Venetia underground project heading for first production in 2023
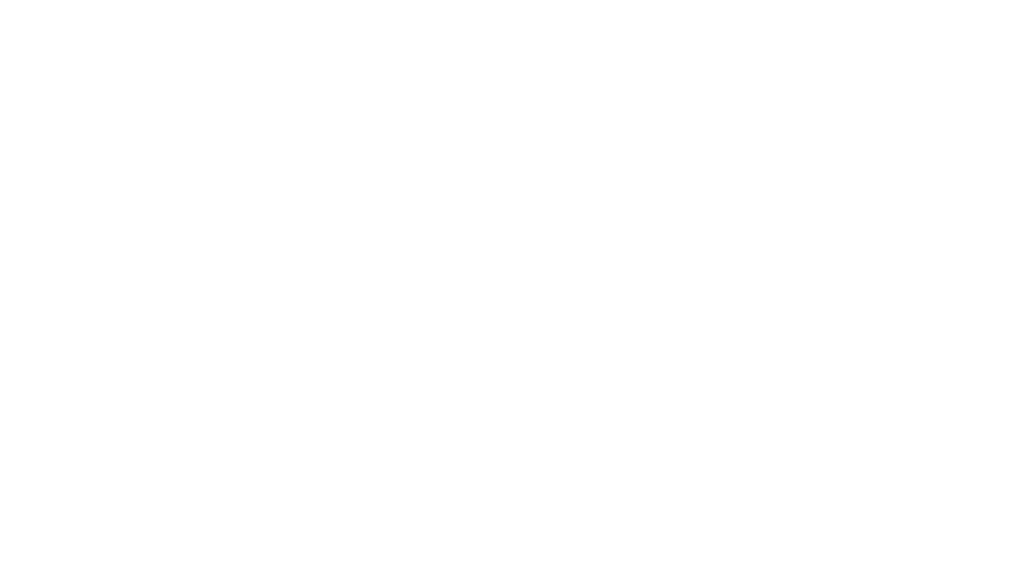
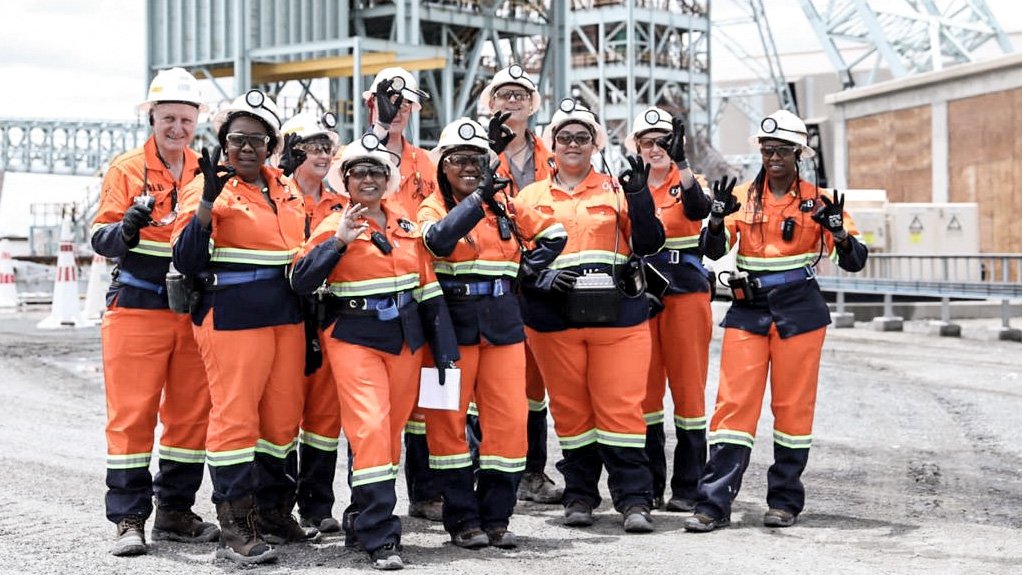
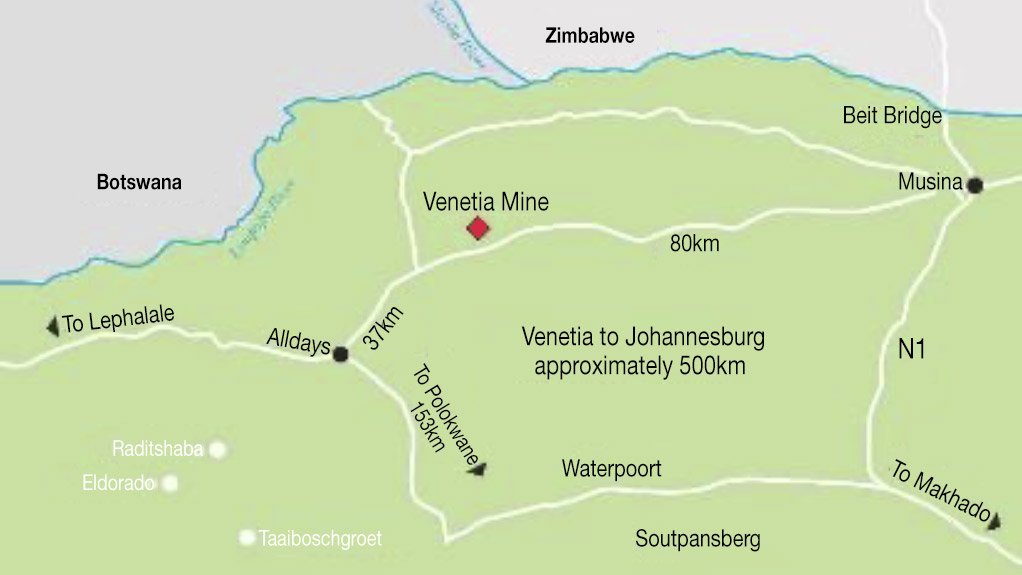
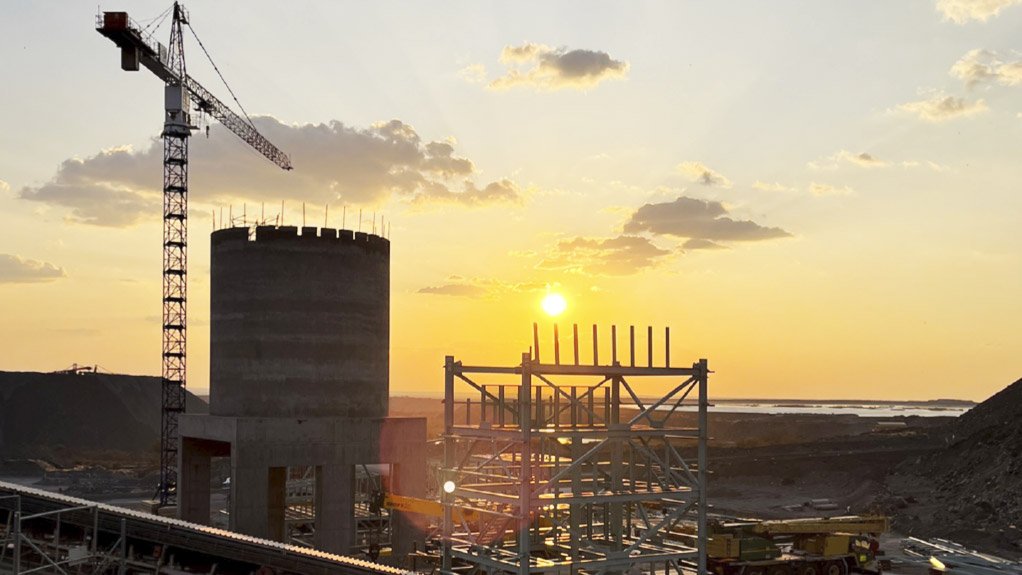
Mining Weekly was part of this week's Venetia Underground Project media visit.
Map showing Venetia.
Surface infrastructure at Venetia Underground Project.
A visit by Engineering News & Mining Weekly to the Venetia Underground Project (VUP) on November 14 provided far-reaching insight into this major diamond development that is scheduled to achieve occupational readiness and first production next year – “hopefully in the first part of the year, all going well”, according to VUP project director Allan Rodel.
“We had a setback recently with some of our visa approval processes, which has caused some challenges, but we’ll overcome them,” Rodel added.
Venetia, South Africa’s largest diamond producer, is located some 32 km south of the Limpopo river, not far from the borders of Botswana and Zimbabwe, and is about 500 km from Johannesburg.
In 2013, Engineering News & Mining Weekly witnessed the first sod-turning of the $2-billion underground extension, amid vibrant, ongoing opencast operation.
“The mine, as we speak, is 30 years old this year,” said Rodel of Venetia, which has been an absolute gem for De Beers ever since the openpit was opened in 1992.
The openpit will continue to operate until December, after which the operation will transition to underground until 2046. “We know, though, that there is definitely opportunity below the current levels,” was Rodel’s comment to visiting media.
Vertical shafts, lateral access tunnels, life-of-mine decline and pit ramp, and related surface, underground and offsite infrastructure make up the VUP’s scope, which provides for the continued mining of two kimberlite orebodies – K01 and K02 – which will be accessed through two vertical shafts extending to a depth of 1 065 m.
Engineering News & Mining Weekly went down the production shaft and the decline and pit ramp, the first production areas.
The production shaft, with a finished internal diameter of 7 m, will be fitted with two rock winders, each having two 24 t payload skips.
The service shaft, also with a finished internal diameter of 7 m, will provide all the services to the underground workings, with both production and service shafts offering downcast air intakes.
