Impact of load on miniaturised motor selection highlighted
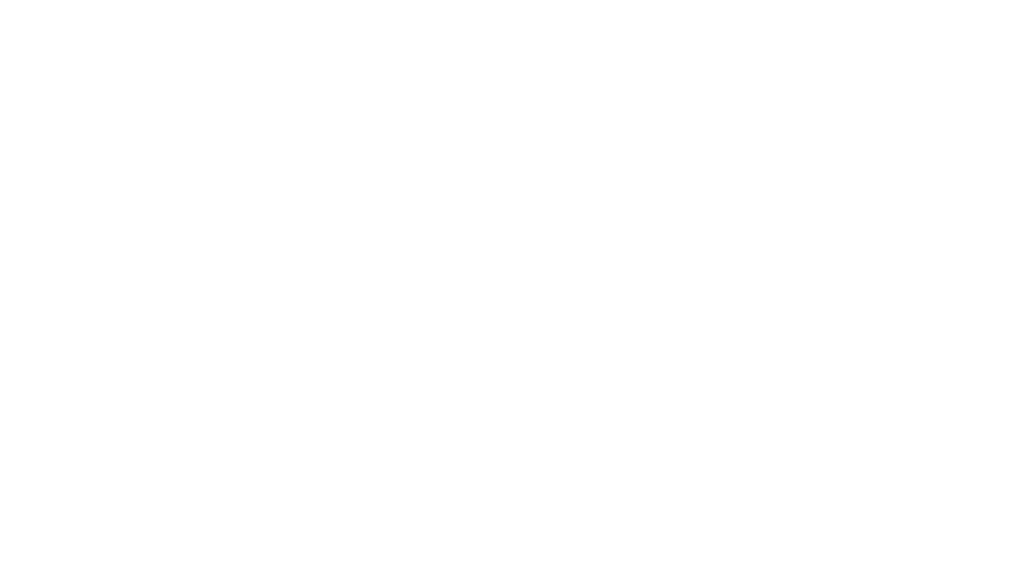
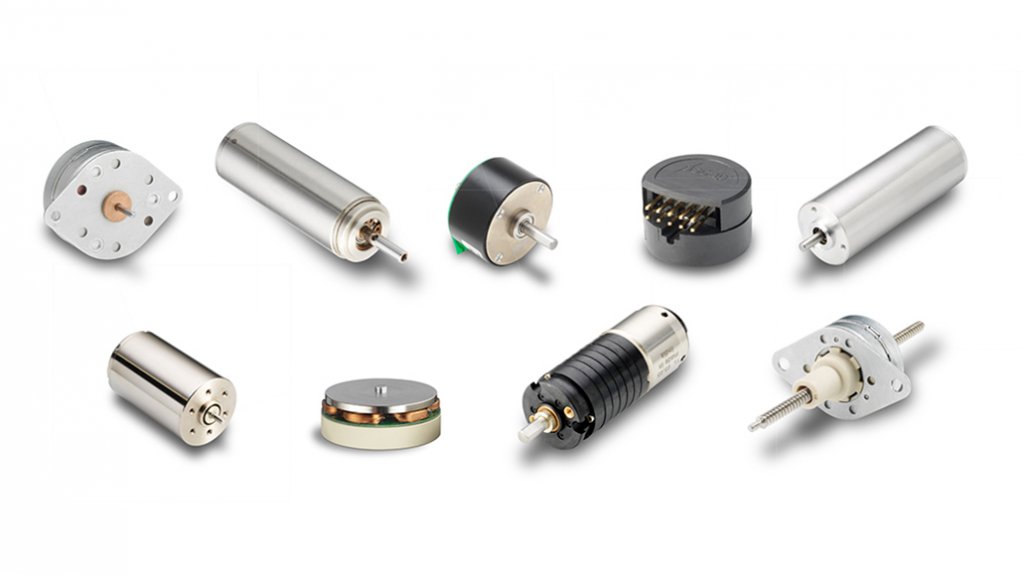
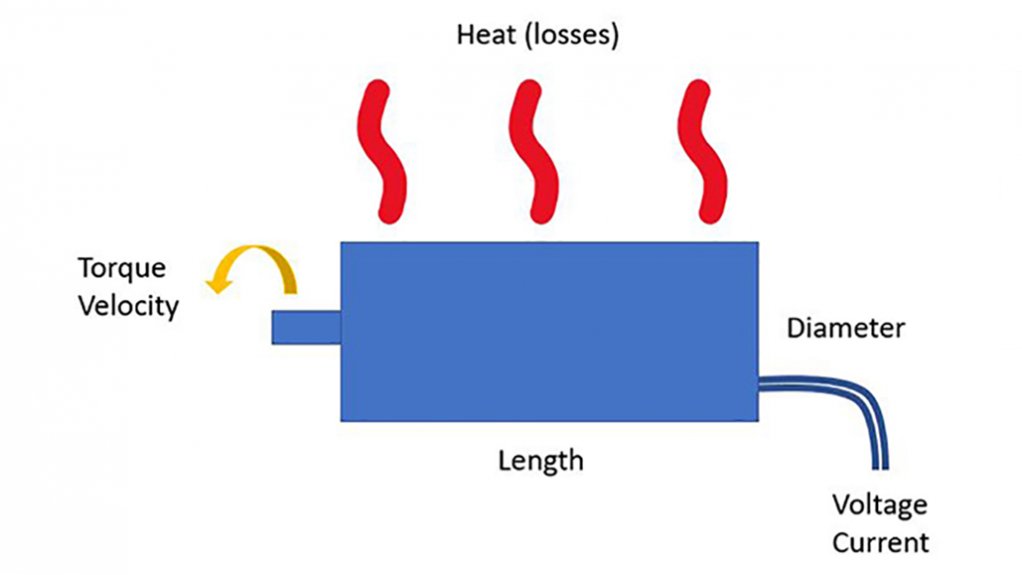
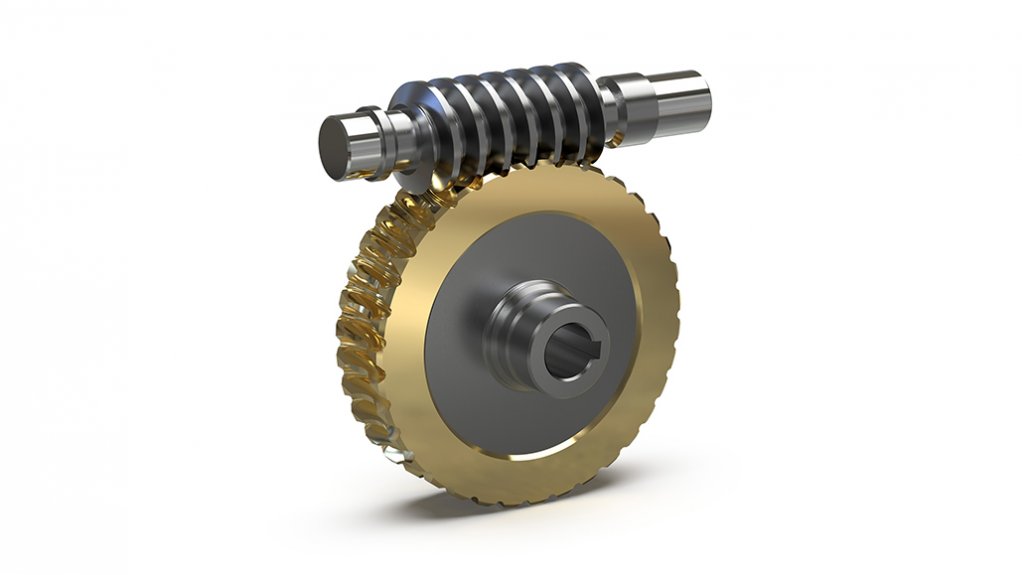
MINIATURE MOTOR When selecting a miniature motor, understanding the different loads acting on the motor is key to achieving the best design
SIMPLIFIED MODEL Torque load on a simplified model of a brush DC motor
WORM GEAR A worm gear consisting of a worm shaft (driven by the motor) and a bronze worm wheel
When selecting a miniature motor, understanding the different loads acting on the motor is key to achieving the best design.
Therefore, understanding the torque load is essential to define the necessary motor power, while understanding radial and axial loads is required to achieve optimal performance and longevity through the most appropriate motion solution specification.
As a result of the wider impact of different loads on the application, it is important to achieve a collaborative process between the original-equipment manufacturer (OEM) and motion solution engineering teams during specification and development, says motion solutions provider Portescap application engineer Valentin Raschke.
“Torque is the rotational force generated by a motor during its operation and is ever-present across motion solution applications in the conversion of electrical energy into mechanical energy. In most cases, when selecting a motor, the required torque, as well as velocity, must be understood over the application’s entire motion cycle, as the motor needs to provide the necessary mechanical power without overheating,” Raschke explains.
In certain applications, the motor or gearbox must not only provide a certain torque to drive the load but must also support a radial load, Raschke adds, noting that examples of a radial load – that is a force acting perpendicular to the motor shaft’s axis of rotation – include a belt drive, driving an axis parallel to the motor, or a diaphragm pump. In the latter case, a piston, mounted on the motor shaft, creates up-and-down movement to facilitate liquid flow, applying a radial load on the motor in the process.
The radial load is relevant, owing to its impact on bearing choice, Raschke says, noting that for a brush direct current (dc) or stepper motor, there are two standard bearing options such as sleeve bearings or ball bearings.
