Using nonoriginal parts only mitigates initial costs
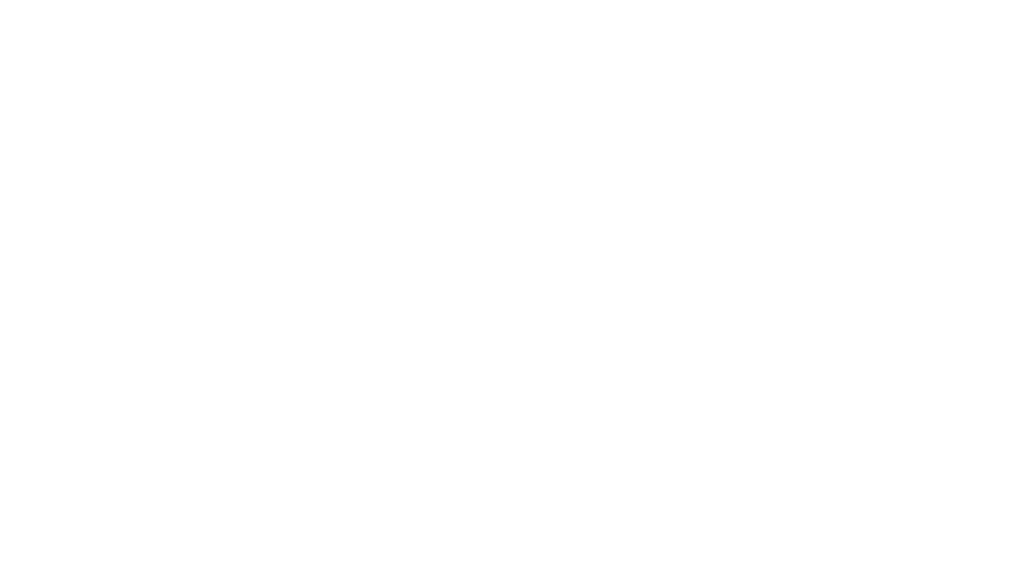
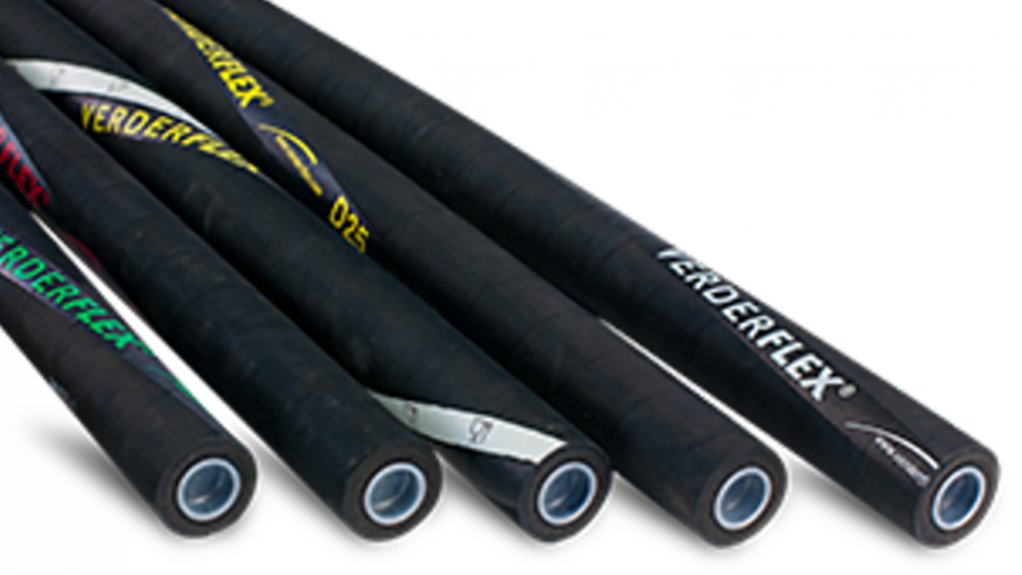
FLEX IT The Verderflex hose is perfectly suited to Verders Dura pumps Caption 02:
In a competitive industrial and mining arena, companies are often driven to keep purchase costs as low as possible and resort to fitting nonoriginal-equipment-manufacturer (non-OEM) aftermarket spare parts into sophisticated pieces of equipment, cautions Verder Pumps SA client services Africa lead Reinhard Seidel.
He explains that this approach ultimately undermines the company’s ability to keep up with tight production schedules and ensure minimal downtime.
“The non-OEM aftermarket parts seldom stand up to the rigorous duty that the OEM part was designed for and, ultimately, end up impacting on uptime, resulting in production losses,” he says.
