Updated range to improve rotational moulding
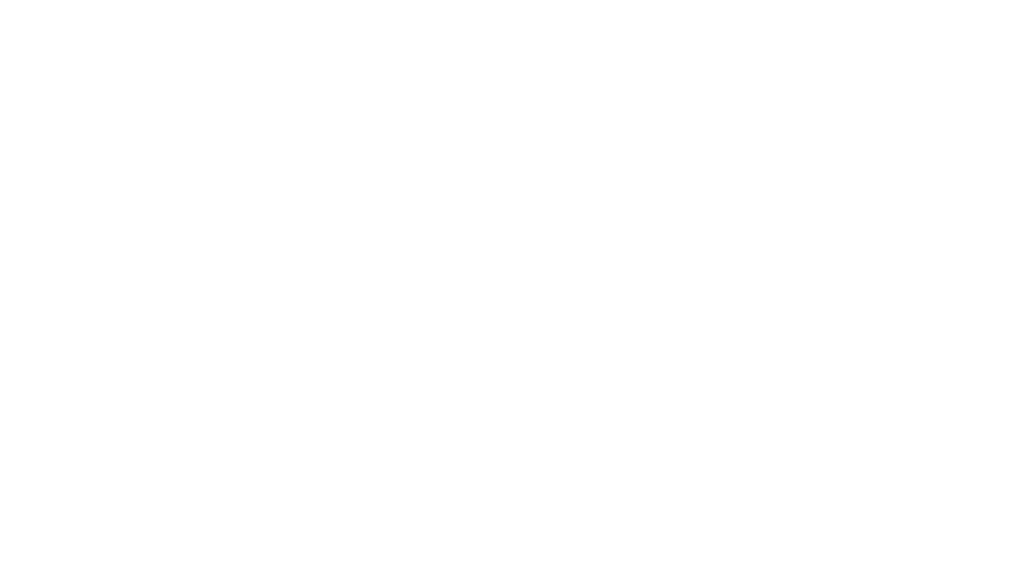
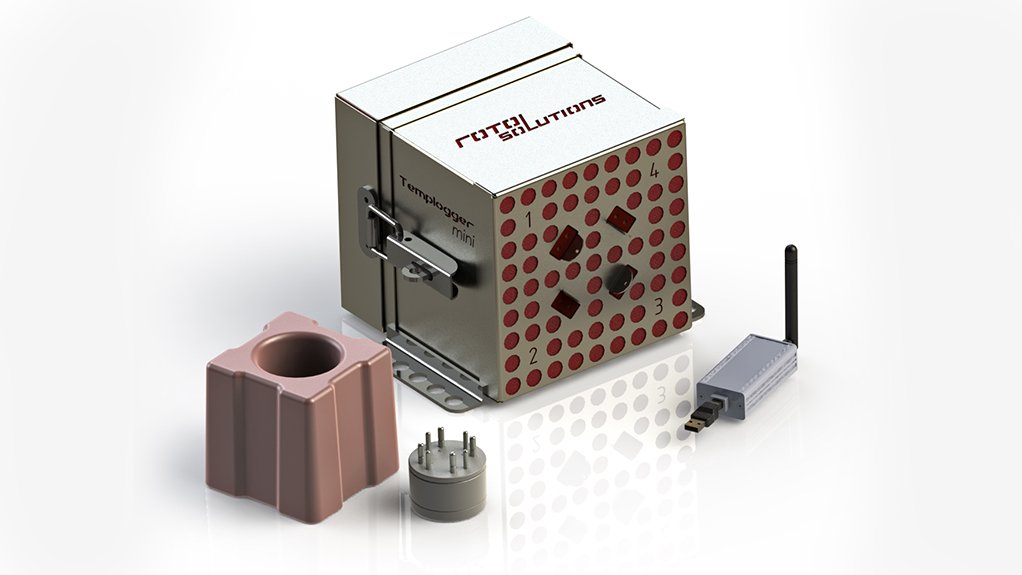
CLOSER CONTROL TempLogger is a real-time temperature-monitoring and -control system, and assists operators in maintaining an ideal processing temperature for inside a mould
Rotational moulding equipment provider Roto Solutions released the latest version among its range of TempLogger temperature monitoring and control systems last month.
TempLogger is a real-time temperature-monitoring and -control system, capable of continuous monitoring and requiring minimal intervention in a production environment. The system enables rotational moulders to measure, control and improve moulded products.
