Tech tackles filling challenges
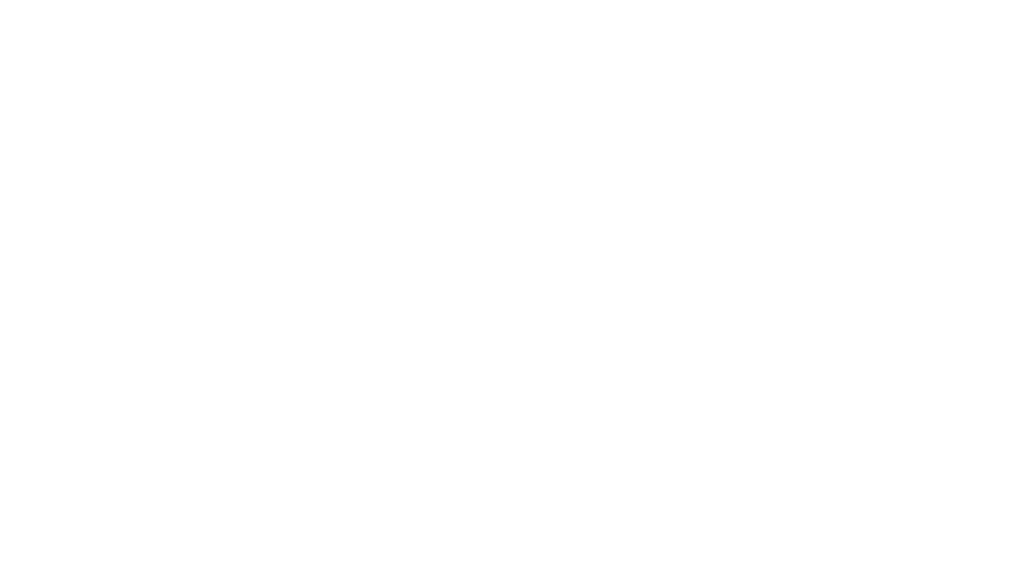
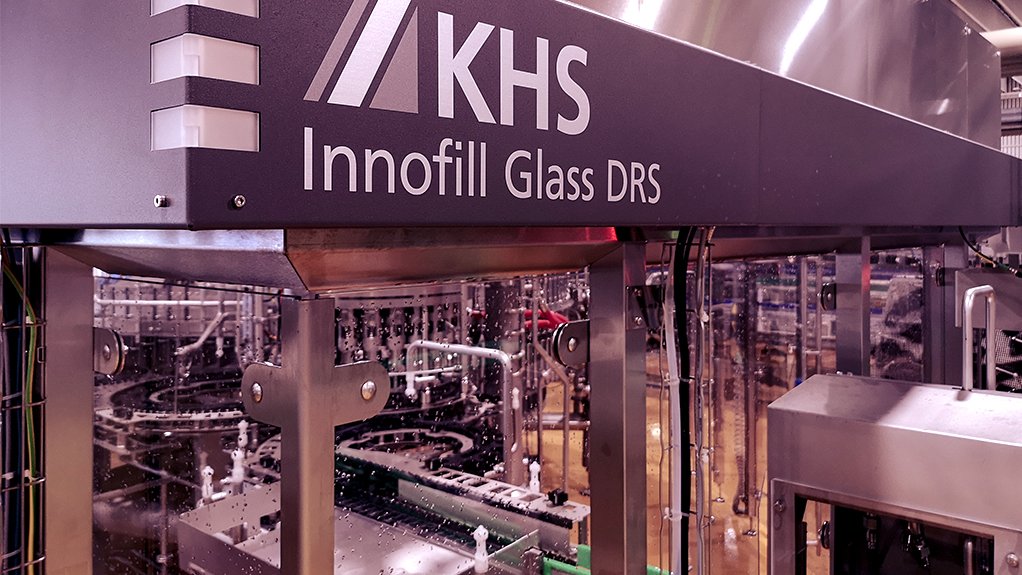
NNOFILL GLASS DRS ECO FILLING SYSTEM The Innofill Glass DRS ECO filling system allows breweries the benefit of a low O2 filling level
For modern-day brewers of trend and light beers, it is a common challenge trying to instil a tolerance to oxygen (O2) pickup, as this phenomenon has substantial negative impacts on the quality of a beer.
This means that, when a beer becomes oxidised by the process of O2 pickup – which can occur during the beer production process when malt is crushed, or when O2 infiltrates seals on crown corks – its flavour profile depreciates, and the beer develops an undesirable taste.
