Coated pumps offer long-term benefits
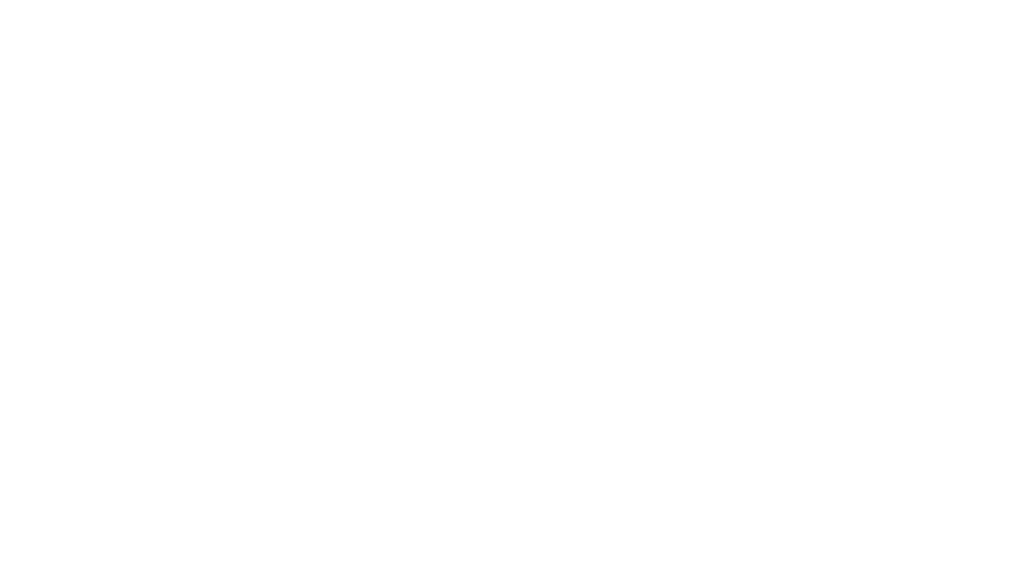
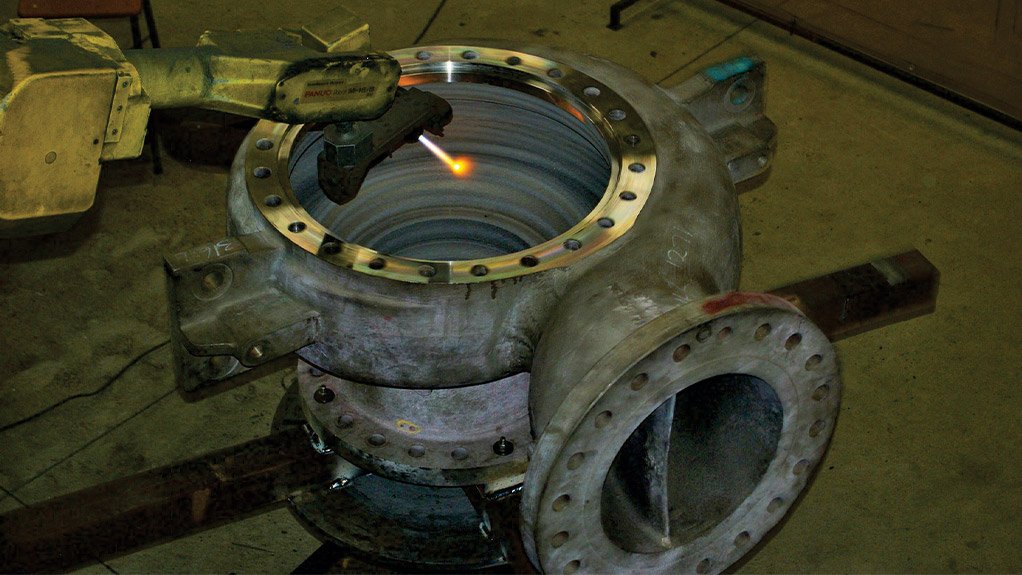
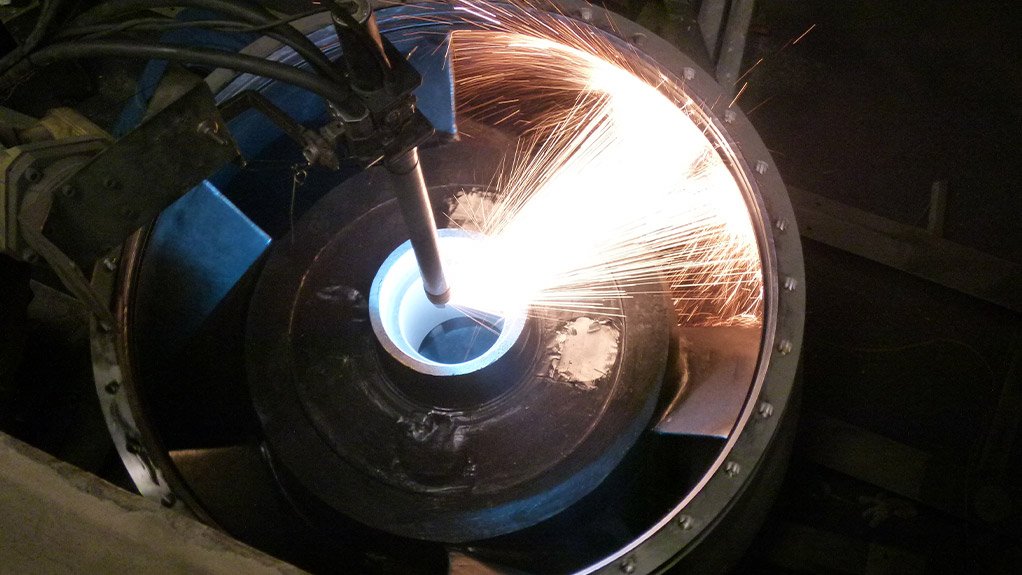
ENVIRONMENT CONSCIOUS The type of coating used on the pumps will depend on the environment the pumps are used in
LONGER LIFE Coatings can extend the lifespan of components
Although the thermal spray coating of pumps can add about 20% more to the capital costs of the pumps, Olifantsfontein-based thermal spray coating technology specialist Thermaspray production manager Paul Young says this will save significantly on operational costs in the long term.
