Thrilling new home-grown technology can win back South Africa’s lost ferroalloy renown
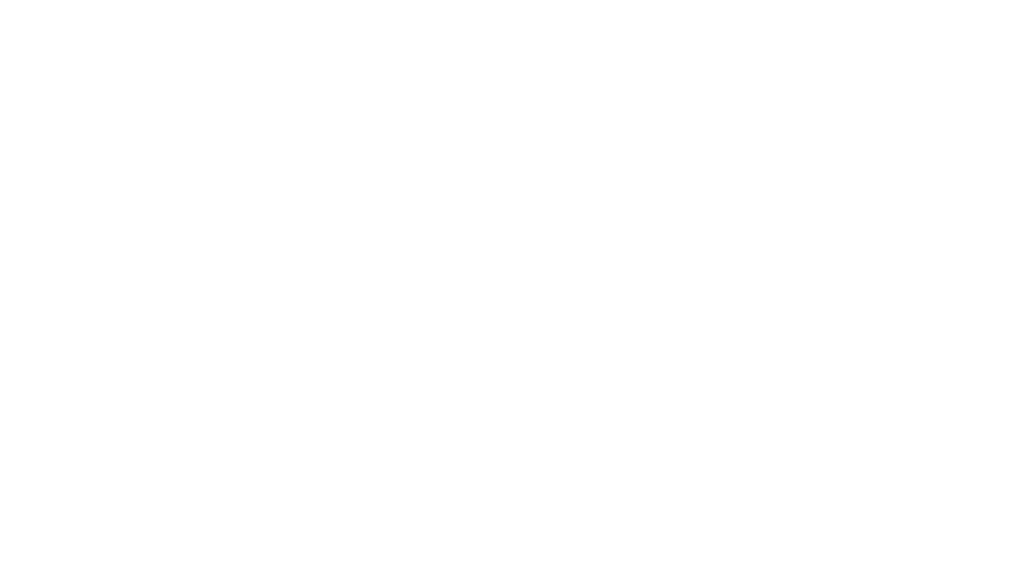
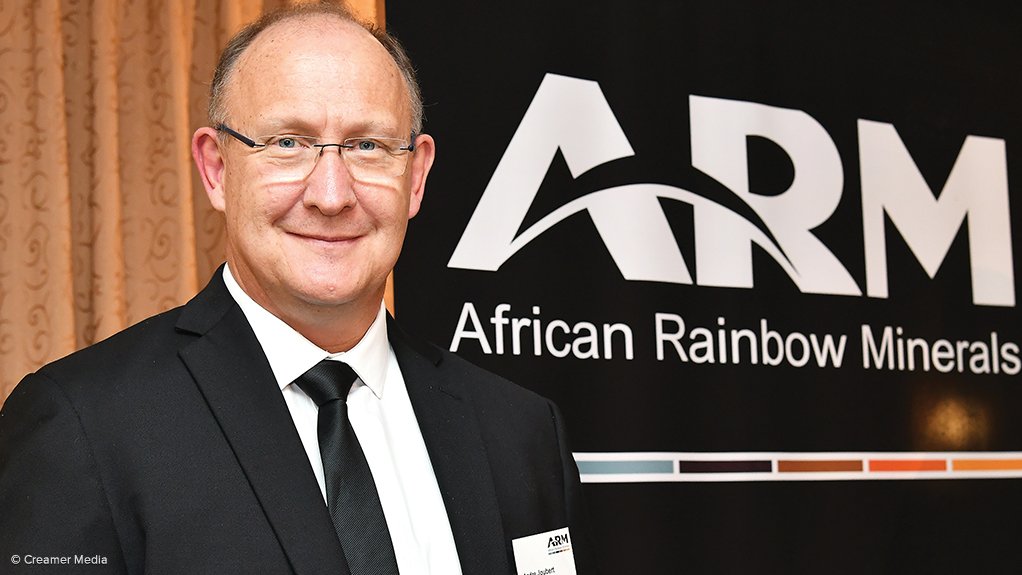
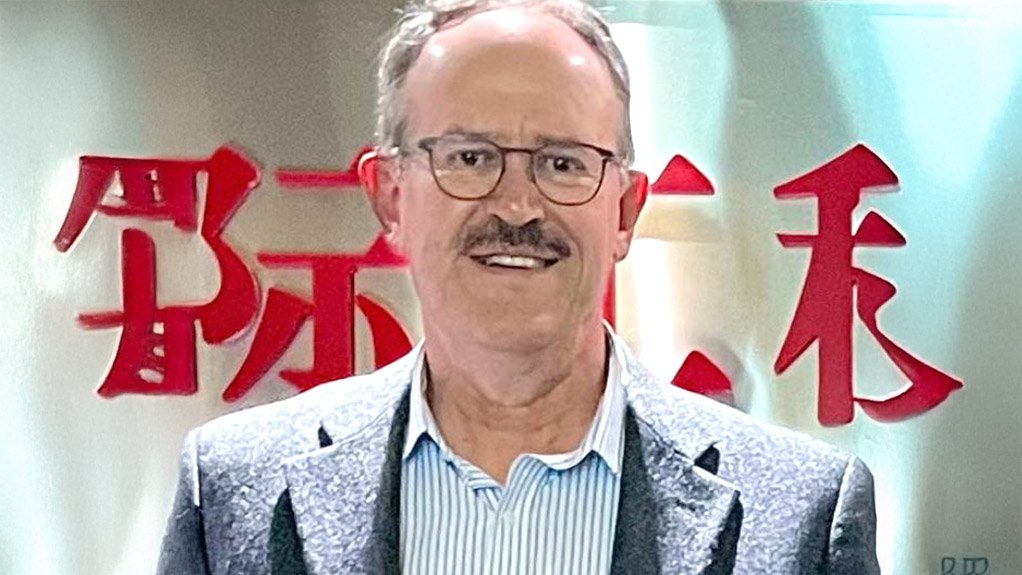
