Smelting project leads to shift in company directors
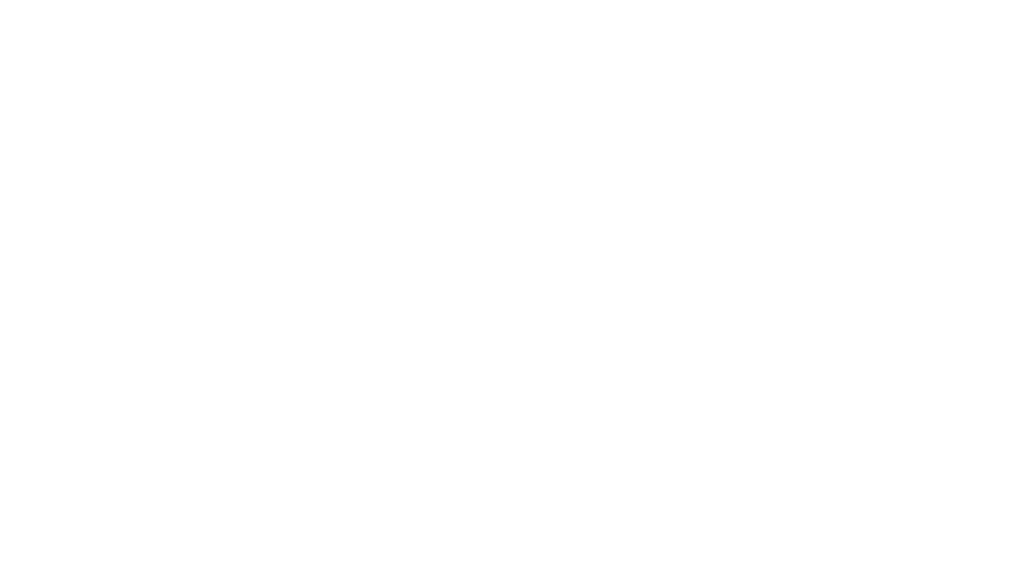
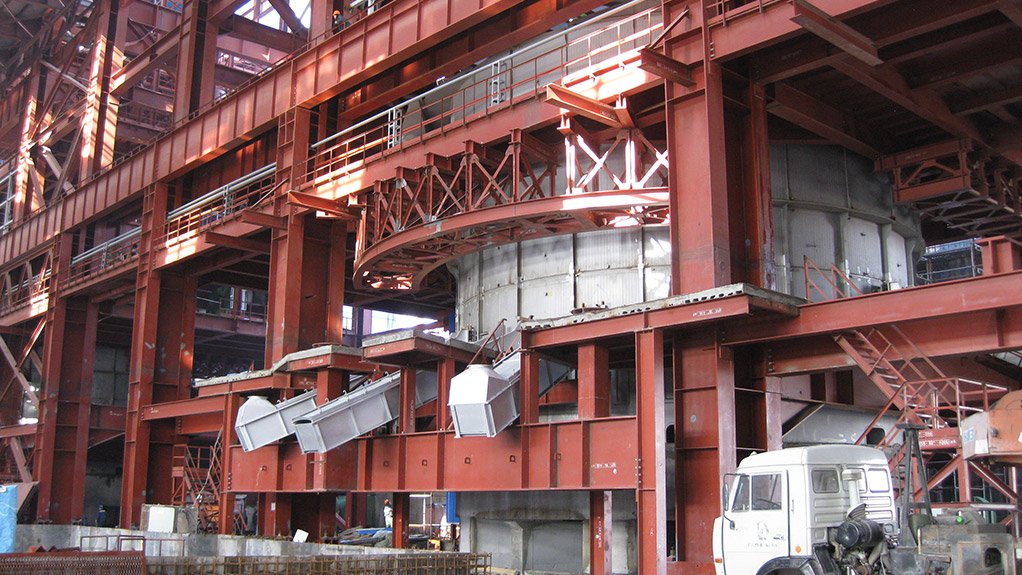
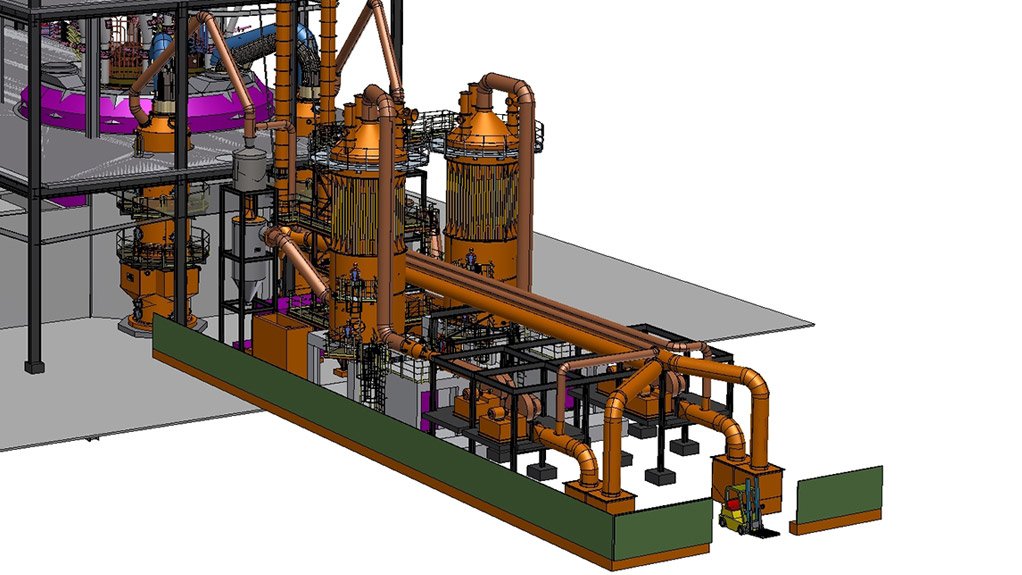
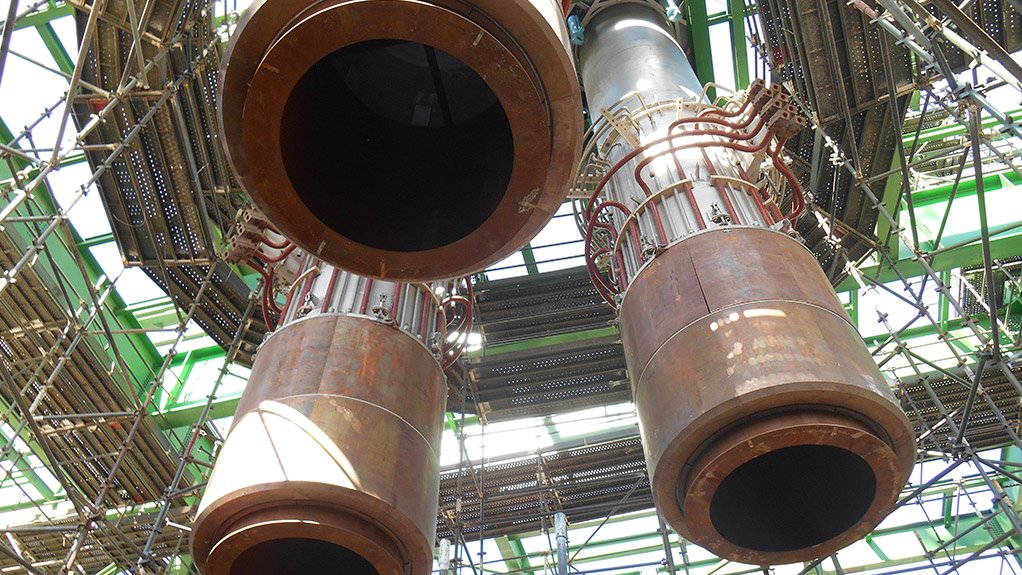
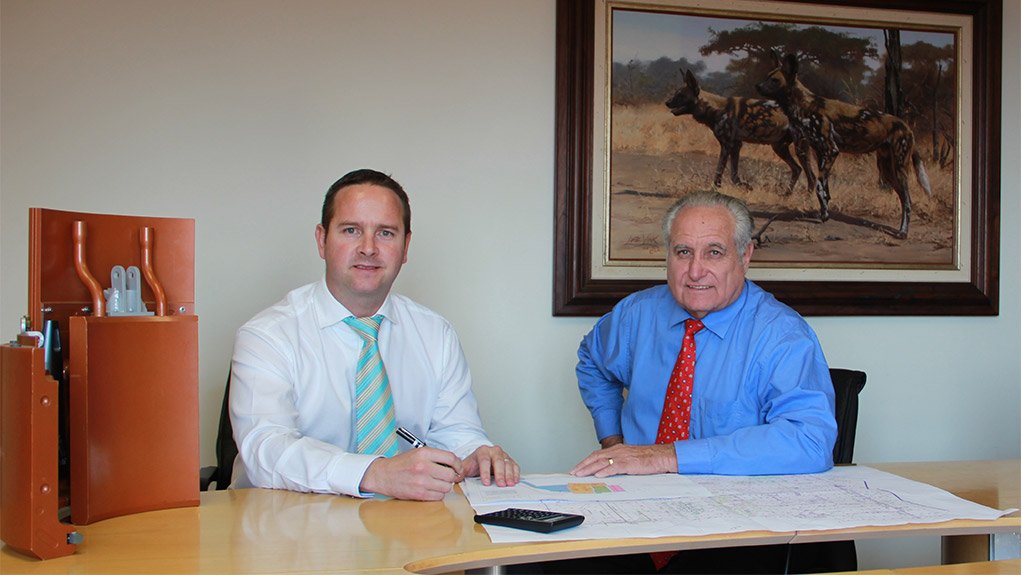
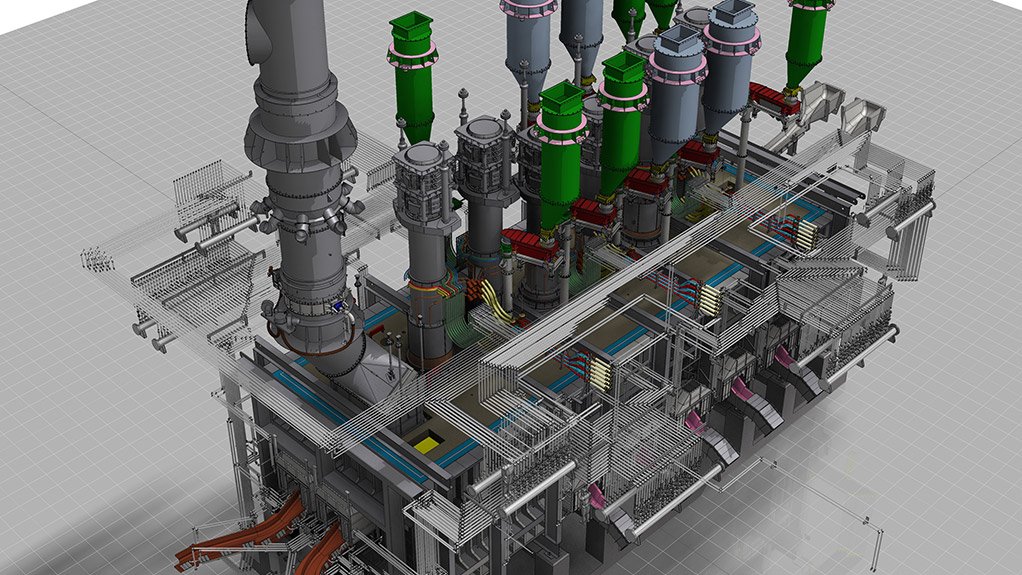
KAZCHROME WORKS PROJECTThe project, which began in 2011, includes the construction of four 72 MW direct current furnaces for the smelting of ferrochrome
GAS CLEANINGSMS Siemag’s duty standby venturi gas cleaning scrubber with advanced goose neck, quencher and wet electrostatic precipitator
NEW TECHNOLOGY The bottom electrodes with forged copper contact shoes, pressure rings and heat shields
DIRECTOR CHANGE As of last month, Andrew van Niekerk replaced Reinier Meyjes as Metix MD, as Meyjes, who was appointed Metix director, will focus on the Sakura smelting project in Sarawak, Malaysia
RECTANGULAR FURNACEThe range includes six-inline large-capacity furnaces that are 135 MVA for iron/nickel alloys
Smelter engineering firm Metix, a subsidiary of German group SMS Siemag, is undertaking the Sakura smelting project, in Sarawak, Malaysia, which has resulted in a reshuffle of its upper ranks.
As of last month, Andrew van Niekerk replaced Reinier Meyjes as MD. Meyjes was appointed as Metix director and will focus on the Sakura project.
Metix is undertaking the detailed design and supply of furnaces as well as the supply of new technology from SMS Siemag to Sakura. The project will include two 81 MVA ferromanganese and silico- manganese closed furnaces and associated gas cleaning, raw material handling, product handling, associated services and infrastructure.
The project will be Meyjes’ main focus until its expected commissioning at the end of 2015. At the same time he aims to provide Metix employees with training on the technical aspects of furnace design.
