Bridgestone South Africa’s manufacturing plant showcases rubber innovation
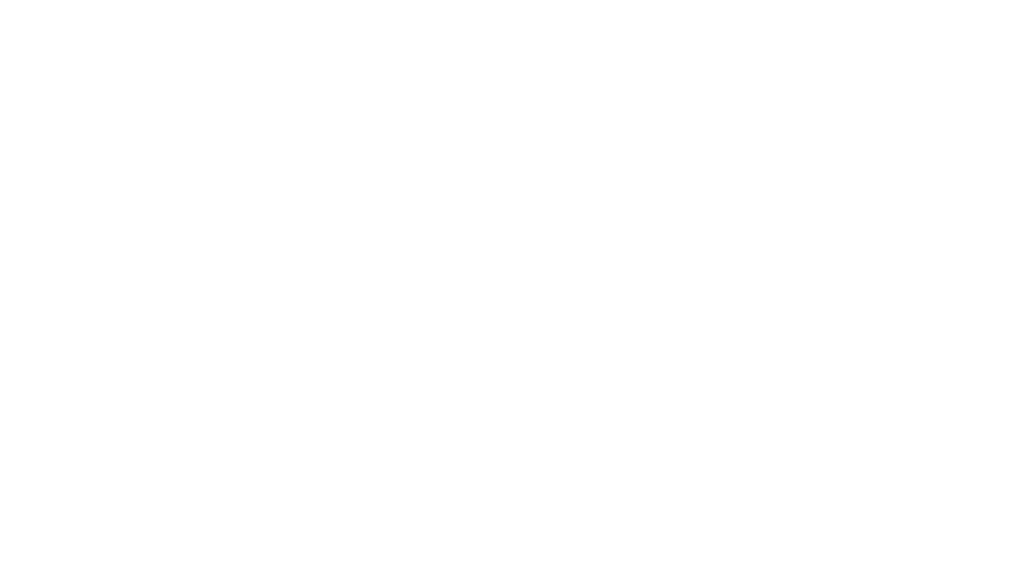
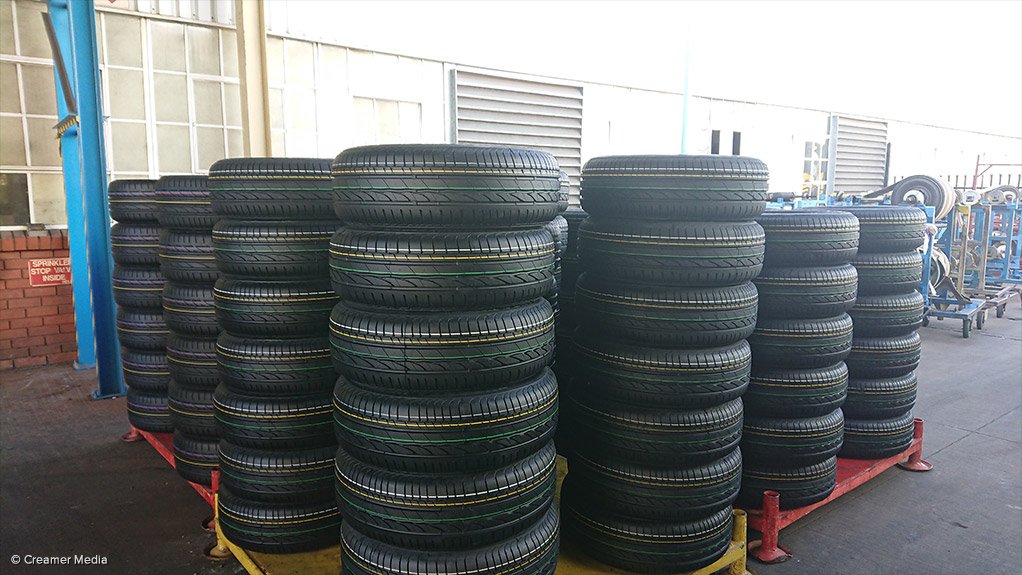
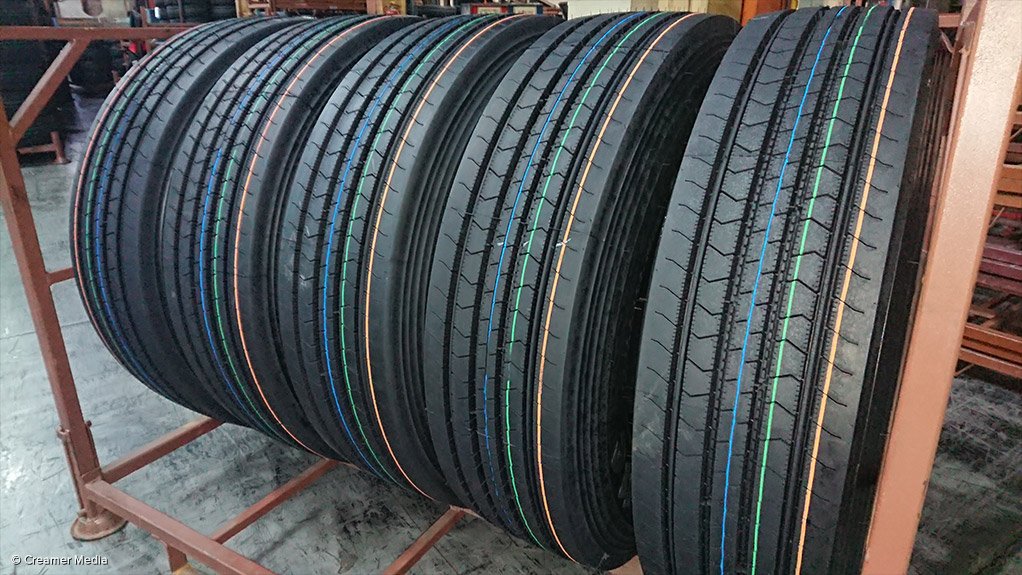
Bridgestone manufacturing plant, in Brits
Bridgestone manufacturing plant, in Brits
Tyre manufacturer Bridgestone South Africa on Wednesday hosted a media tour of its 186 027 m2 manufacturing facility in Brits, North West, to showcase how its technology has evolved from the 1950s to date.
Bridgestone manufactures passenger radial, light truck radial, truck and bus radial, and run flat tyres at the Brits facility, as a qualified original-equipment supplier to automotive brands such as BMW, Mercedes-Benz, Toyota, Volkswagen, Isuzu, Nissan and Ford.
The Brits plant produces about 5 550 passenger tyres a day, and goes through 1 700 raw rubber tons a month across the product portfolio, said Bridgestone South Africa manufacturing executive manager Ian Marsh.
Additionally, Bridgestone manufactures light tuck bias, truck and bus bias, agricultural bias, and off-road bias tyres, as well as pre-cure tread for retreading tyres, at its manufacturing facility in Port Elizabeth, in the Eastern Cape.
The Brits plant is one of six globally in the Bridgestone group to manufacture run flat tyres, which is tyre technology that allows a vehicle to keep driving for 80 km at 80 km/h even when air loss or a puncture is detected, eliminating the need to stop and change a tyre, while contributing to saving materials since spare tyres are not necessary.
Conventional tyres use pressurised air to support the weight of the vehicle. However, when the tyre is punctured, air escapes and the weight of the vehicle is no longer supported. This creates a flat tyre.
When a run-flat tyre is punctured, it loses air, but it continues to support the vehicle’s weight using the reinforced sidewalls.
Bridgestone also has eight retread factories across the country and in Namibia where truck and bus radial casings can be retread.
