We do not want to compete with steel, we want to replace it, GFRP Tech CEO says at facility launch
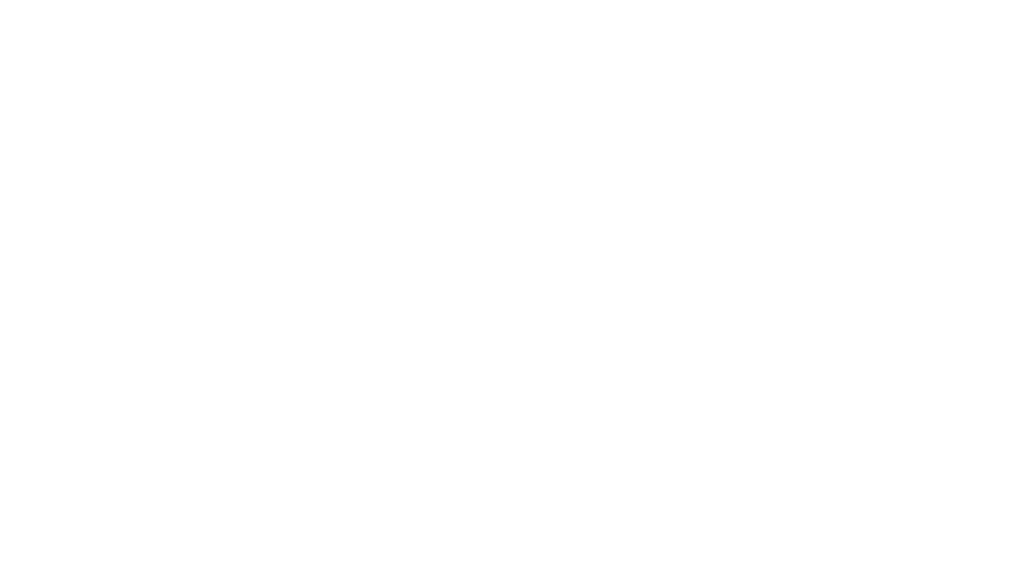
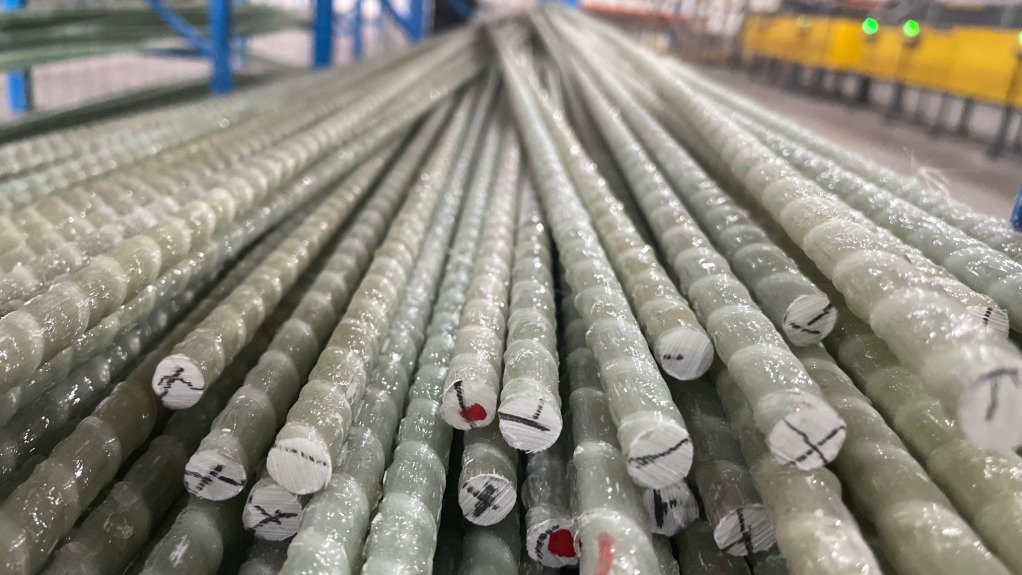
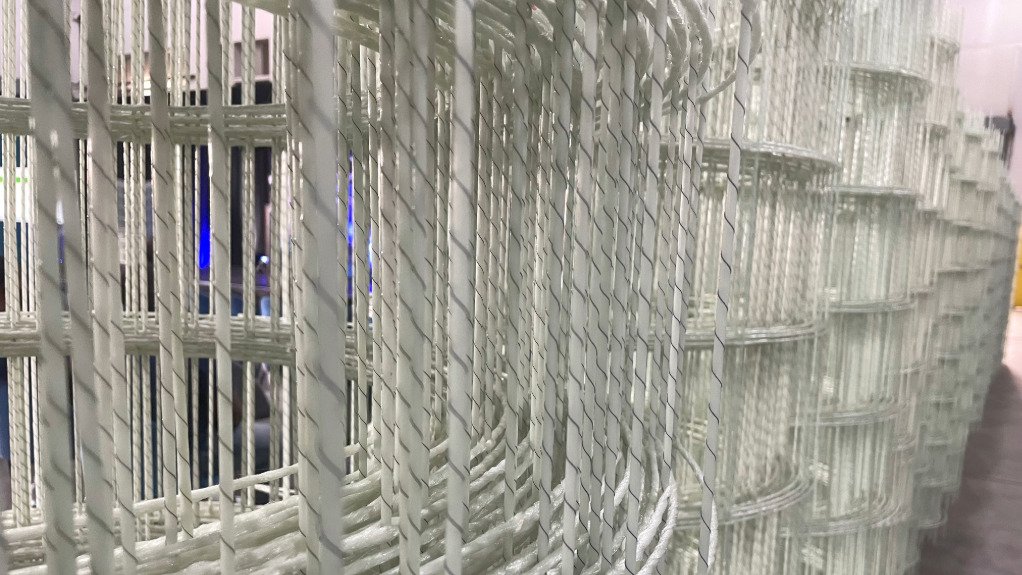
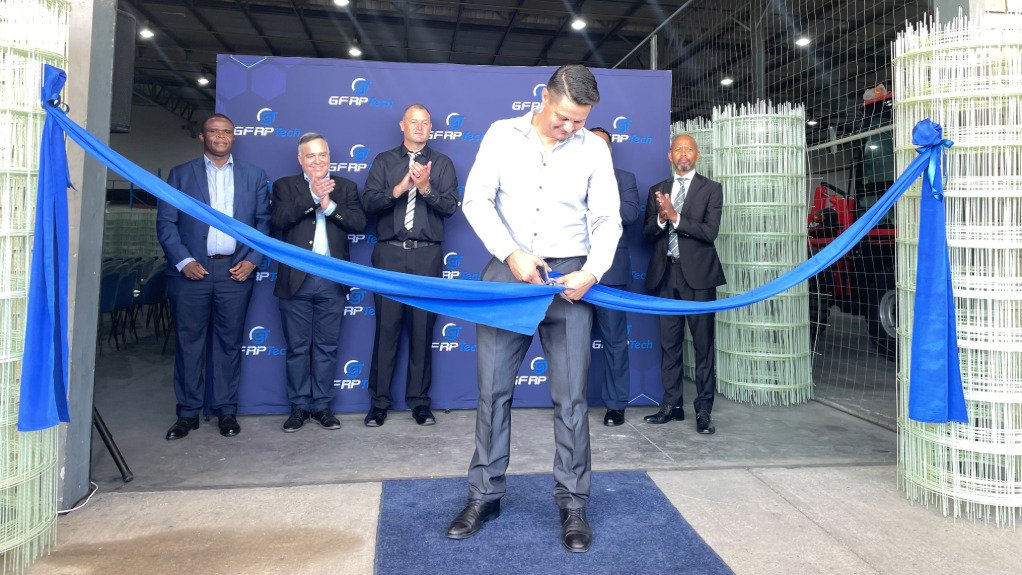
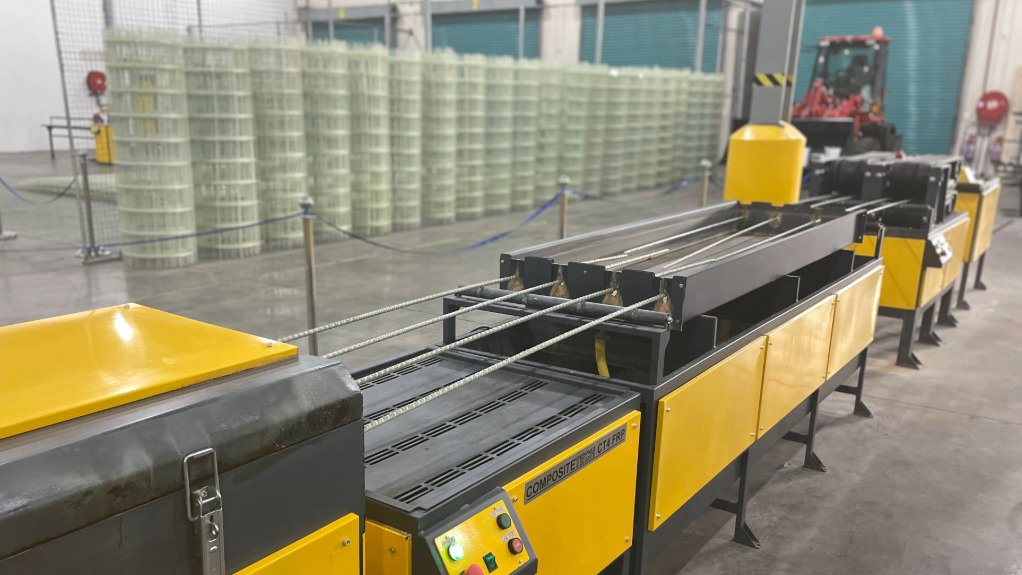
Glass fibre reinforced polymer rebar
Photo by Creamer Media
Glass fibre reinforced polymer mesh
Photo by Creamer Media
GFRP Tech CEO and founder Allen Fiford cutting the ribbon at the opening ceremony
Photo by Creamer Media
Glass fibre reinforced polymer manufacturing
Photo by Creamer Media
Structural reinforcement materials manufacturer GFRP Tech has opened a new research and development (R&D) and manufacturing facility in Linbro Park, Sandton.
The facility – the result of investments of more than R100-million – was officially opened with a ribbon-cutting ceremony on March 6 and will manufacture limited volumes of the