The decline and pit ramp will serve as an additional air intake and logistics management facility. The decline extends to a vertical depth of 590 m.
The K01 orebody will be mined using sub-level caving to produce 4 Mt/y to 4.5 Mt/y, averaging 3.5-million carats a year.
Sublevel caving will also be deployed at KO2, producing 1.9 Mt/y and averaging 0.9-million carats a year.
This equates to 5.9 Mt/y, which will match the throughput capability of Venetia’s main treatment plant.
The ground-handling facilities include manual and automated load-haul dumpers, manual and automated rock breakers, vertical ore passes, an automated truck-loop, underground crushers, ore and waste conveyors and silos.
The trackless fleet will be maintained underground.
Rocks Strengthening Tailings Dams
As Engineering News & Mining Weekly flew in, visible from the air was the exemplary way Venetia has used waste rock to bolster its fines residue deposits, and how rock impounding has been implemented in addition to the normal tailings-linked checks, balances, and assurances.
Moreover, the first of six water control doors designed to counter water ingress into the underground mine has been completed, with De Beers and the South African Weather Service collaborating to develop a weather radar system that will detect weather activities beyond the borders of South Africa, into Botswana and Zimbabwe, where most of the tropical storms arise.
The water control doors will be activated in the event of water inflows into the mine exceeding the capacity of the underground pumping system, which will ultimately have the ability to pump 4 500 m3/h out of the mine. They are designed to seal off the ‘dry’ side of the mine, where the water pumps and other critical infrastructure are located, from the ‘wet’ side, where mining operations on the kimberlite pipe take place.
“Certainly the sheer size of these doors is unusual,” was Murray & Robert Cementation contracts manager Jacques Labuschagne’s comment on the water door which has been built into a roughly 9-m-high by 9-m-wide excavation.
The first water door has a steel frame some 8 m high, 8 m wide and 1 m thick and is anchored into the host rock by 40 mm steel anchors, 234 in total. The completed structure comprises 60 t of steel. In addition, approximately 80 m3 of concrete was used to seal the area around the door to create a watertight interface between the door and the host rock.
Underground dewatering will be achieved through dedicated water passes, water launder tunnelling, degritting facilities, settlers, dams, and pumping infrastructure directing effluent to surface.
Surface Infrastructure
From an elevated position on top of the headgear, Engineering News & Mining Weekly was able to view infrastructure built over the last three years or so. A surface terrace has a main consumer substation, winder houses and headgears, office complex, change house, lamp room, proto room, concrete batch plant, surface ventilation fans, compressor house, shaft service workshop incorporating a rope store/skip workshop, fire water and process water pump station, process water settlers, domestic water tank, process water dam, fire water tanks, ore and waste conveyors, and a buffer stockpile.
At steady state, ventilation fans on surface will extract exhaust air through raise-bored holes.
Skills Development
Many employees drawn from the local community have been trained in a variety of mining and engineering skills.
In addition, Venetia’s ‘Changing Lives Forever’ skills development programme aims to develop skills in the construction industry, with practical training opportunities being created at the mine’s accommodation projects.
Comments
Press Office
Announcements
What's On
Subscribe to improve your user experience...
Option 1 (equivalent of R125 a month):
Receive a weekly copy of Creamer Media's Engineering News & Mining Weekly magazine
(print copy for those in South Africa and e-magazine for those outside of South Africa)
Receive daily email newsletters
Access to full search results
Access archive of magazine back copies
Access to Projects in Progress
Access to ONE Research Report of your choice in PDF format
Option 2 (equivalent of R375 a month):
All benefits from Option 1
PLUS
Access to Creamer Media's Research Channel Africa for ALL Research Reports, in PDF format, on various industrial and mining sectors
including Electricity; Water; Energy Transition; Hydrogen; Roads, Rail and Ports; Coal; Gold; Platinum; Battery Metals; etc.
Already a subscriber?
Forgotten your password?
Receive weekly copy of Creamer Media's Engineering News & Mining Weekly magazine (print copy for those in South Africa and e-magazine for those outside of South Africa)
➕
Recieve daily email newsletters
➕
Access to full search results
➕
Access archive of magazine back copies
➕
Access to Projects in Progress
➕
Access to ONE Research Report of your choice in PDF format
RESEARCH CHANNEL AFRICA
R4500 (equivalent of R375 a month)
SUBSCRIBEAll benefits from Option 1
➕
Access to Creamer Media's Research Channel Africa for ALL Research Reports on various industrial and mining sectors, in PDF format, including on:
Electricity
➕
Water
➕
Energy Transition
➕
Hydrogen
➕
Roads, Rail and Ports
➕
Coal
➕
Gold
➕
Platinum
➕
Battery Metals
➕
etc.
Receive all benefits from Option 1 or Option 2 delivered to numerous people at your company
➕
Multiple User names and Passwords for simultaneous log-ins
➕
Intranet integration access to all in your organisation