Facility upgrades help to ramp up supply
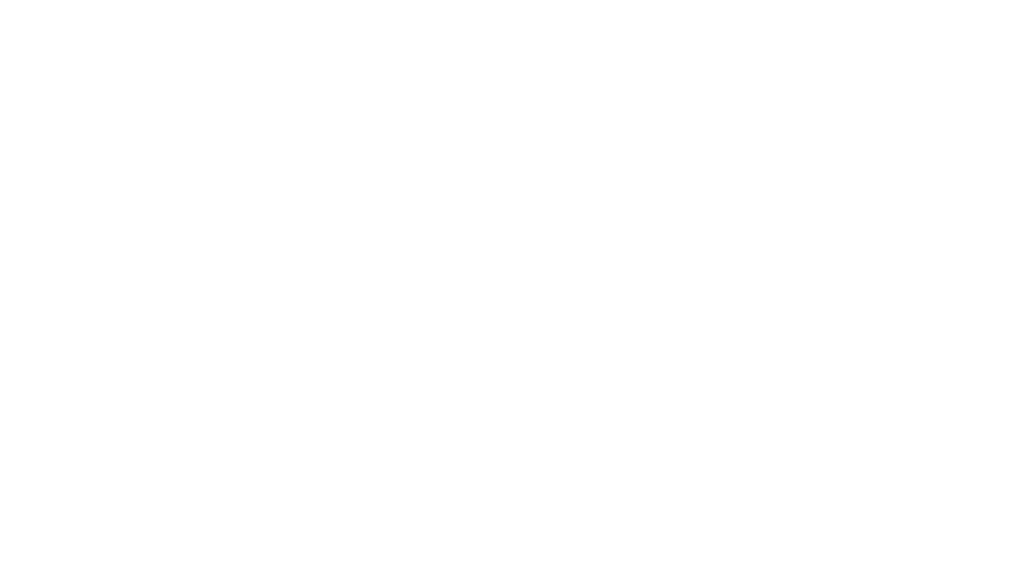
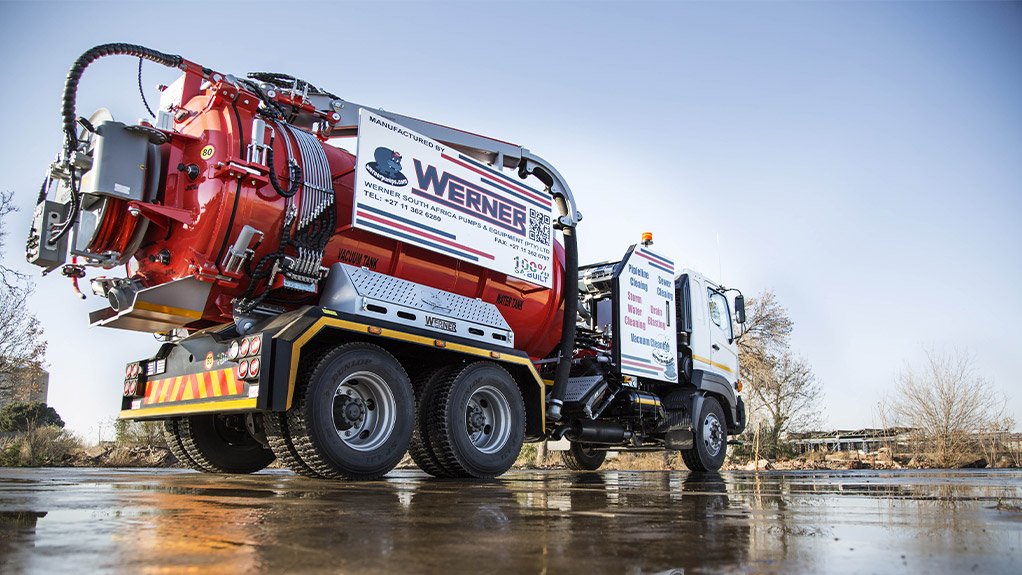
UNDER THE PUMP Werner Pumps has managed to increase its turnaround time, to relieve the pressure of increased demand, by upgrading its facilities
Local high-pressure pumps supplier Werner South Africa Pumps & Equipment has successfully improved its turnaround time from between four and six months to between two and three months to manufacture a truck-mounted pump system, depending on the unit ordered.
“This is subsequent to the implementation of an ongoing facilities upgrade, which commenced in 2016,” says Werner Pumps MD Sebastian Werner.
Werner Pumps manufactures and supplies high-pressure pumps and high-pressure jetting units – from 2.2 kW electric skid units to 12-cylinder diesel-powered units mounted either on trailers or trucks.
Werner explains that the upgrades include a new spray-paint or spraying booth, a new electronics facility for in-house design and testing, as well as a new hydraulics department for the design and assembly of the hydraulics components on its units.
