Manufacturing company stresses expert tanker control systems benefits
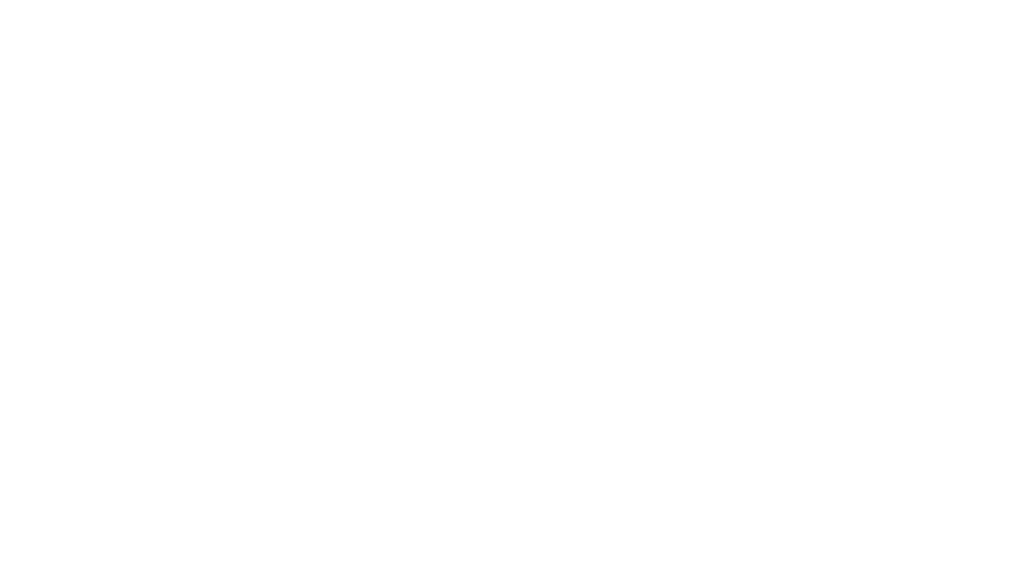
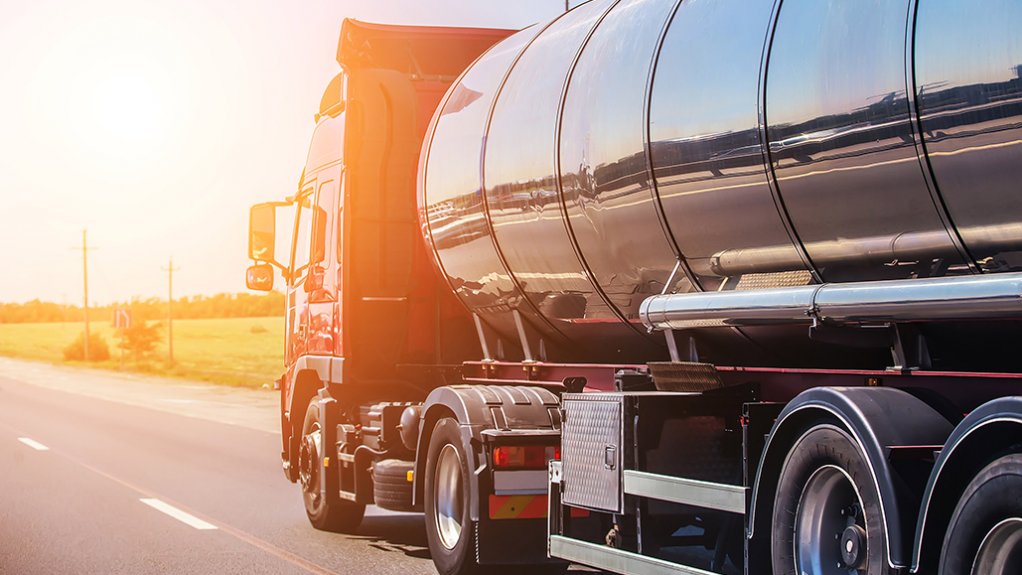
PRUDENT TANKER LOADING Both top-loading and bottom-loading for tankers are made more efficient and safer with expert control systems
Automation and expert control systems can provide health and safety benefits for tanker filling practices, says engineering, integration and manufacturing company Iritron divisional manager Gerhard Greeff.
“Expert control systems can make top-loading safer by implementing additional instrumentation inside of tanks to detect entrained liquids and vapour concentration outside of acceptable limits. These instruments are, however, expensive and less cost effective than changing pipework to enable bottom-loading”.
In South Africa, companies filling tanks at loading depots generally load the tank from the top – referred to as top-loading procedure – with the truck driver standing on top of the tanker and inserting the loading arm of the depot installation through the manhole into the tanker compartment, or in tank-farms where liquid is pumped into tanks through pipes entering the top of the tank.
He adds that there has not been any significant effort from local companies to move away from top-loading towards bottom-loading, for which the driver will fill the tanker through a system of valves and fittings mounted under the tanker or tank.
Owing to the fact that many local tanker users are smaller companies with limited automation on logistics and storage elements, there has been a lack of pressure to change to implement bottom-loading procedures.