Roto Solutions owner Gary Lategan states that this latest range, Version 7 (V7), will have a range of new and improved features, which will make temperature monitoring in rotational moulding simpler, and allow closer control of the rotational moulding process.
“Developments in temperature-monitoring technology over the years have allowed for automating certain processes in rotational moulding. The new features we’ve added will help improve production even more in the industry and will help rotational moulders to make better quality parts 24/7,” he enthuses.
Rotation moulding involves using a hollow mould, which is heated and filled with a certain material such as a polymer. It is then rotated, allowing an even lay-up of the powder to stick to the walls of the mould.
The mould continues to rotate at all times during the heating phase to help avoid deformation during the cooling phase.
Operators are not able to see inside an oven, let alone the mould, to check if the product was moulded to the optimum temperature during the rotational moulding process. Before temperature monitoring systems were available, much guesswork was involved in the process.
Operators relied on time and in some cases visual internal inspection while the mould was inside an oven. Once the required time had passed, the operator would open the oven and the mould to check if the part had formed correctly.
If the part was under-cured or deformed it would have to be scrapped and a new time would need to be set to try and produce a good quality part, subsequently making for an inefficient production process.
However, temperature-monitoring systems, such as TempLogger, have allowed for greater control over this process. The system analyses the total production cycle, providing real-time data on the critical factors occurring inside the oven and mould.
These factors include the temperature inside the oven and on different parts of the mould; and particularly the internal mould temperature; which is used to control the heating, cooling and demoulding cycles; and the amount and type of material used inside of the mould. This information is incorporated into production graphs, to allow for monitoring of cycle times, production reports and material consumption.
Considering these factors, TempLogger assists operators in maintaining the ideal processing temperature for any amount or type of materials inside the mould. This is referred to as the peak internal air temperature, or PIAT.
Alarm settings control oven operation and cooling cycles based on internal mould temperatures.
Additionally, making use of the comprehensive information provided can allow operators to optimise heating, cooling and de-moulding cycle times and improve production rates.
A significant factor which has been improved on in V7 is the cooling process of the TempLogger Sender and Radio, which are placed inside the oven.
Lategan explains that Roto Solutions’ competitors use ice packs, which are placed inside a unit, to cool the Sender and Radio. Roto Solutions’ use of heat absorbers, however, negates the need for cooling between shifts.
The heat absorbers would need to be changed frequently during a moulding shift, which would require opening and closing of the TempLogger V7 Sender during demoulding.
However, improvements made to the TempLogger V7 Sender now allow for a cooled heat absorber to last for a whole moulding shift and to be replaced only when the shift ends. This means that operators do not need to change the heat absorber every cycle of the oven.
This further improves production, as operators can now run up to a nine-hour moulding shift without needing to open the TempLogger V7 Sender.
Comments
Press Office
Announcements
What's On
Subscribe to improve your user experience...
Option 1 (equivalent of R125 a month):
Receive a weekly copy of Creamer Media's Engineering News & Mining Weekly magazine
(print copy for those in South Africa and e-magazine for those outside of South Africa)
Receive daily email newsletters
Access to full search results
Access archive of magazine back copies
Access to Projects in Progress
Access to ONE Research Report of your choice in PDF format
Option 2 (equivalent of R375 a month):
All benefits from Option 1
PLUS
Access to Creamer Media's Research Channel Africa for ALL Research Reports, in PDF format, on various industrial and mining sectors
including Electricity; Water; Energy Transition; Hydrogen; Roads, Rail and Ports; Coal; Gold; Platinum; Battery Metals; etc.
Already a subscriber?
Forgotten your password?
Receive weekly copy of Creamer Media's Engineering News & Mining Weekly magazine (print copy for those in South Africa and e-magazine for those outside of South Africa)
➕
Recieve daily email newsletters
➕
Access to full search results
➕
Access archive of magazine back copies
➕
Access to Projects in Progress
➕
Access to ONE Research Report of your choice in PDF format
RESEARCH CHANNEL AFRICA
R4500 (equivalent of R375 a month)
SUBSCRIBEAll benefits from Option 1
➕
Access to Creamer Media's Research Channel Africa for ALL Research Reports on various industrial and mining sectors, in PDF format, including on:
Electricity
➕
Water
➕
Energy Transition
➕
Hydrogen
➕
Roads, Rail and Ports
➕
Coal
➕
Gold
➕
Platinum
➕
Battery Metals
➕
etc.
Receive all benefits from Option 1 or Option 2 delivered to numerous people at your company
➕
Multiple User names and Passwords for simultaneous log-ins
➕
Intranet integration access to all in your organisation