Meanwhile, original-equipment manufacturers and suppliers have a continuous demand for low rolling resistance tyres and, therefore, Bridgestone regularly upgrades the Brits facility’s equipment to be able to produce lower rolling resistance tyres, explained Bridgestone South Africa manufacturing renewal executive Dries Lottering.
In line with facility renewals and upgrades, Bridgestone recently started implementing the integrated work system (IWS) methodology in its factory, where a bottom-up management process is used, whereby employees take charge as equipment decision-makers, rather than executives who do not encounter the machinery as often, if at all.
The Brits facility employs 801 people.
Lottering says IWS has improved Bridgestone’s productivity to lower defect levels and quicker shift changeovers.
The Brits plant manufacturing process encompasses a raw materials section where natural rubber or synthetic rubber, as well as additives such as carbon black, are stored. This is followed by compound mixing of the raw materials, and then extrusion.
Thereafter, the process moves to component preparation which entails steel cord calendaring or fabric calendaring, tyre building, curing and, finally, quality checking and inspection.
For the compound mixing process, Bridgestone is in the process of upgrading to Variable Intermesh Clearance Mixing technology, which offers better heat distribution and enables low rolling resistance, while saving energy and delivering a higher-quality compound.
“The strength of the intermeshing design is in its ability to move materials aggressively within the mixing chamber, effectively shearing the mix, and owing to its surface area-to-volume ratio design characteristics, an enhanced ability to remove heat generated during the mixing process is achieved,” explained Bridgestone South Africa operations GM Barry Nigrini.
He noted that Bridgestone South Africa is busy preparing the Brits plant to bring in new steel calendaring technology, which will cut steel wires even thinner than with existing technology. These machines will be operational by 2020.
The steel within the tyre offers extra resistance and resilience, which is more often used in truck and bus tyres than passenger tyres. For fabric calendaring, the company prefers using polyester and rayon fabrics.
For quality checking and inspection, the plant uses X-ray machines to check the inside of the tyre for any defects.
Lottering concluded that the Bridgestone South Africa plants undergo continual renewals and upgrades to keep up with customer satisfaction standards and original-equipment manufacturer demands.
Comments
Press Office
Announcements
What's On
Subscribe to improve your user experience...
Option 1 (equivalent of R125 a month):
Receive a weekly copy of Creamer Media's Engineering News & Mining Weekly magazine
(print copy for those in South Africa and e-magazine for those outside of South Africa)
Receive daily email newsletters
Access to full search results
Access archive of magazine back copies
Access to Projects in Progress
Access to ONE Research Report of your choice in PDF format
Option 2 (equivalent of R375 a month):
All benefits from Option 1
PLUS
Access to Creamer Media's Research Channel Africa for ALL Research Reports, in PDF format, on various industrial and mining sectors
including Electricity; Water; Energy Transition; Hydrogen; Roads, Rail and Ports; Coal; Gold; Platinum; Battery Metals; etc.
Already a subscriber?
Forgotten your password?
Receive weekly copy of Creamer Media's Engineering News & Mining Weekly magazine (print copy for those in South Africa and e-magazine for those outside of South Africa)
➕
Recieve daily email newsletters
➕
Access to full search results
➕
Access archive of magazine back copies
➕
Access to Projects in Progress
➕
Access to ONE Research Report of your choice in PDF format
RESEARCH CHANNEL AFRICA
R4500 (equivalent of R375 a month)
SUBSCRIBEAll benefits from Option 1
➕
Access to Creamer Media's Research Channel Africa for ALL Research Reports on various industrial and mining sectors, in PDF format, including on:
Electricity
➕
Water
➕
Energy Transition
➕
Hydrogen
➕
Roads, Rail and Ports
➕
Coal
➕
Gold
➕
Platinum
➕
Battery Metals
➕
etc.
Receive all benefits from Option 1 or Option 2 delivered to numerous people at your company
➕
Multiple User names and Passwords for simultaneous log-ins
➕
Intranet integration access to all in your organisation