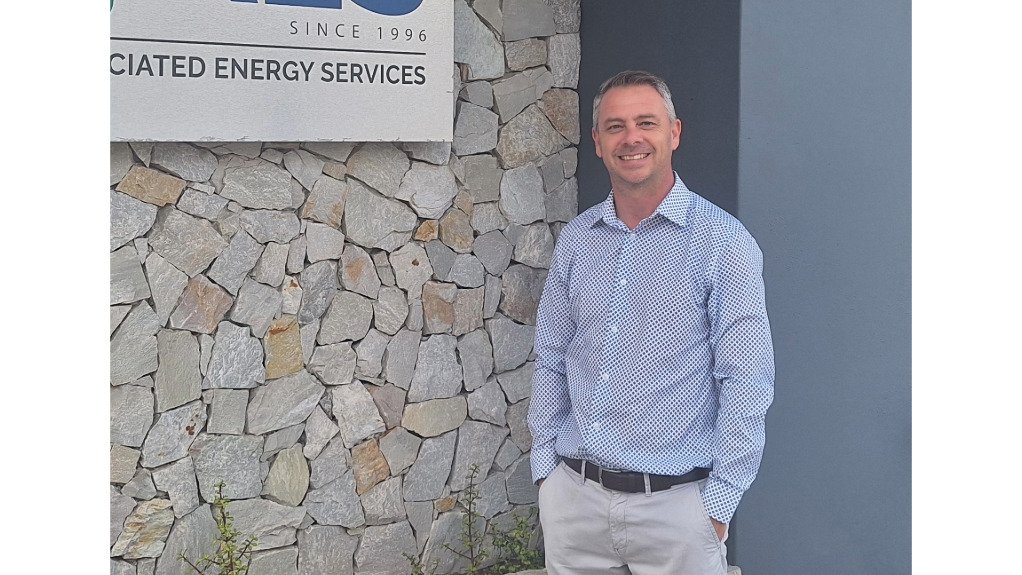
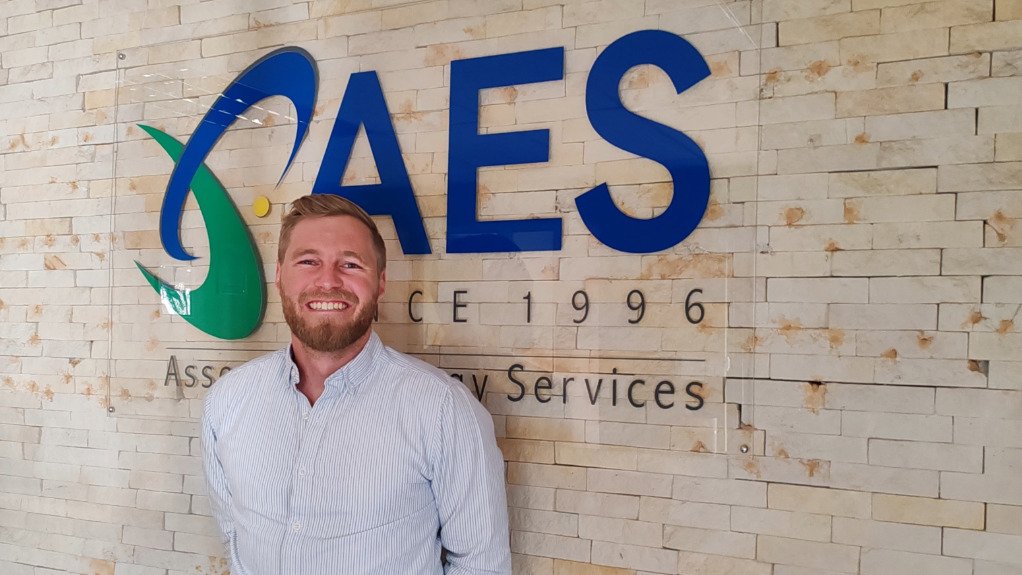
RAY LUND AES operations associate director Ray Lund notes that tyre manufacturing comes with stringent quality and safety requirements
JORDAN SMITH AES Gauteng regional manager Jordan Smith and AES operations associate director Ray Lund work closely with rubber belting and tyre manufacturers in Gauteng and the Eastern Cape
There is a strong drive in and among rubber companies to exchange fossil fuels for renewable-energy sources, says steam and boiler service provider Associated Energy Services (AES).
AES Gauteng regional manager Jordan Smith and AES operations associate director Ray Lund work closely with rubber belting and tyre manufacturers in Gauteng and the Eastern Cape, and stress that, for decades, South Africa’s rubber has been a major material used in both the mining and automotive sectors.
Now, with increasing pressure to address energy use and optimisation within the industry, AES’ intervention as an operations and maintenance service provider, could be “a game changer”, they say.
Steam for Vulcanisation
Steam plays an essential role in vulcanisation, an integral process at the heart of manufacturing of all rubber products, which range from tyres and conveyor belts to sealing components, such as gaskets, or protective wear such as wetsuits or gum boots.
With the application of steam, raw natural and synthetic rubber is transformed into its final durable, yet elastic, form.