Van Niekerk hopes to build on the strong base Meyjes has created as MD and hopes to swiftly enter new markets such as platinum, pig iron, slag cleaning, direct current (dc) furnaces, gas cleaning, cogeneration and prereduction.
These markets will be made accessible through the SMS Siemag group’s processes and technologies.
“Reinier and I have always worked as a team and it is nice to move forward from a basis of familiarity for the next few years. My new role entails leading, motivating and managing the Metix board, executive committee and employees to improve our local position and expand our presence in sub-Saharan Africa,” he states.
The company has already implemented new technologies and products that have extended its reach, into Malaysia, Zambia, Zimbabwe and China.
Van Niekerk hopes to ensure rank changes are implemented successfully while maintaining current business relationships with clients in South Africa.
He has been on the Metix board of directors for ten years and has a vast background and experience, ranging from project costing and engineering principles to the handing over of newly built plants. He hopes to use this knowledge to work with industry partners to accurately deliver cost-competitive plants.
Van Niekerk notes that he is looking forward to interacting with the company’s German counterparts and the exposure he will have to various cultures worldwide to build new partnerships and create new business opportunities for the company.
“While I have many hopes for the company, the most important is to stay true to ourselves and the wishes of the SMS Siemag group chairperson Heinrich Weiss, who said: ‘When a client is in need we do not send lawyers, we send engineers.’ I hope that Metix can deliver on that for the sake of our shareholders, industry and, more importantly, our clients,” Van Niekerk states.
New Technologies
Several new Metix technologies are being used successfully at various projects worldwide. The first of these technologies is a rectangular furnace, which Metix has incorporated into design concepts, engineering specifications and design draughting, with the help of its German counterparts.
The rectangular furnace range includes smaller three-inline or 12 MVA furnaces for copper slag cleaning to six-inline large-capacity furnaces that are 135 MVA for iron/nickel alloys processing.
SMS Siemag has supplied rectangular furnaces to various industries in Brazil, Zambia and Kazakhstan. Further, a 24 MVA matte settling furnace is under construction for base metals miner First Quantum Minerals as part of its major expansion at the Kansanshi copper smelter near Solwezi, in Zambia. The project began in March last year and the commissioning will start in 2014.
Van Niekerk says, to date, all equipment has been ordered and is either in transit or already on site.
First Quantum Minerals is undertaking the installation with Metix supervision. Van Niekerk says it has been exciting and educational to work with a client that knows how SMS Siemag technology functions and that has completed two projects based on the technology.
“Various improvements have been incorporated in the rectangular surface technology, including forged copper launders and tapholes; height-adjustable tapholes; improved safety on cooling water channels; and medium, higher matte flow rates; a longer expected life span; and various proven furnace- and process-control measures. We have so much to look forward to in supplying this technology, especially its application in the platinum, ilmenite and pig iron industries,” he states.
Slag Cleaning
SMS Siemag is working on a new, innovative and intensive slag-cleaning stage. This new development deals with the challenge of finely dispersed smaller precious- metal droplets that do not gravitationally settle into the matte or metal phase of the furnace.
Van Niekerk states that the new invention is an attractive solution, especially for the copper and platinum metals industry.
In copper slag cleaning, the copper content of the slag can be further reduced from about 0.5% to 0.2%.
“The small channel-type unit has a permanent dc field, combined with a magnetic field. In the first zone of the furnace, the slag is electromagneti- cally stirred, causing partial coagulation of the smaller metal droplets. In the second zone, the droplets are forced by capillary motion into the metal or matte phase and additional electro- lytic effects increase the metal recovery rate. This process is patented for all metals,” Van Niekerk explains.
DC Furnaces
SMS Siemag is completing a major expansion of global diver- sified mining group Eurasian Natural Resources Corporation’s (ENRC’s) Kazchrome works at Aktobe, in Kazakhstan.
The project, which began in 2011, includes the construction of four 72 MW dc furnaces for the smelting of ferrochrome. The yearly production of the plant will be about 440 000 t/y of high-carbon ferrochrome.
Van Niekerk says an interactive design phase with ENRC’s existing dc operations know-how and SMS Siemag’s experience in dc projects, ensured the application of tested and the development of much-needed new technologies.
These technologies include improved thermal efficiency, air-cooled refractory roofs, arc-deflection control, a high-speed thyristor ignition controller and on-power electrode additioning.