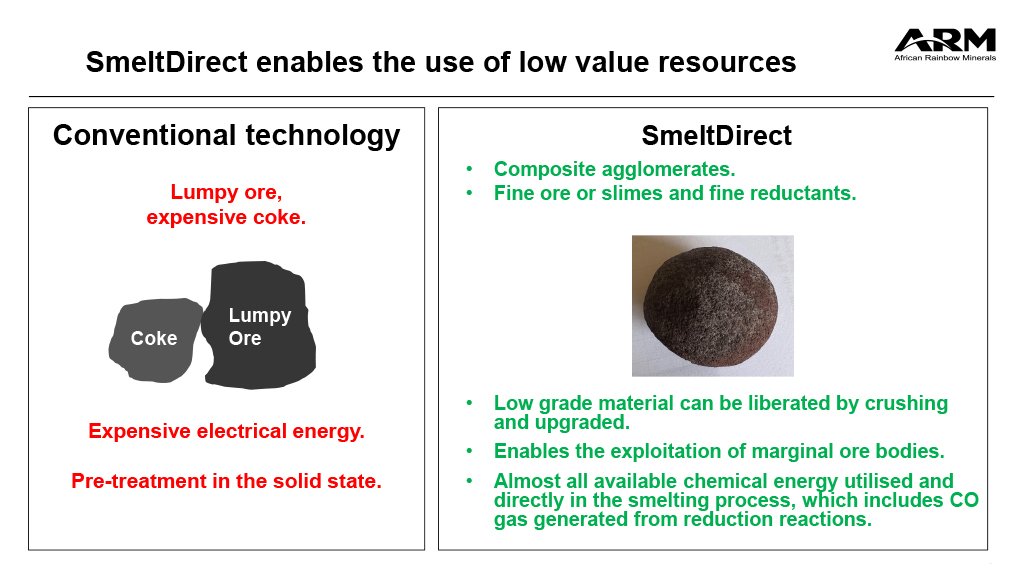
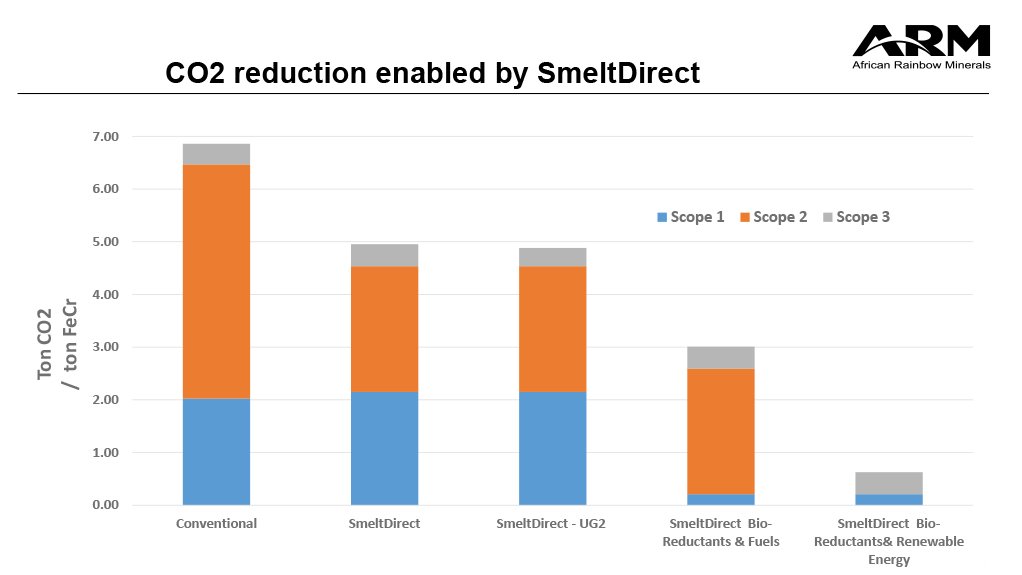
ARM Ferrous Division CE Andre Joubert interviewed by Mining Weekly's Martin Creamer. Video: Darlene Creamer.