Sleeve bearings typically support a lower radial load than ball bearings, and offer a shorter lifetime, but this is offset by their reduced cost. Using sleeve bearings is sufficient for most motor applications where cost is important and low or no radial load is present.
However, Raschke notes that for applications which have higher radial load demands, such as the belt drive and diaphragm pump examples, “using at least one ball bearing, positioned closest to the point of load, can significantly extend lifetime”.
In contrast, Raschke explains that brushless dc motors (BLDC) typically use two ball bearings.
“As BLDC motors are by design equipped with electric commutation (instead of a mechanical commutation as for brush dc motors), their lifetime is mainly dependent on the reliability of the bearing system.”
Raschke adds that using ball bearings for BLDC motors therefore enables a long lifetime even at high speeds.
“As part of the specification, a motor manufacturer will typically define a maximum radial dynamic force for a minimum motor lifetime at a specific speed. However, this depends on the size of the bearings used, the distance between the two ball bearings in the motor, and the point where the radial load is applied. “Typically, a long motor with oversized ball bearings supports a larger radial load than a shorter motor,” Raschke comments.
Further, in terms of dynamic and static load challenges, Raschke says that the axial load represents load bearing in the direction of the motor axis which, along with a radial load, “we see, for example, when using a worm gear”.
“It’s often mandatory to support significant axial loads with ball bearings rather than sleeve bearings because of the higher demands. However, calculating a motor’s maximum recommended dynamic axial load depends on the ball bearings used, their arrangement, and preload,” Raschke adds.
For a BLDC motor, the dynamic axial load is typically supported by the front ball bearing which is preloaded from inside the motor. If an axial push load is acting on the motor, the preload on the front ball bearing is reduced.
“This can lead to additional radial play, negatively impacting the lifetime, as well as causing vibration and noise. In the opposite case, an axial pull load, which acts in the same direction as the internal preload, will also increase stress,” Raschke says.
A static axial load can also be applied to the motor, usually when an additional component, such as a pinion, is press-fitted onto the shaft. Exceeding the maximum recommended static load could lead to permanent deformation of the ball bearings and race, resulting in reduced life as well as increased noise and vibration of the bearing. Therefore, Raschke urges that specification of the motor “should not be made in isolation of additional integrated components”.
Raschke adds that when specifying a motion solution, “it is vital to discuss how it will integrate with the application as a whole, as different loads will have a significant impact on a motor’s performance, reliability and lifetime”.
“Combining the need to effectively handle various torque loads with the wider criteria of motion solution specification, confirms why a collaborative approach between the motion designer and the OEM engineering team is crucial from the outset,” Raschke notes, adding that a dedicated motion solution provider like Portescap supports customers in capturing the full picture of the loads experienced by the motor in each application.
“To ensure that the solution fulfils the application requirements and achieves optimum operational value, a partnership with a motion solution specialist is crucial,” Raschke concludes.
Comments
Press Office
Announcements
What's On
Subscribe to improve your user experience...
Option 1 (equivalent of R125 a month):
Receive a weekly copy of Creamer Media's Engineering News & Mining Weekly magazine
(print copy for those in South Africa and e-magazine for those outside of South Africa)
Receive daily email newsletters
Access to full search results
Access archive of magazine back copies
Access to Projects in Progress
Access to ONE Research Report of your choice in PDF format
Option 2 (equivalent of R375 a month):
All benefits from Option 1
PLUS
Access to Creamer Media's Research Channel Africa for ALL Research Reports, in PDF format, on various industrial and mining sectors
including Electricity; Water; Energy Transition; Hydrogen; Roads, Rail and Ports; Coal; Gold; Platinum; Battery Metals; etc.
Already a subscriber?
Forgotten your password?
Receive weekly copy of Creamer Media's Engineering News & Mining Weekly magazine (print copy for those in South Africa and e-magazine for those outside of South Africa)
➕
Recieve daily email newsletters
➕
Access to full search results
➕
Access archive of magazine back copies
➕
Access to Projects in Progress
➕
Access to ONE Research Report of your choice in PDF format
RESEARCH CHANNEL AFRICA
R4500 (equivalent of R375 a month)
SUBSCRIBEAll benefits from Option 1
➕
Access to Creamer Media's Research Channel Africa for ALL Research Reports on various industrial and mining sectors, in PDF format, including on:
Electricity
➕
Water
➕
Energy Transition
➕
Hydrogen
➕
Roads, Rail and Ports
➕
Coal
➕
Gold
➕
Platinum
➕
Battery Metals
➕
etc.
Receive all benefits from Option 1 or Option 2 delivered to numerous people at your company
➕
Multiple User names and Passwords for simultaneous log-ins
➕
Intranet integration access to all in your organisation