Weighing solution aids accuracy
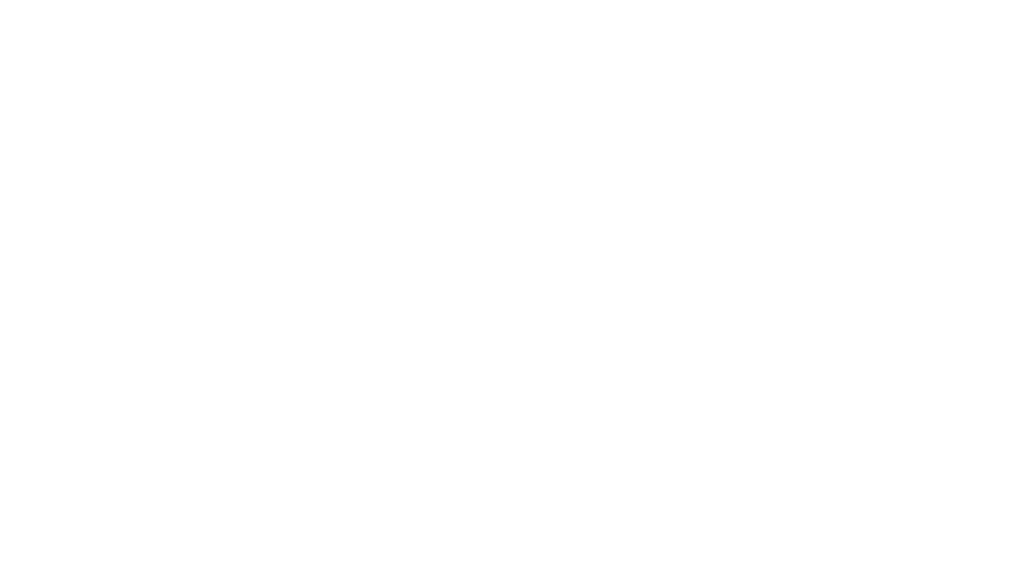
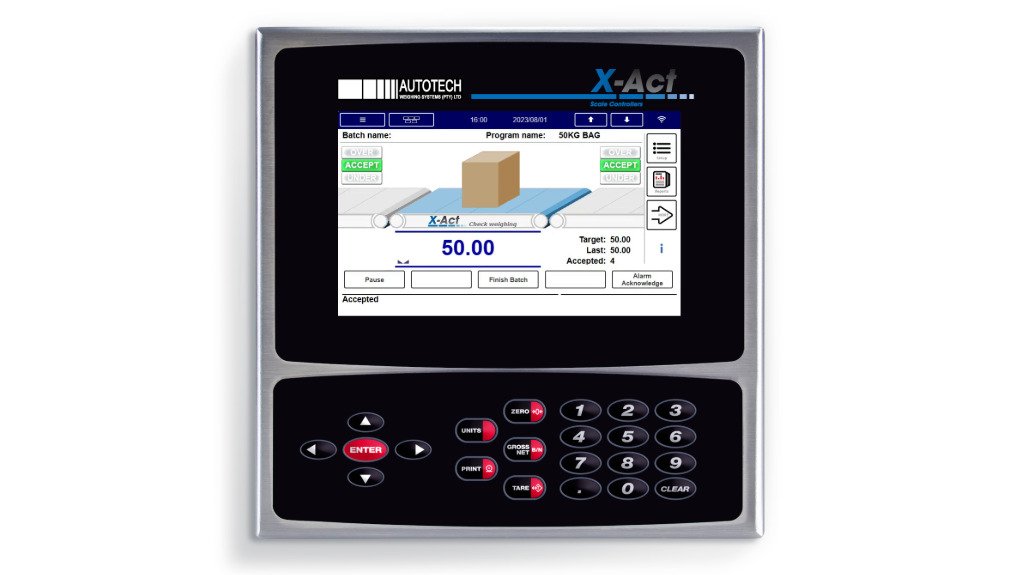
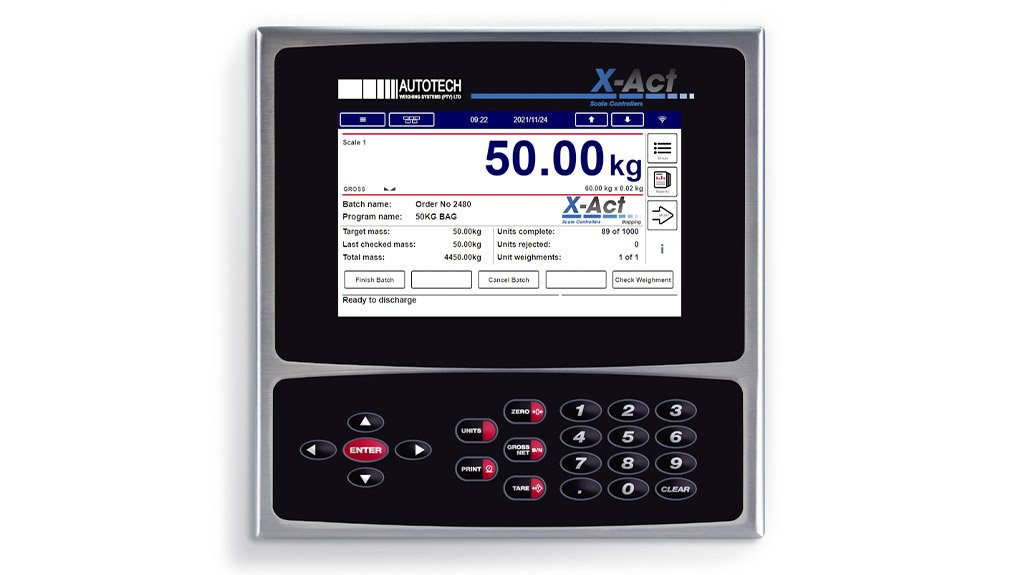
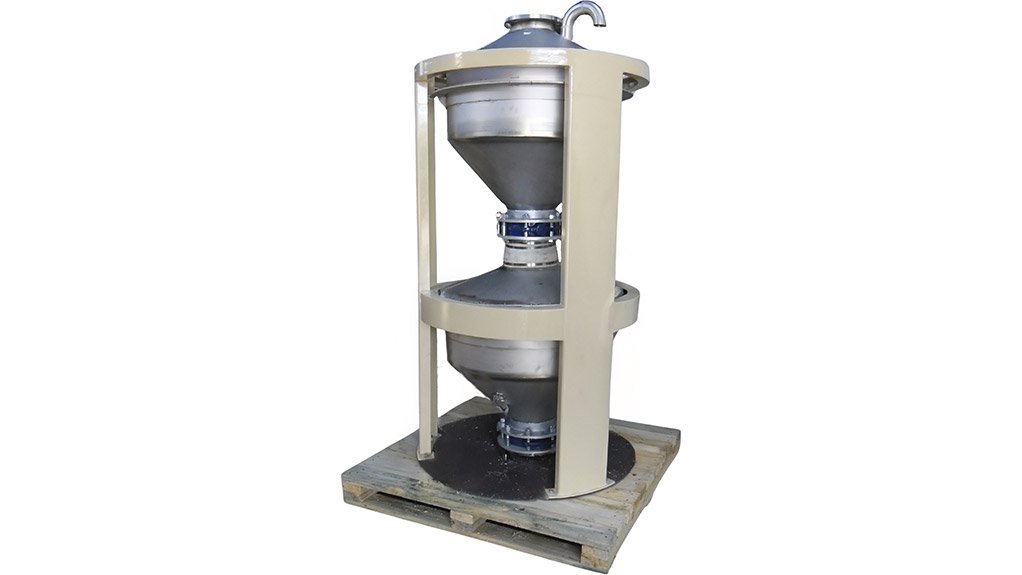
WORTH THE WEIGHT The X-Act Scale Controller and weighing systems ensures efficiency, accuracy and cost-effectiveness, offering precise weighing to sugar mills
Through its X-Act Scale Controller and weighing systems, measuring instruments supplier Autotech Weighing Systems offers efficiency, accuracy and cost-effectiveness to sugar mills.
Autotech’s technology is currently being implemented at sugar mills throughout Africa; it is also manufacturing a new design of throughput weigher to enhance production efficiency. This system measures material from the mill to the packing plant, ensuring correlation during processing stages, says Autotech national technical sales representative Kyle Fourie.
The X-Act Scale Controller is designed to accurately measure sugar throughput and production from the mill through to dispatch, maximising throughput while maintaining accuracy. The full turnkey solution includes both hardware and software tailored to customers’ specific requirements.
By ensuring precise weighing, the system mitigates the risks, costs and legal implications associated with under- or overfilling bags. Additionally, the controller minimises the costs and additional time required to correct inaccurately filled bags.
Further, the X-Act Scale Controller enhances automation within sugar processing plants by using various communication protocols and fieldbus connectivity options. The controller displays weighment, production, status and diagnostic information. Additionally, it communicates in real-time with enterprise resource planning and supervisory control and data acquisition systems, thereby ensuring overall equipment effectiveness and seamless data integration.