SMS Siemag holds patents for the use of an electrode column system that enables the operator to control the electrode under full power, significantly increasing production levels. Further, an in-house design tool provides reduced arc deflection, which increases the life of the lining.
Similar to the rectangular technology, Metix has studied and priced various plant sizes, such as those ranging from 5 MW to multiple 75 MW furnaces for ferrochrome, ilmenite, pig iron and platinum-group metals.
SMS Siemag is also considering the use of rotary hearth furnaces as a prereduction step for ferro- nickel and ferrochrome smelting to improve energy efficiency.
First demonstration-scale tests show potential electricity savings of more than 50% in the electrical smelter while using prereduced hot chromium-ore agglomerates.
Tests were conducted in two demonstration plants and results show that, depending on the location, the combination of rotary hearth furnace and submerged-arc furnace processes may become a competitive alternative to conventional process combinations currently on the market.
The company is also testing different technologies for preheating, which should provide its clients with energy savings of between 10% and 50%, and which could be retrofitted to existing-furnace building layouts and feed systems.
Metix also offers carbon monoxide-rich gas cleaning of closed furnaces. The cleaning units range from 12 000 Nm3/h to 150 000 Nm3/h and have been supplied to various converter plants.
The company’s latest offering includes full-duty and standby functions for each furnace, four cleaning stages, a wet electrostatic precipitator and advanced furnace pressure control with sufficient distribution pressure.
SMS Siemag also focuses on cogeneration technologies to deal with South Africa’s power shortages.
“We have invested many years in developing technologies for cogeneration and heat recovery that can be applied to all types of furnaces to recover between 15% and 30% of energy input. These include heat recovery boilers for hot-gas and cogene- ration plants on converters for carbon monoxide-rich gas cleaning, storage and burners,” Van Niekerk explains.
Refining Technology for Ferrochromium and Ferromanganese
SMS Siemag has years of experience in converter technology and its current design covers converters with fluid flow models, improved with computational fluid dynamics, as well as detailed parameter studies covering vessel geometry, stirring rate and the number and dia- meter of pouring plugs.
“Our range of converters includes conventional basic oxygen furnace converters for ferronickel and argon oxygenated decarburisation (AOD) converters for the production of medium carbon ferromanganese and medium carbon ferrochromium. Most recently, we developed and proved the feasibility of an industrial- scale-application carbon dioxide-blowing technology in an AOD vacuum converter for medium carbon ferro- chromium with less than 1% of carbon,” Van Niekerk explains.
This technology significantly cuts operation costs and the need for expensive cooling materials, with a chromium yield of 95.5% achieved during testing.
Comments
Announcements
What's On
Subscribe to improve your user experience...
Option 1 (equivalent of R125 a month):
Receive a weekly copy of Creamer Media's Engineering News & Mining Weekly magazine
(print copy for those in South Africa and e-magazine for those outside of South Africa)
Receive daily email newsletters
Access to full search results
Access archive of magazine back copies
Access to Projects in Progress
Access to ONE Research Report of your choice in PDF format
Option 2 (equivalent of R375 a month):
All benefits from Option 1
PLUS
Access to Creamer Media's Research Channel Africa for ALL Research Reports, in PDF format, on various industrial and mining sectors
including Electricity; Water; Energy Transition; Hydrogen; Roads, Rail and Ports; Coal; Gold; Platinum; Battery Metals; etc.
Already a subscriber?
Forgotten your password?
Receive weekly copy of Creamer Media's Engineering News & Mining Weekly magazine (print copy for those in South Africa and e-magazine for those outside of South Africa)
➕
Recieve daily email newsletters
➕
Access to full search results
➕
Access archive of magazine back copies
➕
Access to Projects in Progress
➕
Access to ONE Research Report of your choice in PDF format
RESEARCH CHANNEL AFRICA
R4500 (equivalent of R375 a month)
SUBSCRIBEAll benefits from Option 1
➕
Access to Creamer Media's Research Channel Africa for ALL Research Reports on various industrial and mining sectors, in PDF format, including on:
Electricity
➕
Water
➕
Energy Transition
➕
Hydrogen
➕
Roads, Rail and Ports
➕
Coal
➕
Gold
➕
Platinum
➕
Battery Metals
➕
etc.
Receive all benefits from Option 1 or Option 2 delivered to numerous people at your company
➕
Multiple User names and Passwords for simultaneous log-ins
➕
Intranet integration access to all in your organisation