Steel billet and precision casting foundry, South Africa
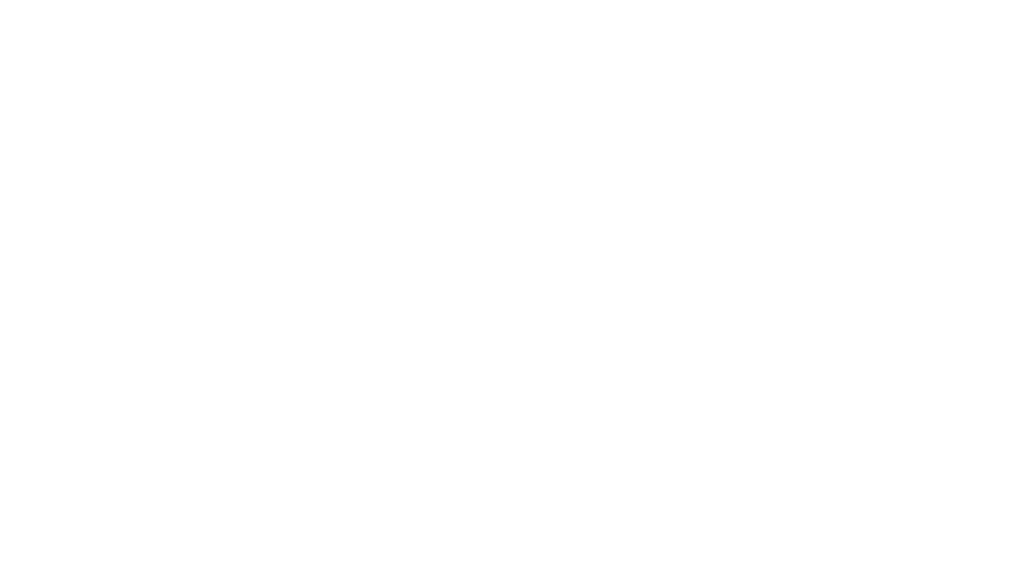
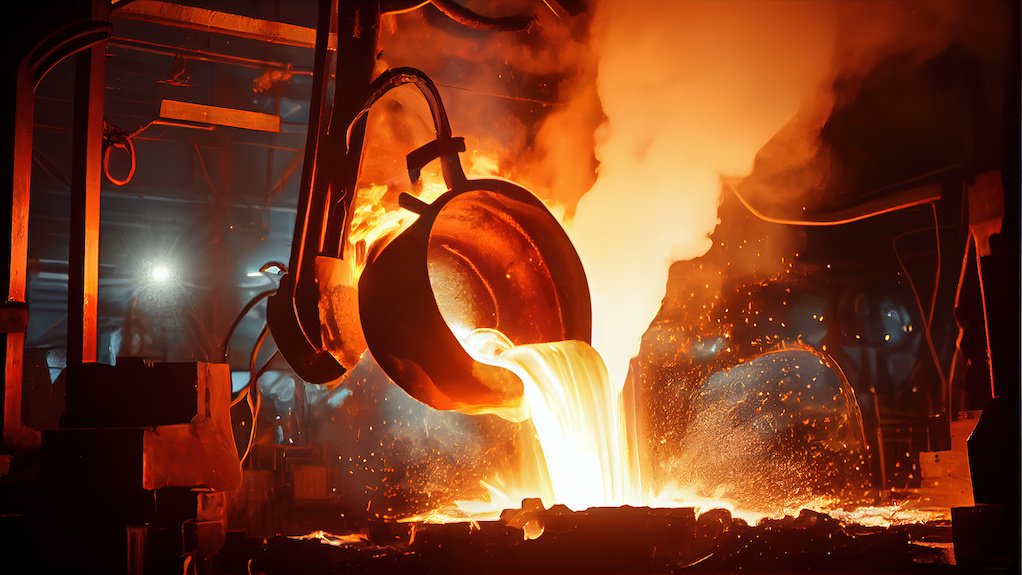
Name of the Project
Steel billet and precision casting foundry.
Location
Benoni, Gauteng, South Africa.
Project Owner/s
GeT Steel, part of the GeT Metal Group.
Project Description
A draft scoping study has proposed the refurbishment of the former Naledi Foundry.
The project will comprise two operational areas: Area A – a steel billet manufacturing foundry, and Area B – a precision casting/investment casting foundry.
Area A will process incoming raw materials at up to 15 000 t a month of scrap steel, iron and stainless steel, and produce up to 14 000 t a month total output of steel billets. The steel billet manufacturing foundry will include, inter alia:
- the refurbishment of existing buildings and infrastructure, the demolition of infrastructure, the construction of new buildings and warehouses, and the installation of key equipment.
- a raw material waste storage area.