African Rainbow Minerals Ferrous Division CE Andre Joubert.
Photo by Creamer Media Chief Photographer Donna Slater
ARM Executive Technology Development Henk Bouwer.
The smelting technology enables the use of low value resources.
Bio reductants, renewables green the smelting.
JOHANNESBURG (miningweekly.com) – New Proudly South African smelting technology, which uses 70% less electricity, cuts costs, slashes carbon emissions and can process low-grade material, has all the attributes needed to win back the top ferroalloy production renown that South Africa enjoyed in the not so distant past.
The inventive new green, clean, economically competitive, locally patented smelting technology, which is tried, tested and proven, needs only 1.2 MW of power to produce a ton of ferrochrome compared with the conventional 4 MW of power needed to do so.
It not only has all the attributes to reverse South Africa’s downward ferrochrome and ferromanganese slide but could even boost back the likes of Highveld Steel and Vanadium as well as open the way for a return of the local production of high-manganese rail.
Slogging away at developing SmeltDirect since 2012 has been Johannesburg Stock Exchange-listed African Rainbow Minerals (ARM), headed by executive chairperson Dr Patrice Motsepe.
Crucial for South Africa is that ARM has managed to come up with a trailblazer that is not only 300% more efficient but also provides bottom-of-the-cost-curve benefit.
Very advantageous as well is that it enables existing mothballed furnaces to produce three times more efficiently.
In addition, biocarbon can be used to oust fossil fuel reductants, clean renewable energy can be introduced, and manganese and iron ores that are currently unsaleable can be processed.
A detailed bankable feasibility study has been completed, engagement with ferroalloy peers on joint venture partnerships has taken place, and funding and co-financing arrangements for what will be a major generator of direct and indirect jobs are showing early promise. Some 700 jobs are created for every 200 000 t of alloy production a year and South Africa was once a producer of about four or five million tons a year, which points to the potential of creating tens of thousands of new jobs.
Moreover, the use of renewable energy with biocarbon can slash Scope 1 and 2 carbon emissions by up to 80% and Scope 3 emissions are halved, resulting in good carbon credits being on the cards when Europe’s Carbon Border Adjustment Mechanism (CBAM) comes into effect from January 2026.
Visiting experts from around the world have given the fully operational demonstration plant at ARM’s Machadodorp Works a firm thumbs up.
“If we work together, we can, in a pretty short timeframe, get South Africa back to being a leader in ferroalloy production,” ARM Ferrous Division CE Andre Joubert, in the company of ARM executive technology development Henk Bouwer, predicted in a Zoom interview with Mining Weekly. (Also watch attached Creamer Media video.)
“I'm looking at this from a South African perspective, where we can partner with existing producers in South Africa and then start with the process to convert one furnace at a time, confirm the technology, see that it can produce at a commercial level, and from there on roll it out through all our mothballed furnaces and the current low or marginally profitable smelters in South Africa.
“It’s very, very important that we, as a country, unite. We have big alloy producers in South Africa, people with a lot of experience, a lot of know-how; [it’s very, very important] that we expose this technology in that context, to partner with these entities where there are already existing plants and infrastructure. You just need to retrofit this technology on to that.
“Secondly, I think we need to have a bilateral with government…If we work together, and we're very smart, we can revive this whole beneficiation process, which we can put back into our own hands and create the necessary employment,” Joubert enthused.
Mining Weekly: In what manner should this new technology be deployed to ensure that it adds maximum value in our country?
Joubert: I want to raise three key elements of this technology. The first one, which I want to emphasise, is that this technology isn't just a nice or cute technology. It is a process that will bring us to the bottom of the cost curve, so we will be able to produce alloys competitively against the rest of the world. Number two, if you look at the challenges that we're facing with Transnet, and if we plan this properly, for every two tons of ore that you need to rail or export, you only need one ton of alloy, so immediately you reduce reliance on Transnet, and also the cost to get all of this ore and the infrastructure to get this ore out. The third one is that, in addition to energy consumption being 70% less than conventional, the technology’s Scope 1 and 2 carbon emissions from current anthracite with nothing extraordinary, are about 35% less than conventional. But if we use biocarbon, and renewable energy for our furnaces – because now the furnaces no longer need that massive bump of energy so it’s more controllable and manageable – we can reduce the Scope 1 and 2 carbon emissions by up to 80%. Then, apart from that, the Scope 3 carbon emissions can be reduced by 50% because you export half the normal volume. Also, with Europe’s CBAM coming in from January 2026, the carbon credits from this technology will be massively beneficial. The other nice thing about this is that we can retrofit this on existing furnaces that have been closed down. It will still require quite a decent capital investment, but much, much less than for building a new greenfields project somewhere else in the world. We are already engaging with industry partners to look at co-investing and we're not looking at this from an ARM-only perspective. I'm looking at this from a South African perspective.
