Steam trap provides solution to condensate problems
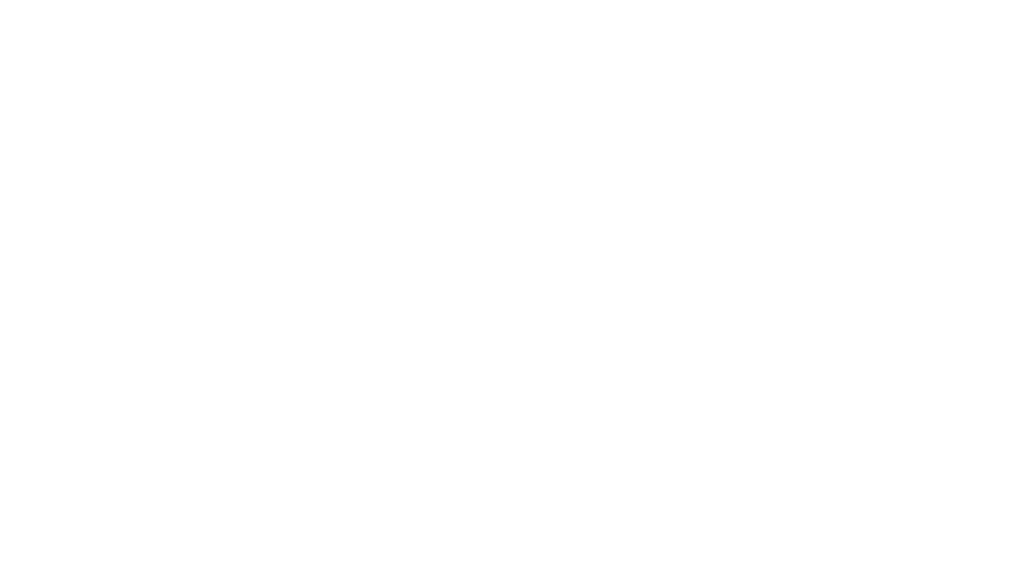
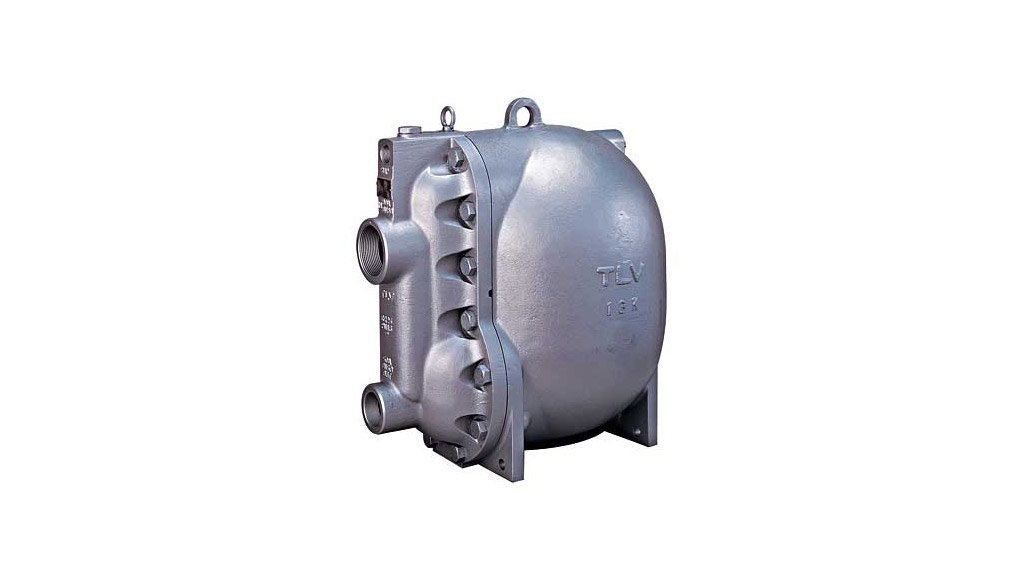
IMPROVED PRODUCTIVITY The Powertrap GT10 reduces steam usage in industry heat exchangers
The ability of valves supplier Heaton Valves’ Powertrap GT10 to improve production by removing condensate from steam systems where stall may occur makes it an increasingly popular solution for the petrochemicals, food and beverage and motor industries, which are experiencing problems with heat-exchanger stall, the company says.