- five electric induction furnaces (two 16 t and three 10 t) for the melting, refining and casting of scrap steel into steel billets.
- an automatic billet caster.
- a rolling mill for the conversion of semifinished casted products (billets) into finished products such as structural steel.
- air emissions abatement equipment serving the five foundry furnaces. In principle, emissions filtration will entail localised extraction, as well as building extraction, in the main foundry area, and appropriate filtration such as bag filters. The previous abatement system is in good enough condition to reuse in the foundry.
- Area B will process incoming raw materials at up to 220 t a month of scrap metals, mainly scrap metals with various additional compounds, and will produce up to 210 t a month of cast components (about 270 000 cast components). The precision casting foundry will include:
- the refurbishment of existing buildings and infrastructure, the construction of new buildings and warehouses, and the installation of key equipment.
- a raw material waste storage area.
- wax pressing to produce wax patterns (injection moulding).
- the covering of wax trees with slurry to make moulds.
- 11 electric induction furnaces ranging from 50 kg to 500 kg to melt metal to pour into ceramic moulds.
- six gas-fired bake-out ovens in the heat-treatment department to bake ceramic moulds before casting metal into them.
- slurry rotating tanks.
- two electric bake-out kilns in the melting department to heat treat the metal castings.
- the casting of ceramic moulds.
- a high-pressure, water-blasting station to remove ceramic from cast moulds.
- grinders to remove castings from feeder systems.
- straightening presses to straighten castings after heat treatment.
- electric welding machines.
- an air emissions abatement system serving the foundry furnaces, bake-out ovens and kilns. In principle, emissions filtration will entail localised extraction and building extraction in the main foundry area, as well as appropriate filtration such as bag house filters.
- shotblasting and sandblasting to remove excess ceramic from castings.
- the recycling of used wax and boiling out of impurities in electric wax reclamation tanks.
An estimated 200 000 kWh a month of electricity from Eskom will be used for the melting, refining and casting of the steel in electric induction furnaces and kilns. Municipal water will
be used.
About 900 000 ℓ of water a month will be required to service the precision casting foundry and three-million litres a month for the steel billet manufacturing foundry.
A closed water circulation system will be implemented in both areas; therefore, there will be no wastewater output.
Liquid petroleum gas (LPG) will be used to fire the gas-fired top hats in the rolling mill at the steel billet manufacturing refinery.
A maximum of 1 140 GJ a month of LPG will supply the gas-fired bake-out ovens at the precision casting foundry to fire the gas-fired top hats in the rolling mill.
Potential Job Creation
Not stated.
Capital Expenditure
Not stated.
Planned Start/End Date
Get Steel invited interested and affected parties to submit comments on the draft scoping report on the refurbishment of the Naledi Foundry in May 2024. Comments needed to be submitted before June 14.
Latest Developments
None stated.
Key Contracts, Suppliers and Consultants
None stated.
Contact Details for Project Information
GeT Metal Group, tel +27 21 853 3086 or email info@getmetalgroup.co.za.
Comments
Announcements
What's On
Subscribe to improve your user experience...
Option 1 (equivalent of R125 a month):
Receive a weekly copy of Creamer Media's Engineering News & Mining Weekly magazine
(print copy for those in South Africa and e-magazine for those outside of South Africa)
Receive daily email newsletters
Access to full search results
Access archive of magazine back copies
Access to Projects in Progress
Access to ONE Research Report of your choice in PDF format
Option 2 (equivalent of R375 a month):
All benefits from Option 1
PLUS
Access to Creamer Media's Research Channel Africa for ALL Research Reports, in PDF format, on various industrial and mining sectors
including Electricity; Water; Energy Transition; Hydrogen; Roads, Rail and Ports; Coal; Gold; Platinum; Battery Metals; etc.
Already a subscriber?
Forgotten your password?
Receive weekly copy of Creamer Media's Engineering News & Mining Weekly magazine (print copy for those in South Africa and e-magazine for those outside of South Africa)
➕
Recieve daily email newsletters
➕
Access to full search results
➕
Access archive of magazine back copies
➕
Access to Projects in Progress
➕
Access to ONE Research Report of your choice in PDF format
RESEARCH CHANNEL AFRICA
R4500 (equivalent of R375 a month)
SUBSCRIBEAll benefits from Option 1
➕
Access to Creamer Media's Research Channel Africa for ALL Research Reports on various industrial and mining sectors, in PDF format, including on:
Electricity
➕
Water
➕
Energy Transition
➕
Hydrogen
➕
Roads, Rail and Ports
➕
Coal
➕
Gold
➕
Platinum
➕
Battery Metals
➕
etc.
Receive all benefits from Option 1 or Option 2 delivered to numerous people at your company
➕
Multiple User names and Passwords for simultaneous log-ins
➕
Intranet integration access to all in your organisation