There is, however, a solution to the phenomenon of O2 pickup in beer, which has been created by renowned manufacturer of filling and packing equipment for the beverage, food, and non-beverage sectors KHS Group.
Remarkable Beer Quality
The “cutting-edge” technology assists breweries, during beer production, to obtain low O2 pickup and, therefore, an enhanced, reliable quality of beer. KHS Group’s Innofill Glass DRS ECO filling system uses additives such as ascorbic acid and bisulphite. The Innofill Glass DRS ECO filling system allows breweries the benefit of a low O2 filling level on an “unprecedented scale”.
Reduced O2, Reduced Carbon Dioxide
The new plant engineering allows less O2 to penetrate the beer, and, in doing so, consumes less carbon dioxide (CO2). During the process of bottle filling, a new hollow probe filler enables greatly reduced CO2 consumption on the one hand and even lower O2 pickup on the other.
The container is first evacuated through the vacuum channel and then purged with CO2 gas. A KHS-patented purging process is used to this end. The container is then pressurised to filling pressure with the inert gas as usual. This makes an extremely low total O2 pickup of 20 ppb possible at a CO2 consumption of 160 g/hl.
Therefore, the total O2 pickup required can be selected as needed. This means that a range of automatic product type conversions can be set with maximum CO2 savings for an especially O2-sensitive, cold-hopped beer, a dark beer insensitive to oxygen, or even for totally different filling products.
Alternative O2-Reduction Methods for Flavour Stability
Reducing O2 pickup is an important step in achieving an enhanced and strengthened flavour stability in beers. For this reason, tanks are pressurised with inert gas and are often cleaned in the presence of this gas to prevent any loss. If the inert gas is CO2, only acidic cleaning is possible on retention of the gas. If nitrogen (N2) is used, the amount of dissolved N2 in the beer must be observed to achieve an undisrupted filling performance.
Essentially, tank pressures should be selected so that they are as low as possible to match the partial CO2 pressure of the beer and so that pumps can be used for any necessary pressure increases. During filtration the use of de-aerated water is strongly recommended. An O2 content of below 0.2 mg/ℓ is ideal – also for purging water during flash pasteurisation, for example – as non-de-aerated water contains about 10 mg/ℓ.
It is safe to assume that breweries must buy their CO2, and owing to the rising prices in doing so, this is a growing cost factor. A lower consumption for the filled bottle means that the production process will be more efficient. Additionally, the lower the O2 pickup, the better the product quality.
KHS states that it has established a perfect combination to address both issues through its Innofill Glass DRS ECO.
Comments
Press Office
Announcements
What's On
Subscribe to improve your user experience...
Option 1 (equivalent of R125 a month):
Receive a weekly copy of Creamer Media's Engineering News & Mining Weekly magazine
(print copy for those in South Africa and e-magazine for those outside of South Africa)
Receive daily email newsletters
Access to full search results
Access archive of magazine back copies
Access to Projects in Progress
Access to ONE Research Report of your choice in PDF format
Option 2 (equivalent of R375 a month):
All benefits from Option 1
PLUS
Access to Creamer Media's Research Channel Africa for ALL Research Reports, in PDF format, on various industrial and mining sectors
including Electricity; Water; Energy Transition; Hydrogen; Roads, Rail and Ports; Coal; Gold; Platinum; Battery Metals; etc.
Already a subscriber?
Forgotten your password?
Receive weekly copy of Creamer Media's Engineering News & Mining Weekly magazine (print copy for those in South Africa and e-magazine for those outside of South Africa)
➕
Recieve daily email newsletters
➕
Access to full search results
➕
Access archive of magazine back copies
➕
Access to Projects in Progress
➕
Access to ONE Research Report of your choice in PDF format
RESEARCH CHANNEL AFRICA
R4500 (equivalent of R375 a month)
SUBSCRIBEAll benefits from Option 1
➕
Access to Creamer Media's Research Channel Africa for ALL Research Reports on various industrial and mining sectors, in PDF format, including on:
Electricity
➕
Water
➕
Energy Transition
➕
Hydrogen
➕
Roads, Rail and Ports
➕
Coal
➕
Gold
➕
Platinum
➕
Battery Metals
➕
etc.
Receive all benefits from Option 1 or Option 2 delivered to numerous people at your company
➕
Multiple User names and Passwords for simultaneous log-ins
➕
Intranet integration access to all in your organisation