During tyre manufacture the green tyre is placed in a mould, into which highly pressurised steam is fed. This vulcanises the tyre in the curing machine, where its parts are compressed together, giving the tyre its final shape and durable qualities.
Lund notes that tyre manufacturing comes with stringent quality and safety requirements: “This means that good control of the steam and heat energy is required when a tyre is being cured.”
A press system is used to manufacture rubber belts through the process of steam heating, which provides the pressure and temperature necessary to bond and cure the components.
Smith points out that steam provides a consistent source of heat: “If the steam temperature drops and does not heat all sections of the plates equally, that results in a poorly bonded product which will not deliver the required strength and durability.”
He explains that when there is excess temperature and pressure, the belt produced is too brittle.
When Sustainability is a Stretch
Although rubber production has changed very little over the years, the sector is now facing many challenges. Ever-increasing cost pressures – coupled with an industry move to greener suppliers – has driven the need for innovation.
Rubber manufacturers with global parent companies are at the forefront of this transformation, which entails striking a balance between the social and governance commitments of a multinational and South Africa’s often harsh economic challenges.
Change must be carefully managed to ensure long-term sustainability and not put businesses at risk.
Lund elaborates that a fuel switch does, inevitably, necessitate substantial capital investment if clients want to run their plants effectively, efficiently and competitively.
He adds a large amount of capital expenditure is needed to realise those gains.
Lund points out that, generally, the technology required to burn biomass efficiently can be more expensive, adding that, as more companies convert to biomass and demand grows, so too may the cost thereof.
Unfortunately, there is a view that, because biomass is waste, it should be inexpensive, however, it has been found that locally owned rubber sector companies are very challenged by the capital investment required and the costs entailed.
“Owing to global economic, social and governance commitments, international counterparts are more inclined to consider workable solutions,” Smith observes.
A Phased Approach
Smith and Lund both favour a long-term, phased approach that AES typically recommends to clients in the rubber sector.
This begins with the ‘low-hanging fruit’ of quicker gains from optimising the performance of existing plant and processes, which ultimately clears the way for a switch to renewables further down the line.
Taking the phased approach has been successful, and AES has a proven track record of delivering substantial energy optimisation-related improvements, assisting a rubber sector client to reduce its carbon dioxide emissions and coal consumption by an impressive 11.03% with zero capital investment.
Smith attributes this to AES effectively leveraging economies of scale, doing cost-effective procurement of the correct quality coal and spares for maintenance, and individually assessing each client’s site to determine bespoke improvements and savings.
Further to this, well-trained and operationally skilled staff on site 24/7 are key in successfully driving energy plant improvements.
“We have the expertise to ensure the best set-up and operation of the steam reticulation and energy plant on our clients’ sites,” he says.
Additionally, many businesses are looking for that extra percentage gain in efficiency and partnering with AES is an effective way of unlocking that improvement.
With input cost and energy efficiency – and even carbon emission tax savings – the rubber sector can make the much-needed transition from dependence on fossil fuels, Lund continues.
He says AES would like to encourage rubber sector companies to optimise their energy usage through a strategic partnership with AES.
“We can get them ‘bouncing back’ and on the road to energy optimisation and sustainability,” he concludes.
Comments
Press Office
Announcements
What's On
Subscribe to improve your user experience...
Option 1 (equivalent of R125 a month):
Receive a weekly copy of Creamer Media's Engineering News & Mining Weekly magazine
(print copy for those in South Africa and e-magazine for those outside of South Africa)
Receive daily email newsletters
Access to full search results
Access archive of magazine back copies
Access to Projects in Progress
Access to ONE Research Report of your choice in PDF format
Option 2 (equivalent of R375 a month):
All benefits from Option 1
PLUS
Access to Creamer Media's Research Channel Africa for ALL Research Reports, in PDF format, on various industrial and mining sectors
including Electricity; Water; Energy Transition; Hydrogen; Roads, Rail and Ports; Coal; Gold; Platinum; Battery Metals; etc.
Already a subscriber?
Forgotten your password?
Receive weekly copy of Creamer Media's Engineering News & Mining Weekly magazine (print copy for those in South Africa and e-magazine for those outside of South Africa)
➕
Recieve daily email newsletters
➕
Access to full search results
➕
Access archive of magazine back copies
➕
Access to Projects in Progress
➕
Access to ONE Research Report of your choice in PDF format
RESEARCH CHANNEL AFRICA
R4500 (equivalent of R375 a month)
SUBSCRIBEAll benefits from Option 1
➕
Access to Creamer Media's Research Channel Africa for ALL Research Reports on various industrial and mining sectors, in PDF format, including on:
Electricity
➕
Water
➕
Energy Transition
➕
Hydrogen
➕
Roads, Rail and Ports
➕
Coal
➕
Gold
➕
Platinum
➕
Battery Metals
➕
etc.
Receive all benefits from Option 1 or Option 2 delivered to numerous people at your company
➕
Multiple User names and Passwords for simultaneous log-ins
➕
Intranet integration access to all in your organisation