“A thermal spray coated pump may last up to three to five times longer than an uncoated pump, and then some of the pump parts, such as impellers and rings, may still be salvageable for reuse.”
He explains that the type of coating used on the pumps will depend on the environment the pumps are used in, for example, how abrasive or corrosive the water is. “There are polymer coatings that are better suited to specific corrosive environments than thermal spray coatings. However, these may not be perfectly suited to environments where there is a significant amount of abrasion.”
Thermal spray coatings include pure metals, such as copper; metal alloys, such as stainless steel; ceramics, such as zirconia; and ceramic metal composite or carbide coatings, such as tungsten carbide.
Thermaspray offers a variety of thermal spray coatings for pumps as nearly any material that is produced in wire or powder form can be processed into a coating.
However, Young mentions that the coating equivalent does not necessarily have the same properties as the original material as there are composite coatings that have unique functional properties which are produced by combining different materials and processes.
Thermaspray coatings extend the life span of components, especially when operating in harsh environments, says Young.
He explains that a worn component need not be discarded and replaced by a new one as, in some instances, the component can be refurbished to its original specification, after which the component life may be extended when coated with a suitable Thermaspray material.
New Equipment
Thermaspray received its 4 kW fibre-coupled diode laser-cladding machine last month and it is being commissioned at the moment, with the company planning to start production next month.
The technology solution consists of the laser machine, supplemented by various cladding optics, including internal-diameter cladding capabilities. These optics are mounted on a six-axis robotic manipulator that ensures repeatability and process stability.
Young explains that laser cladding is a weld buildup process that applies primarily metallic overlay coatings to metallic surfaces. These overlays vary in purpose, from severe erosive protection to high-temperature corrosion protection.
“Owing to the metallurgically bonded overlay, laser-clad coatings are resistant to impact, so the technology can be used in slurry pump environments, as well as impact-prone applications.”
Moreover, the laser cladding of shafts is possible, as the process has significantly less heat input, compared with traditional welding processes; this significantly reduces any risk of component distortion when refurbishing worn or mis-machined parts.
He notes that extremely low dilution between the overlay material and component surface is another distinct advantage of laser cladding over other traditional welding processes.
“Less material needs to be used to achieve the desired surface properties, which means that components can be restored to near-net shape, eliminating the need for extensive machining or grinding after restoration.”
Laser cladding enhances the surface of components to last longer, making this technology ideally suited for the refurbishment of worn components to original-equipment manufacturer specifications, as well as for surface enhancement of new components, he concludes.
Comments
Announcements
What's On
Subscribe to improve your user experience...
Option 1 (equivalent of R125 a month):
Receive a weekly copy of Creamer Media's Engineering News & Mining Weekly magazine
(print copy for those in South Africa and e-magazine for those outside of South Africa)
Receive daily email newsletters
Access to full search results
Access archive of magazine back copies
Access to Projects in Progress
Access to ONE Research Report of your choice in PDF format
Option 2 (equivalent of R375 a month):
All benefits from Option 1
PLUS
Access to Creamer Media's Research Channel Africa for ALL Research Reports, in PDF format, on various industrial and mining sectors
including Electricity; Water; Energy Transition; Hydrogen; Roads, Rail and Ports; Coal; Gold; Platinum; Battery Metals; etc.
Already a subscriber?
Forgotten your password?
Receive weekly copy of Creamer Media's Engineering News & Mining Weekly magazine (print copy for those in South Africa and e-magazine for those outside of South Africa)
➕
Recieve daily email newsletters
➕
Access to full search results
➕
Access archive of magazine back copies
➕
Access to Projects in Progress
➕
Access to ONE Research Report of your choice in PDF format
RESEARCH CHANNEL AFRICA
R4500 (equivalent of R375 a month)
SUBSCRIBEAll benefits from Option 1
➕
Access to Creamer Media's Research Channel Africa for ALL Research Reports on various industrial and mining sectors, in PDF format, including on:
Electricity
➕
Water
➕
Energy Transition
➕
Hydrogen
➕
Roads, Rail and Ports
➕
Coal
➕
Gold
➕
Platinum
➕
Battery Metals
➕
etc.
Receive all benefits from Option 1 or Option 2 delivered to numerous people at your company
➕
Multiple User names and Passwords for simultaneous log-ins
➕
Intranet integration access to all in your organisation