Local safety standards also do not make bottom-loading mandatory, he adds.
Safer Top-Loading & Bottom-Loading
Safety procedures for top-loading are followed to avoid sparks or open flames that can ignite flammable vapour-air mixtures.
For corrosive liquids, safety procedures are mostly focused on keeping people away from tank vents to avoid entrained liquid droplets being inhaled or falling on them.
Greeff acknowledges that, in Europe, the top-loading procedure is less common, owing to its health and safety risks.
He notes that, for the bottom-loading process, the driver is not required to ascend a tall tanker, which is required for top-loading.
Bottom-loading also follows a closed-loop process that reduces the risk of static electricity occurrence, which may cause a spark that can ignite a fuel and oxygen mix.
It is also a much faster loading process, as the driver can safely load more than one tanker container at a time using an automated system.
Automation and Expert Controls
Both loading methods are made safer with expert control systems.
“Linked with level sensors and high-level alarms to ensure no over-fill, and flow valves to regulate or stop flow when required, expert systems can be used to make sure that vapour concentrations do not reach flammable levels, and overflow is prevented for top-loading.
“For bottom-loading, level and flow will be controlled in a similar manner, but no sensors will be required to monitor entrained liquid or vapour and air concentration,” adds Greeff.
Expert control systems make a case for safer, environmentally friendlier tanker loading processes by providing systems that control the flammable and corrosive liquid discharge process and in-tank meters, valves, vapour and complete tanker control systems.
Supplying, configuring and installing a wholly automated tanker control system allows for controlling and monitoring any aspect of the tank loading process in a safe manner, he notes.
“With a control system, you can measure the accuracy of the product load, type, volume, overfill prevention, in-tank pressure monitoring, automated valve control and levelling, venting system and more. The benefits of this automation – other than the health, safety and environmental aspects – are less product waste and a more cost-effective loading process.”
Automated systems reduce the risk of injury and explosion, as a person is not required to manually monitor the filling from the risk area, in addition to conducting monitoring with an intelligent system.
Such a system reduces the risk of entrained liquid or flammable vapour concentration reaching the environment, which can create explosions or localised “acid rain”.
“Using flow valves and limit switches, automated systems will also reduce the risk of starting pumps without securing pipes and connections. Automated systems can also ensure that the correct tanks are being filled by monitoring valve positions. This is especially critical in locations where oxidising agents and reducing agents are delivered in bulk.”
Encouraging Safer Practices
Greeff contends that, while safer regulations would be preferable, market education and awareness are key factors in encouraging companies to use safety practices.
Considering the importance placed on ensuring fatality-free days in most industrial companies, switching to safer practices “catapults a company towards establishing an environment that is conductive to safe, injury- and, ultimately, fatality-free days”.
He stresses the importance of safer practices, and that international investors demand a focus on environmental, social and governance (ESG) strategy, where responsible procedures and policies are expected before investments can take place.
“Harmful and expensive liquid spillages, driver injuries while loading tankers, fires and explosions are all hazards that can be avoided by adopting safer and more environment-friendly operating procedures when loading tankers. The automation of this process allows for a derisked and less hazardous method of loading tankers contributing to a sustainable ESG strategy,” he concludes.
Comments
Press Office
Announcements
What's On
Subscribe to improve your user experience...
Option 1 (equivalent of R125 a month):
Receive a weekly copy of Creamer Media's Engineering News & Mining Weekly magazine
(print copy for those in South Africa and e-magazine for those outside of South Africa)
Receive daily email newsletters
Access to full search results
Access archive of magazine back copies
Access to Projects in Progress
Access to ONE Research Report of your choice in PDF format
Option 2 (equivalent of R375 a month):
All benefits from Option 1
PLUS
Access to Creamer Media's Research Channel Africa for ALL Research Reports, in PDF format, on various industrial and mining sectors
including Electricity; Water; Energy Transition; Hydrogen; Roads, Rail and Ports; Coal; Gold; Platinum; Battery Metals; etc.
Already a subscriber?
Forgotten your password?
Receive weekly copy of Creamer Media's Engineering News & Mining Weekly magazine (print copy for those in South Africa and e-magazine for those outside of South Africa)
➕
Recieve daily email newsletters
➕
Access to full search results
➕
Access archive of magazine back copies
➕
Access to Projects in Progress
➕
Access to ONE Research Report of your choice in PDF format
RESEARCH CHANNEL AFRICA
R4500 (equivalent of R375 a month)
SUBSCRIBEAll benefits from Option 1
➕
Access to Creamer Media's Research Channel Africa for ALL Research Reports on various industrial and mining sectors, in PDF format, including on:
Electricity
➕
Water
➕
Energy Transition
➕
Hydrogen
➕
Roads, Rail and Ports
➕
Coal
➕
Gold
➕
Platinum
➕
Battery Metals
➕
etc.
Receive all benefits from Option 1 or Option 2 delivered to numerous people at your company
➕
Multiple User names and Passwords for simultaneous log-ins
➕
Intranet integration access to all in your organisation