company’s novel Envirabar and Enviramesh products, which are glass fibre reinforced polymer (GFRP) composite alternatives to steel rebar and steel mesh.
“Our aim is not to compete with steel. We are looking to replace steel. We can be competitive, since we are on the same path pricewise, but the benefits and advantages of GFRP far outweigh steel in almost every respect,” GFRP Tech CEO and founder Allen Fiford told Engineering News.
The new facility, which will employ about 30 people, will also facilitate GFRP R&D to further enhance the product capabilities and provide training in the use of GFRP products.
Fiford revealed that the company had plans to open a second manufacturing-only plant within the next two years, which would accommodate a much larger manufacturing capacity, employing about 300 people.
The GFRP products, which are the result of eight years of research in the viability of GFRP composite materials in construction projects, have proven to be 75% lighter than steel but three times stronger, with a tensile strength of more than 1 500 mPa compared to the standard steel rebar tensile strength of about 500 mPa.
“The lightweight nature of GFRP materials facilitates greater efficiency within workmanship on site, moving of materials, and reduces transportation costs,” Fiford said at the launch.
The GFRP composite material is electromagnetic neutral, making it ideal for use in specialist construction projects such as communications centres, data centres or server farms, as it effectively eliminates the Faraday cage effect caused by steel mesh.
In addition, GFRP composite materials offer zero conductivity, zero corrosion and improved ductility.
“Corrosion is a big risk in the construction industry. That’s where most structures fail. That’s one of the key reasons we developed GFRP materials to replace steel”, Fiford said.