The X-Act Scale Controller can also automatically adjust the feeding parameters for the best balance between speed and accuracy, without operator intervention, making it ideal for high-speed bagging operations.
Autotech’s throughput weigher is particularly suited for sugar mills owing to its efficiency and reliability, as well as minimal downtime requirements. The system is user-friendly, providing easy access to data for monitoring and optimisation.
By using the same controller hardware across all weighing systems, Autotech aids cost-effectiveness, as it allows sugar mills to maintain a stockholding of a common set of spare parts.
Autotech’s weighing mechanics, controlled by the X-Act controller, cater to a range of applications, including net and gross weighers for bagging systems from 10 kg to over 1 t, throughput weighers and inline check scales on conveyors.
For free-flowing sugar, the X-Act controller ensures accuracy and efficiency across various applications. In bagging operations, it can handle 10 kg to 50 kg bags at a rate that exceeds 15 bags a minute with an accuracy of 0.1%, while bulk bagging achieves throughput exceeding 60 t/h with an accuracy of 0.1%. For general throughput, the system can process more than 80 t/h while maintaining an accuracy of 0.1%.
Autotech’s weighing systems use high-precision, internationally approved loadcells. Further, the X-Act controller is approved by the National Regulator for Compulsory Specifications as well as various international industry bodies, such as International Organisation of Legal Metrology, ensuring compliance and trust in the final product, says Fourie.
Customisation and Support
Autotech collaborates closely with sugar mills and refineries to develop customised weighing and bagging solutions. By working with project managers and engineers in the design phase, the company ensures that systems are adapted to site layouts, throughput needs and dimensional constraints. Simulation testing is also available to validate hardware, software and data transfer.
Fourie elaborates that a common custom feature that sugar producers request is interfacing with peripheral equipment such as inline metal detectors that halt feeding to allow contaminants to be cleared, thereby minimising downtime and material waste. Additional requests include integrated test mass pieces for easier calibration; and control over peripheral equipment such as automatic bag placement and transfer mechanisms. without requiring additional programmable logic controllers.
The X-Act controller software, fully developed and supported in-house by Autotech, is highly customisable for various weighing applications. This allows the company to respond quickly to special requirements and operational changes, ensuring continuous improvement and adaptation to industry needs.
Autotech remains committed to continuous software development, enhancing both new applications and existing systems. Clients can also allow remote access options, enabling Autotech to monitor the weighing process and diagnose issues, ensuring optimal performance across both standard and customised applications.
Autotech has a long-standing presence in the sugar industry, supplying solutions across South Africa, Eswatini, Zambia, Egypt and Mauritius, with some of its bagging systems operating in the sugar industry for more than 20 years, demonstrating the company’s reliability and durability, Fourie concludes.
Comments
Press Office
Announcements
What's On
Subscribe to improve your user experience...
Option 1 (equivalent of R125 a month):
Receive a weekly copy of Creamer Media's Engineering News & Mining Weekly magazine
(print copy for those in South Africa and e-magazine for those outside of South Africa)
Receive daily email newsletters
Access to full search results
Access archive of magazine back copies
Access to Projects in Progress
Access to ONE Research Report of your choice in PDF format
Option 2 (equivalent of R375 a month):
All benefits from Option 1
PLUS
Access to Creamer Media's Research Channel Africa for ALL Research Reports, in PDF format, on various industrial and mining sectors
including Electricity; Water; Energy Transition; Hydrogen; Roads, Rail and Ports; Coal; Gold; Platinum; Battery Metals; etc.
Already a subscriber?
Forgotten your password?
Receive weekly copy of Creamer Media's Engineering News & Mining Weekly magazine (print copy for those in South Africa and e-magazine for those outside of South Africa)
➕
Recieve daily email newsletters
➕
Access to full search results
➕
Access archive of magazine back copies
➕
Access to Projects in Progress
➕
Access to ONE Research Report of your choice in PDF format
RESEARCH CHANNEL AFRICA
R4500 (equivalent of R375 a month)
SUBSCRIBEAll benefits from Option 1
➕
Access to Creamer Media's Research Channel Africa for ALL Research Reports on various industrial and mining sectors, in PDF format, including on:
Electricity
➕
Water
➕
Energy Transition
➕
Hydrogen
➕
Roads, Rail and Ports
➕
Coal
➕
Gold
➕
Platinum
➕
Battery Metals
➕
etc.
Receive all benefits from Option 1 or Option 2 delivered to numerous people at your company
➕
Multiple User names and Passwords for simultaneous log-ins
➕
Intranet integration access to all in your organisation