He cites a recent case study at one of the largest copper producers in the Southern African Development Community, in which the hidden costs of buying a “surprisingly expensive low-priced” peristaltic hose were exposed.
For commercial reasons, the mining company chose to fit a non-OEM hose in a Verder peristaltic pump. Production bore the brunt of this commercial decision, as the “surprisingly expensive low-priced” hose failure rate was an average of three failures a week.
“These failures resulted in production stoppages, and increased maintenance and manpower requirements,” he points out.
As a result of the production stoppages, Verder was asked to investigate the reason for the failures. It subsequently presented a simple remedy, namely fitting an OEM hose.
The exercise of buying and fitting the non-OEM hose in an attempt to reduce inventory costs and minimise expenditure proved to be an expensive choice.
Seidel stresses that while non-OEM aftermarket hoses may cost less on initial purchase, using hoses with incorrect dimensions and hoses of inferior construction leads to frequent hose failures, which, in turn, leads to unplanned stoppages, production losses and avoidable maintenance costs.
These direct costs include the replacement of lubricant and premature gearbox failure, owing to the ingress of the pumped media into the gearbox, caused by the burst hose, and the cost of another replacement hose.
The OEM hose was fitted to the DURA Pump and run under the same operating conditions. Records have been kept over this time – to measure the conditions and timing until a potential failure of the Verder OEM hose – and the results have been significant.
The non-OEM hose had failed and been replaced, on average, three times a week. In comparison, the Verder OEM hose – installed on December 1, 2021 – is still in operation, without failure or loss of production throughput.
As such, the cost saving far outweighed any costs saved in installing the non-OEM hose.
Specific Specifications
“Every Verderflex hose is manufactured to rigid specifications for consistent wall thickness, to ensure that the fibre reinforcing is embedded centrally when the hose is constructed,” says Siedel.
Consequently, the precision manufacturing process, mitigates the need to carry out machining of the hose’s outside diameter.
Additionally, the importance of correct pulsation dampeners and other technicalities that affect hose life cannot be understated – just dimensional differences will have an influence on hose life which leads to costs associated with unplanned stoppages.
The Verder hose has a signature textured finish, which enhances lubricant adhesion to the hose, thereby reducing surface friction between hose and shoe.
He explains that for a client to be sure that they are fitting an OEM hose, the client will notice that all Verderflex hoses have a clear colour-coded identification stripe and Verder branding along the length of the hose, indicating the material of construction.
“The construction of the OEM hose plays an integral part in the life span of the hose,” says Seidel.
He concludes that if the hose the client is fitting in its Verder peristaltic pump does not have these markings, the client can be sure that while it may be saving upfront costs by buying cheap, the client will most certainly be buying at least twice.
Comments
Announcements
What's On
Subscribe to improve your user experience...
Option 1 (equivalent of R125 a month):
Receive a weekly copy of Creamer Media's Engineering News & Mining Weekly magazine
(print copy for those in South Africa and e-magazine for those outside of South Africa)
Receive daily email newsletters
Access to full search results
Access archive of magazine back copies
Access to Projects in Progress
Access to ONE Research Report of your choice in PDF format
Option 2 (equivalent of R375 a month):
All benefits from Option 1
PLUS
Access to Creamer Media's Research Channel Africa for ALL Research Reports, in PDF format, on various industrial and mining sectors
including Electricity; Water; Energy Transition; Hydrogen; Roads, Rail and Ports; Coal; Gold; Platinum; Battery Metals; etc.
Already a subscriber?
Forgotten your password?
Receive weekly copy of Creamer Media's Engineering News & Mining Weekly magazine (print copy for those in South Africa and e-magazine for those outside of South Africa)
➕
Recieve daily email newsletters
➕
Access to full search results
➕
Access archive of magazine back copies
➕
Access to Projects in Progress
➕
Access to ONE Research Report of your choice in PDF format
RESEARCH CHANNEL AFRICA
R4500 (equivalent of R375 a month)
SUBSCRIBEAll benefits from Option 1
➕
Access to Creamer Media's Research Channel Africa for ALL Research Reports on various industrial and mining sectors, in PDF format, including on:
Electricity
➕
Water
➕
Energy Transition
➕
Hydrogen
➕
Roads, Rail and Ports
➕
Coal
➕
Gold
➕
Platinum
➕
Battery Metals
➕
etc.
Receive all benefits from Option 1 or Option 2 delivered to numerous people at your company
➕
Multiple User names and Passwords for simultaneous log-ins
➕
Intranet integration access to all in your organisation