“What happens is that when reinforcing steel is exposed to moisture onsite, it flakes. If you don’t brush the rust away and then pour the concrete, the concrete won’t adhere to the surface of the steel. This results in the steel being loose within the concrete, which defeats the purpose,” consulting firm DPN Consulting MD Preven Naicker said, noting that this could severely undermine structural integrity.
Another benefit of GFRP Tech’s products is that they have absolutely no resale value, which significantly reduces the risk of theft from site.
“The biggest problem we [struggle] with in this country is risk to project. Through that risk, we know that there is a lot of theft because that’s what happens to our most useful minerals. You get steel, you bring it to site, and before you know it, it’s missing. We’ve got a product that has no resale value other than the purpose it was designed for,” Fiford explained.
“At the moment, the amount of issues that contractors have with regard to steel theft onsite is significant. The social impacts of having steel onsite – it creates the opportunity for theft.
“The zero resale value of GFRP products means that we will, by default, do away with the threat of theft. The only theft that might occur is out of spite. This product is purpose made, which means you can do nothing with it except to use it for the purpose intended,” Naicker added.
Further, the GFRP manufacturing process also uses significantly less energy than its steel counterparts.
“It has a low carbon footprint. It takes less energy to manufacture and, obviously, we are not mining vast amounts of iron ore and having it smelted down to get reinforcing steel,” Fiford said.
He added that the adoption of novel materials like these depended on changing the mindsets of young architectural and engineering professionals to consider more novel and environmentally friendly materials.
“Infrastructure restoration is the budget item that we sit with in this country. We’ve got dilapidated roads, bridges that are failing, and other structures that are failing. The biggest problem with that is failing concrete. Now, with the GFRP bar, we know that we can do restoration or design new infrastructure and save a lot of time and money,” Fiford said.
Further, with ArcelorMittal South Africa’s recent announcement that it will be closing its longs business, steel rebar is set to become more costly and harder to come by, which works in GFRP Tech’s favour.
“It is definitely an advantage for us because the country will be limited in terms of the supply of reinforcing steel. It presents an opportunity to embrace innovative, sustainable solutions that can revitalise our economy and reduce our dependency on high-energy use materials,” Fiford said.
Although GFRP Tech’s products currently meet local construction standards, Fiford confirmed that work is currently underway to ensure that they conform to international standards as well.
Comments
Press Office
Announcements
What's On
Subscribe to improve your user experience...
Option 1 (equivalent of R125 a month):
Receive a weekly copy of Creamer Media's Engineering News & Mining Weekly magazine
(print copy for those in South Africa and e-magazine for those outside of South Africa)
Receive daily email newsletters
Access to full search results
Access archive of magazine back copies
Access to Projects in Progress
Access to ONE Research Report of your choice in PDF format
Option 2 (equivalent of R375 a month):
All benefits from Option 1
PLUS
Access to Creamer Media's Research Channel Africa for ALL Research Reports, in PDF format, on various industrial and mining sectors
including Electricity; Water; Energy Transition; Hydrogen; Roads, Rail and Ports; Coal; Gold; Platinum; Battery Metals; etc.
Already a subscriber?
Forgotten your password?
Receive weekly copy of Creamer Media's Engineering News & Mining Weekly magazine (print copy for those in South Africa and e-magazine for those outside of South Africa)
➕
Recieve daily email newsletters
➕
Access to full search results
➕
Access archive of magazine back copies
➕
Access to Projects in Progress
➕
Access to ONE Research Report of your choice in PDF format
RESEARCH CHANNEL AFRICA
R4500 (equivalent of R375 a month)
SUBSCRIBEAll benefits from Option 1
➕
Access to Creamer Media's Research Channel Africa for ALL Research Reports on various industrial and mining sectors, in PDF format, including on:
Electricity
➕
Water
➕
Energy Transition
➕
Hydrogen
➕
Roads, Rail and Ports
➕
Coal
➕
Gold
➕
Platinum
➕
Battery Metals
➕
etc.
Receive all benefits from Option 1 or Option 2 delivered to numerous people at your company
➕
Multiple User names and Passwords for simultaneous log-ins
➕
Intranet integration access to all in your organisation