South African delegates hear of Thailand's consistently adapted automotive support policy
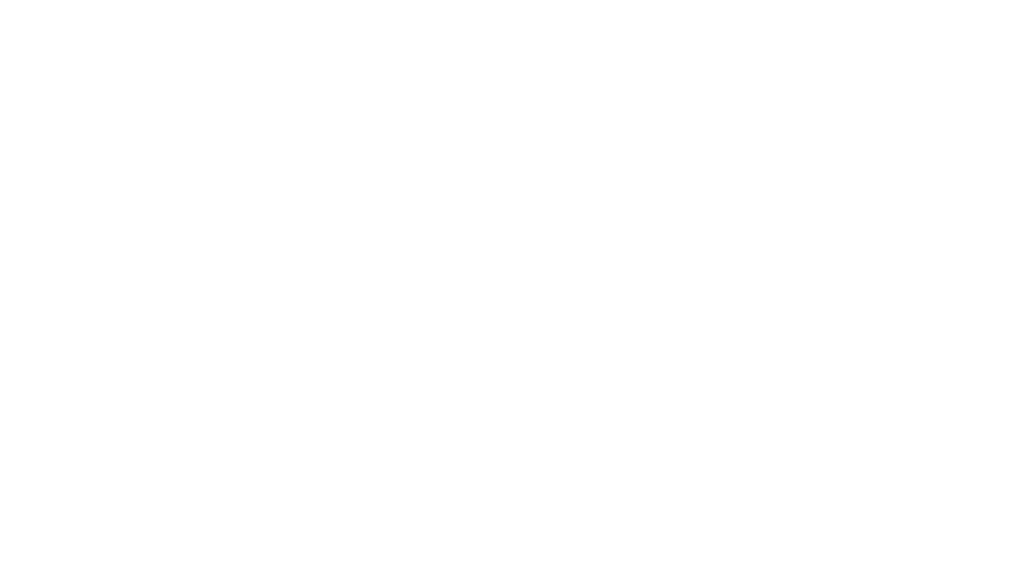
Thammasat University Faculty of Economics associate Professor Kriengkrai Techakanont tells delegates at a seminar hosted by NAACAM and TWIMS about the policy decisions that have helped to grow Thailand's automotive industry. Video and editing: Shadwyn Dickinson.
Thailand has a national automotive industry policy committee, which includes private-sector and government representatives, that deliberates and then puts in place fixed-term incentives to drive private-sector companies to transition in the agreed-upon direction.
This was informed by the effect that the local assembly of pickup trucks had on the country's automotive sector, in particular in driving the development of components and parts suppliers in the sector, Thammasat University Faculty of Economics Associate Professor Kriengkrai Techakanont told delegates attending a seminar hosted by industry organisation the National Association of Automotive Component and Allied Manufacturers and nonprofit initiative the Toyota Wessels Institute for Manufacturing Studies (TWIMS) on October 1.
Techakanont said the Thai automotive industry had been shaped by consistent policy.
TWIMS ambassador and University of Pretoria's Gordon Institute of Business Science Associate Professor, Justin Barnes, noted that, like South Africa, Thailand does not have indigenous car manufacturer brands and developed as part of the production legs of the global production network.
"The difference is that Thailand has managed to move closer to the core of the global production value chain and established itself as a major partner of multinational investors for producing and consolidating production of particular types of technology in the global value chain."
Thailand's automotive sector is about three times larger than South Africa's and employs about four times as many people as the local industry, but both started at similar levels in the 1990s.
South Africa's automotive sector had struggled to reposition itself and was not in the same strong position as Thailand's industry, hence the value of studying Thailand's progress – especially as it was also a developing nation, he added.
By the turn of the century, Thailand was ranked among the 20 biggest countries in terms of cars manufactured, and the government set a target for the country to be among the top ten within 20 years, said Techakanont.
Consistent policy support, mainly in the form of fixed-term and well-defined incentives, contributed to it being ranked eleventh in global cars made in 2018 and, although production is lower than its peak of 2.4-million units produced a year, it currently produces about 1.8-million vehicles a year.
"It took about three decades for us to find the right ingredients for moving with the changes in global markets," he noted.
Thailand managed to scale up its automotive sector more substantially than South Africa and managed to deepen the local value addition and jobs gained from the presence of the sector, said Barnes.
The supply side of the industry was developed during the first three decades of its automotive production, up to the 1990s,and has become rooted in Thailand, said Techakanont.
"This is how we will be able to scale up and catch up with global trends of carbon neutrality and new-energy vehicles (NEVs). When looking at developing the automotive value chain, it must start with research and development (R&D).
"Thailand started at the lowest value addition in terms of automotive manufacturing but has managed to climb up the value chain into engineering and R&D. We did not originally have manufacturing capacity, but we had some parts suppliers," he said.
Now, the country serves several car markets, and parts suppliers are investing in R&D in Thailand, with some multinational brands already using the country to carry out pilot production runs.