The upgrades also include two under-roof welding booths, with a new tank welding rotator, which allow for the tanks to be easily and smoothly rotated while the welder completes each weld. Werner suggests that the quality and uniformity of the weld have been more evident since these additions.
“The spray-paint booth will enable us to have a better and more appealing finish on our products, as well as decrease the environmental impact when spraying,” says Werner.
He adds that the new spray-paint booth is large enough to accommodate two trucks simultaneously.
The electronics and hydraulics departments allow for improved in-house design and assembly, which also negates the need to import parts or wait on distributors. “Being self-sufficient has made us more efficient, and uniform in our assembly,” says Werner.
He adds that the company currently has about 11 trucks on order for the year and has had enquiries for more orders.
The products on order include trailer, vacuum, combination and recycling units, which are due to be used in municipal water applications and at State-owned power utility Eskom’s power stations.
Werner explains that the ash which is a very evident by-product of burning coal at power stations, needs to be removed from the power stations’ hoppers. A vacuum truck is best suited to remove the ash and deposit it safely at an ash disposal site.
“As an International Standards Organisation-accredited company comes the push to improve one’s environmental ratings,” he says, adding that the company considered not only its environmental impact but also that of the product it supplies to customers.
For example, Werner Pumps’ Amanzi unit repurposes the water captured when cleaning a sewer or stormwater line – through an onboard filtration process – allowing for a more economical and water-conscious pumping process.
Werner explains that instead of using clean drinking water, the unit uses the grey water it produces to complete the job.
Assembly Process
The process of assembling the truck- mounted system begins by building a suitable tank, and then a subframe is manufactured to support and attach the tank to the body. The subframe reinforces the body so that it can maintain the weight of the tank.
Further fittings are then installed, which allow for the tank to be tilted or lowered for the removal of waste in the tanks. Once the fittings are attached to the truck body, the pumps – a high-pressure pump and a high-pressure vacuum pump – are installed at the front of the subframe. The necessary hydraulics and electrical fittings are then fitted to the pumps and components, which then completes the skid.
Werner stresses that the company has opted for a hydraulic pump system instead of a fan belt-driven system: “It gives you more power output, is quieter and, overall, a safer system to use.”
He enthuses that the company offers a maintenance plan in the form of a booklet that customers keep with them. Service on the current pump system is done every 350 hours.
“We also conduct one or two training days, where customers would bring the operator to our Springs offices, and we train them on how to use the pumps and hydraulics or booms.”
Werner adds that the factory has a pool that is used for practical training, where an operator would be shown how to jet and vacuum in a real-life water situation, further quipping that this also saves water.
Subsequent to the training, an instructor is made available to go out to site for a week to ensure that the operator has been adequately trained, and is available for any follow-up questions or to address any possible situations.
Werner explains that the company has begun to offer a rental option, whereby customers can rent a unit of equal capacity or function from Werner Pumps until their order is completed.
“If there are unexpected delays, we offer the rental unit to our clients to bridge any gap and remove any inconvenience,” concludes Werner.
Comments
Press Office
Announcements
What's On
Subscribe to improve your user experience...
Option 1 (equivalent of R125 a month):
Receive a weekly copy of Creamer Media's Engineering News & Mining Weekly magazine
(print copy for those in South Africa and e-magazine for those outside of South Africa)
Receive daily email newsletters
Access to full search results
Access archive of magazine back copies
Access to Projects in Progress
Access to ONE Research Report of your choice in PDF format
Option 2 (equivalent of R375 a month):
All benefits from Option 1
PLUS
Access to Creamer Media's Research Channel Africa for ALL Research Reports, in PDF format, on various industrial and mining sectors
including Electricity; Water; Energy Transition; Hydrogen; Roads, Rail and Ports; Coal; Gold; Platinum; Battery Metals; etc.
Already a subscriber?
Forgotten your password?
Receive weekly copy of Creamer Media's Engineering News & Mining Weekly magazine (print copy for those in South Africa and e-magazine for those outside of South Africa)
➕
Recieve daily email newsletters
➕
Access to full search results
➕
Access archive of magazine back copies
➕
Access to Projects in Progress
➕
Access to ONE Research Report of your choice in PDF format
RESEARCH CHANNEL AFRICA
R4500 (equivalent of R375 a month)
SUBSCRIBEAll benefits from Option 1
➕
Access to Creamer Media's Research Channel Africa for ALL Research Reports on various industrial and mining sectors, in PDF format, including on:
Electricity
➕
Water
➕
Energy Transition
➕
Hydrogen
➕
Roads, Rail and Ports
➕
Coal
➕
Gold
➕
Platinum
➕
Battery Metals
➕
etc.
Receive all benefits from Option 1 or Option 2 delivered to numerous people at your company
➕
Multiple User names and Passwords for simultaneous log-ins
➕
Intranet integration access to all in your organisation