Rubber company innovates to meet industry challenges
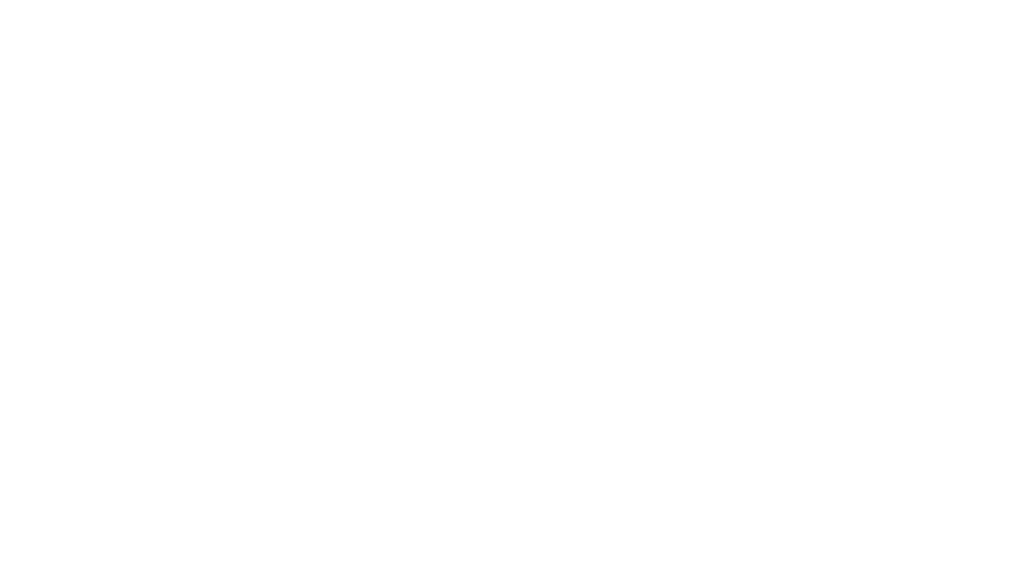

WAYNE TOZER AND SUE SUPASAR RPM aims to limit imports by manufacturing products locally where possible
High levels of unemployment, raw material shortages and energy constraints have negatively affected the South African rubber manufacturing industry as the economy begins to recover from the effects of the Covid-19 lockdown, says rubber manufacturer Rubber Products and Mouldings (RPM) director Wayne Tozer.
He explains that the continuous power outages are disruptive to the manufacture of rubber moulded products as they require longer setup times.
While RPM has introduced generators to provide backup power for some of its machinery during loadshedding, some machines are unable to operate on generator power, as they are power intensive.
Hence, the company introduced flexible production hours by operating during times outside of loadshedding.
“We are a small entrepreneurial company, we are able to manoeuvre quickly and make decisions and changes at short notice as required to meet our customer needs,” Tozer adds.
Moreover, he identifies two other primary challenges in the industry – raw material price volatility and global shortages of raw materials used in certain rubber compounds.
RPM has been partnering with UK rubber compound manufacturer Hexpol since 2019 to buy its specialised rubber compounds. This has assisted RPM in avoiding supply shortages owing to Hexpol’s buying power.
“We roll with the punches and we mitigate wherever we can. We try to buffer the price movements between ourselves and our customers by purchasing stock for extended periods to reduce price volatility,” says Tozer.
Further uncertainties in the rubber moulding market – fostered by lockdown and the subsequent transport and logistics issues – meant that companies battled to import goods and find containers. This, in turn, increased transportation costs of imported products.
As a result, some companies sought to procure rubber moulded products locally and, owing to its custom-moulding offerings, RPM assisted clients with their rubber needs.
“Having our own manufacturing facility – which supplies our retail store – ensures that our stocks are kept optimal at all times,” says Tozer.
He adds that the local rubber moulding industry is often subjected to competition from imported products, which poses a risk to the South African economy by limiting employment opportunities.
Hence, RPM aims to limit imports by manufacturing products locally where possible.
RPM director Sue Supasar adds that, while the rubber manufacturing industry took a knock during lockdown, with many companies closing down, RPMs manufacturing capacity increased and, as a result, the company was able to employ more people.
To further localise manufacturing, RPM released its 25 kg rubber saddle used to transport steel coils.
While the product was initially imported into South Africa, RPM now manufactures it locally after having conducted research and development, trials and extensive product testing before releasing it into the local market in late 2020. RPM is the exclusive manufacturer of this rubber saddle in South Africa.
The company has also added a polyurethane section to its business, with additional products and developments in the pipeline.
RPM aims to ensure that rubber remains relevant in the manufacturing industry by producing high-quality products locally.
Tozer, therefore, notes that the industry remains “fairly buoyant” despite challenges.
“While it is not always easy to produce high-quality products while remaining cost competitive, we aim to maintain this standard. If we continue on the growth path that we have been on for the past four years, then we will continue to create significantly more employment over the next four years,” he concludes.
Comments
Press Office
Announcements
What's On
Subscribe to improve your user experience...
Option 1 (equivalent of R125 a month):
Receive a weekly copy of Creamer Media's Engineering News & Mining Weekly magazine
(print copy for those in South Africa and e-magazine for those outside of South Africa)
Receive daily email newsletters
Access to full search results
Access archive of magazine back copies
Access to Projects in Progress
Access to ONE Research Report of your choice in PDF format
Option 2 (equivalent of R375 a month):
All benefits from Option 1
PLUS
Access to Creamer Media's Research Channel Africa for ALL Research Reports, in PDF format, on various industrial and mining sectors
including Electricity; Water; Energy Transition; Hydrogen; Roads, Rail and Ports; Coal; Gold; Platinum; Battery Metals; etc.
Already a subscriber?
Forgotten your password?
Receive weekly copy of Creamer Media's Engineering News & Mining Weekly magazine (print copy for those in South Africa and e-magazine for those outside of South Africa)
➕
Recieve daily email newsletters
➕
Access to full search results
➕
Access archive of magazine back copies
➕
Access to Projects in Progress
➕
Access to ONE Research Report of your choice in PDF format
RESEARCH CHANNEL AFRICA
R4500 (equivalent of R375 a month)
SUBSCRIBEAll benefits from Option 1
➕
Access to Creamer Media's Research Channel Africa for ALL Research Reports on various industrial and mining sectors, in PDF format, including on:
Electricity
➕
Water
➕
Energy Transition
➕
Hydrogen
➕
Roads, Rail and Ports
➕
Coal
➕
Gold
➕
Platinum
➕
Battery Metals
➕
etc.
Receive all benefits from Option 1 or Option 2 delivered to numerous people at your company
➕
Multiple User names and Passwords for simultaneous log-ins
➕
Intranet integration access to all in your organisation