Additionally, while most of the first-tier suppliers were subsidiaries of automotive manufacturers or joint ventures, there were also some Thai suppliers in the first-tier and there continued to be investment in parts production in Thailand, Techakanont said.
Specifically, Thailand provides incentives for parts suppliers independently of incentives for automotive manufacturers, including for NEV parts and components manufacturers, which helps to support the gradual transition of this part of the sector.
It then also provides a range of incentives for the local manufacturing of vehicles. It requires that automotive manufacturers applying for incentives commit to fixed production targets within well-defined time frames, and that a certain percentage of their vehicles produced must be NEVs, typically 30%.
"The challenge for South Africa is that local assembly is critical for a local supply chain. However, the value of the industry in the country is derived from the value chain, and there would be no supply chain without assembly.
"Vehicle assembly drives the value from the supply chain and the components side of the industry will be important as we transition to NEVs," emphasised Barnes.
THAI STRATEGY
Using a competitive advantage defining strategy, Thailand had decided that it lacked the engineering resources and R&D capabilities to lead on the frontiers of new automotive technology and, therefore, decided to adopt a strategy of following automotive technology development, said Techakanont.
"We rather took the comparative advantage of following, based on our endowments of labour and natural resources. The industry was developed through this channel. We started with simple production and then localisation and then plugging into the global value chain, as we grow our engineering capabilities."
Thailand uses excise tax as its incentives instrument, with conventional internal combustion engine (ICE) cars being subjected to a 25% excise tax, while more efficient cars are subjected to a 12% to 14% excise tax and NEVs are subjected to only an 8% excise tax.
This made the price of battery electric vehicles, for example, comparable to ICE cars in the same market segment, he noted.
"We use incentives to encourage firms that are standing still to move. Thailand aims to make it easy for companies to decide whether to commit or not to new investments based on the potential incentives they will receive," he said.
The incentives are generous, with up to 150 000 Thai Baht provided to automotive manufacturers making NEVs, which enables these companies to sell NEVs at a price of 850 000 Thai Baht. This is comparable to the price of more efficient cars.
This has driven adoption in the local market, which now has more than 6 000 electric vehicle charging points. This incentive has also attracted car makers, with five Chinese car makers currently invested in the country since 2022, of which three are already producing vehicles and the further two will start producing in 2025.
Thailand's incentives require that manufacturers commit to production targets and that they must produce at least one vehicle in Thailand for every vehicle they import to enter the market.
This had enabled one car manufacturer to boost sales up to almost 100 000 units a year of NEVs, but it must start producing one vehicle in Thailand for each imported during the next year or, if it delayed, it must produce 1.5 vehicles in Thailand for each vehicle imported, he illustrated.
This format of providing greater incentives for early movers helps to cover their risks while also affording other manufacturers the chance to start manufacturing when they are ready, encouraging foreign direct investment and the associated changes in parts production over time.
The country was strict with manufacturers, with those not meeting targets losing incentives and being penalised and/or fined, he noted.
"The right ingredients for Thailand were policy flexibility but consistency. We adopted rationalisation for localisation targets, which allowed investors to be informed before they built. This created a deepening in the Thai automotive value chain."
Comments
Press Office
Announcements
What's On
Subscribe to improve your user experience...
Option 1 (equivalent of R125 a month):
Receive a weekly copy of Creamer Media's Engineering News & Mining Weekly magazine
(print copy for those in South Africa and e-magazine for those outside of South Africa)
Receive daily email newsletters
Access to full search results
Access archive of magazine back copies
Access to Projects in Progress
Access to ONE Research Report of your choice in PDF format
Option 2 (equivalent of R375 a month):
All benefits from Option 1
PLUS
Access to Creamer Media's Research Channel Africa for ALL Research Reports, in PDF format, on various industrial and mining sectors
including Electricity; Water; Energy Transition; Hydrogen; Roads, Rail and Ports; Coal; Gold; Platinum; Battery Metals; etc.
Already a subscriber?
Forgotten your password?
Receive weekly copy of Creamer Media's Engineering News & Mining Weekly magazine (print copy for those in South Africa and e-magazine for those outside of South Africa)
➕
Recieve daily email newsletters
➕
Access to full search results
➕
Access archive of magazine back copies
➕
Access to Projects in Progress
➕
Access to ONE Research Report of your choice in PDF format
RESEARCH CHANNEL AFRICA
R4500 (equivalent of R375 a month)
SUBSCRIBEAll benefits from Option 1
➕
Access to Creamer Media's Research Channel Africa for ALL Research Reports on various industrial and mining sectors, in PDF format, including on:
Electricity
➕
Water
➕
Energy Transition
➕
Hydrogen
➕
Roads, Rail and Ports
➕
Coal
➕
Gold
➕
Platinum
➕
Battery Metals
➕
etc.
Receive all benefits from Option 1 or Option 2 delivered to numerous people at your company
➕
Multiple User names and Passwords for simultaneous log-ins
➕
Intranet integration access to all in your organisation