The Powertrap GT10 – a condensate pump with a built-in steam trap – is manufactured by Japan-based valves manufacturer TLV and distributed locally by Heaton Valves.
“The main function of the GT10 is to remove condensate from steam systems under stall conditions,” the company says, explaining that the Powertrap functions as a steam trap when there is a positive pressure differen- tial across the heat exchanger, or as a pump when there is a negative pressure differential and stall occurs in the system.
“This continuous removal of the condensate allows for more efficient heat transfer across the heat exchanger,” the company notes.
The Powertrap GT10 can be used in the drainage of heat exchangers, and in flash steam recovery systems and nonvented receivers such as the low-pressure stages of turbines and absorption chillers, the company says.
Meanwhile, the company notes that, although it has installed about 40 Powertraps in the petrochemicals, brewing and motor industries since the product’s introduction onto the local market in the late 1990s, industry is only now starting to recognise its potential as a solution to stall.
Since the Powertrap GT10 – which is locally classified as a valve – was installed at a large petrochemicals plant, last year, the client has registered a reduction in steam use, an increase in production and energy savings, and a return on investment of three to four months.
Heaton Valves completed another Powertrap GT10 installation at the same petrochemicals plant in January and installed another at a brewing plant in a neighbouring country.
Managing Stall
Stall is often present in heat exchanger systems, reducing productivity, the company says, since “stall occurs when the necessary pressure differential across a drainage device, such as a trap, becomes negative, resulting in condensate no longer being discharged from the drainage device and, instead, to pool inside a heat exchanger”.
Stall can be identified when the system experiences problems such as ruptured heaters, water hammer or damage, or uneven heating temperatures.
Moreover, the company adds that “steam traps do not have the ability to draw out condensate on their own”, explaining that the condensate is discharged through the pressure difference between the trap inlet (primary) pressure and outlet (secondary) pressure.
“This means that the trap inlet pressure must, therefore, be higher than the trap outlet pressure to allow for proper condensate flow,” the company says.
While other solutions to condensate problems are available on the market, which include separate pump and steam trap designs, the Powertrap G10 is a multifunctional system contained in a single piece of equipment.
Features of the Powertrap include the management of high-temperature condensate without cavitation, while no electric power or additional level controls are required, which makes it intrinsically safe – an important factor for the refining industry, the company notes.
Further, the company says the GT10 Powertrap provides easy in-line access to internal components, which simplifies cleaning and reduces main- tenance costs.
The company has increased its Powertrap G10 stock and aims to install another five units this year.
Comments
Press Office
Announcements
What's On
Subscribe to improve your user experience...
Option 1 (equivalent of R125 a month):
Receive a weekly copy of Creamer Media's Engineering News & Mining Weekly magazine
(print copy for those in South Africa and e-magazine for those outside of South Africa)
Receive daily email newsletters
Access to full search results
Access archive of magazine back copies
Access to Projects in Progress
Access to ONE Research Report of your choice in PDF format
Option 2 (equivalent of R375 a month):
All benefits from Option 1
PLUS
Access to Creamer Media's Research Channel Africa for ALL Research Reports, in PDF format, on various industrial and mining sectors
including Electricity; Water; Energy Transition; Hydrogen; Roads, Rail and Ports; Coal; Gold; Platinum; Battery Metals; etc.
Already a subscriber?
Forgotten your password?
Receive weekly copy of Creamer Media's Engineering News & Mining Weekly magazine (print copy for those in South Africa and e-magazine for those outside of South Africa)
➕
Recieve daily email newsletters
➕
Access to full search results
➕
Access archive of magazine back copies
➕
Access to Projects in Progress
➕
Access to ONE Research Report of your choice in PDF format
RESEARCH CHANNEL AFRICA
R4500 (equivalent of R375 a month)
SUBSCRIBEAll benefits from Option 1
➕
Access to Creamer Media's Research Channel Africa for ALL Research Reports on various industrial and mining sectors, in PDF format, including on:
Electricity
➕
Water
➕
Energy Transition
➕
Hydrogen
➕
Roads, Rail and Ports
➕
Coal
➕
Gold
➕
Platinum
➕
Battery Metals
➕
etc.
Receive all benefits from Option 1 or Option 2 delivered to numerous people at your company
➕
Multiple User names and Passwords for simultaneous log-ins
➕
Intranet integration access to all in your organisation