How are you able to prove to potential funders and investors that SmeltDirect is a bankable technology that can use the many mothballed furnaces that are lying dormant?
We started this process in 2012, so this is no flash in the pan. This is not a blue sky theory that Henk and I thought about. We’ve spent hours and days and years in developing this technology. We went through the proper process of literature research. We did lab work, we did bench scale work, we did pilot scale. Now we’ve got a full-on demonstration plant running and operating. We've done a detailed bankable feasibility study. We've had external alloy experts out to the plant at Machadodorp Works to see the process. We involved a renowned expert and asked him to come and prove to us that this can't work, that it doesn't work. He came there and we got a very positive report. We've also invited industry operators, people that work in the smelting industry, executives of various companies to come and look at our plant at Machadodorp, and everyone was impressed, and understands the broad principles. We've also patented the technology to protect South Africa and our industry. There were even people flown in from Australia to come and observe first-hand what we're doing here, and all of them were very complimentary and very confident that this technology can work. We followed that up with a detailed design work by GLPS, a company well known in South Africa. They understand smelting, they understand alloy production. They've done the feasibility study for us and so there's a high level of confidence that this technology does work, and we just need that next phase of investment to bring it into full commercial production.
CHROMIUM 2024
In addition to SmeltDirect being able to process fines and slimes, Bouwer, at last month’s Chromium 2024 conference, drew attention to its ability to also unlock the potential of South Africa’s vast carbonate manganese ore resources, which are considered less desirable when taking into account conventional smelting technology.
Even so, South Africa would be forced to mine these ores as high-grade ores became depleted and 100% of these carbonate ores can be smelted efficiently with SmeltDirect, which is positioned to produce the most competitive green alloys and must not be overlooked.
Given this technological breakthrough, vast volumes of ore can now leave the country in beneficiated form and at many times the value of raw ore.
The huge economic advantage of producing a green alloy using so much less electricity must be taken up.
Producing alloy rather than exporting ore will not only create a substantial number of jobs, but also alleviate the major logistics issues in exporting vast volumes of ore.
South Africa could also be producing far more stainless steel than it is from the ferrochrome it should be producing.
The South African government departments and industry need to urgently find sustainable solutions to save the South African ferroalloy beneficiation industry and enable it to reach its potential.
Comments
Press Office
Announcements
What's On
Subscribe to improve your user experience...
Option 1 (equivalent of R125 a month):
Receive a weekly copy of Creamer Media's Engineering News & Mining Weekly magazine
(print copy for those in South Africa and e-magazine for those outside of South Africa)
Receive daily email newsletters
Access to full search results
Access archive of magazine back copies
Access to Projects in Progress
Access to ONE Research Report of your choice in PDF format
Option 2 (equivalent of R375 a month):
All benefits from Option 1
PLUS
Access to Creamer Media's Research Channel Africa for ALL Research Reports, in PDF format, on various industrial and mining sectors
including Electricity; Water; Energy Transition; Hydrogen; Roads, Rail and Ports; Coal; Gold; Platinum; Battery Metals; etc.
Already a subscriber?
Forgotten your password?
Receive weekly copy of Creamer Media's Engineering News & Mining Weekly magazine (print copy for those in South Africa and e-magazine for those outside of South Africa)
➕
Recieve daily email newsletters
➕
Access to full search results
➕
Access archive of magazine back copies
➕
Access to Projects in Progress
➕
Access to ONE Research Report of your choice in PDF format
RESEARCH CHANNEL AFRICA
R4500 (equivalent of R375 a month)
SUBSCRIBEAll benefits from Option 1
➕
Access to Creamer Media's Research Channel Africa for ALL Research Reports on various industrial and mining sectors, in PDF format, including on:
Electricity
➕
Water
➕
Energy Transition
➕
Hydrogen
➕
Roads, Rail and Ports
➕
Coal
➕
Gold
➕
Platinum
➕
Battery Metals
➕
etc.
Receive all benefits from Option 1 or Option 2 delivered to numerous people at your company
➕
Multiple User names and Passwords for simultaneous log-ins
➕
Intranet integration access to all in your organisation