Improving efficiency, safety and profits with specialised equipment
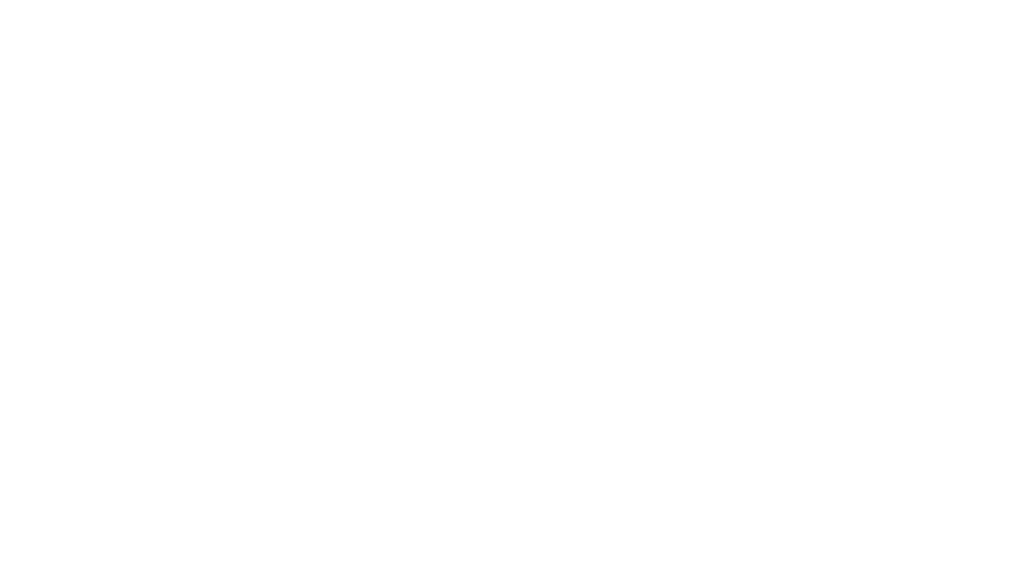
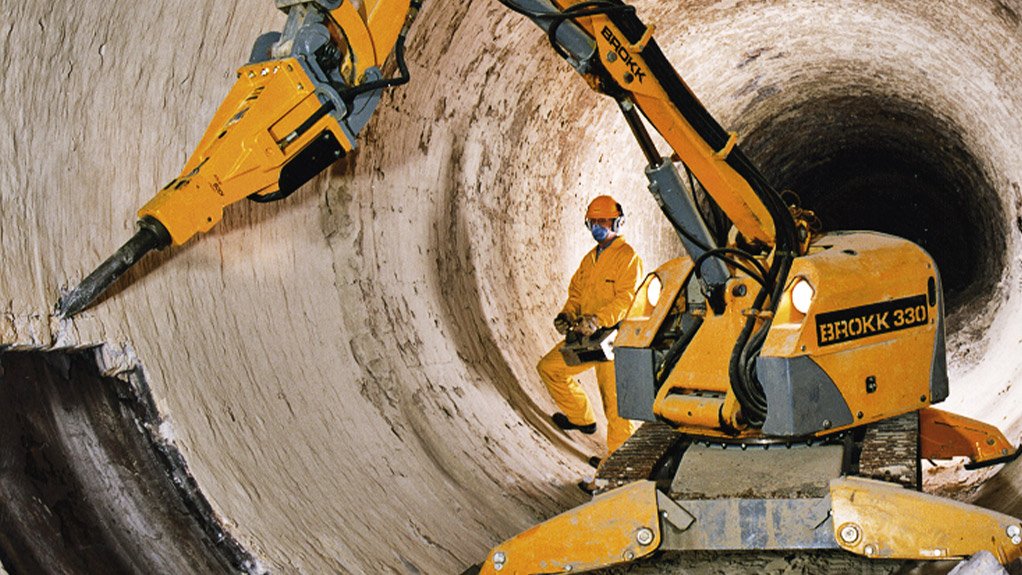
ACTION PLAN It is critical to implement a detailed and consistent plan of action, ensuring the safety of all persons during large, intricate, and complicated projects
There is a big opportunity to improve safety, efficiency and cost savings when it comes to kiln maintenance, says cement kiln equipment and bricking-machine manufacturer Bricking Solutions MD Heather Harding.
“Whether the challenge rests with plant personnel or a subcontractor, planning ahead and having the right equipment can prove both beneficial and profitable,” she adds.
Harding advises that the first thing plant managers or subcontractors should consider is what kind of ramp will be most suitable to access the inside of the kiln safely and efficiently. For example, ramps made with 6061-T6 aircraft aluminium offer a modular design, making it easy to manoeuver into place while providing ample capacity for a forklift or skid steer and materials.
Another challenge for facilities with large kilns is how to safely and efficiently install the bridge section. “This is often too difficult and unsafe for a forklift to install without assistance and, as a result, many plants continue to use an outdated bridge installation method.”
She states that this method is not the safest option as it uses an overhead hoist, along with a forklift and rigging to sling the bridge section across the cooler span into the kiln.
As such, Harding encourages plant personnel and subcontractors to rather use a load fixture as it is a more safe and efficient bridge installation method. A load fixture is a frame secured to the burn floor and door frame that features adjustable-height horizontal support beams.
The beams back the bridge section of the ramp using cables, while it is being extended across the cooler chamber. Installers can either roll the bridge section into place manually, or use a forklift to guide the load fixture and lower the bridge onto the kiln lip with the cable hoist.
Subsequently, once the method for accessing the kiln is determined, plant managers or contractors must decide how to safely inspect the kiln for hot spots and list necessary repairs. “Inspection can be incredibly dangerous, as it either requires the removal of coating or operating under potentially loose brickwork.”
Harding explains that the only way to significantly reduce the risk of injuries while inspecting a kiln during an outage is with a safety inspection cage. With a safety cage, masons entering the kiln remain protected from potential falling brick. Cages can also be attached to one another to provide a safe passageway through a burn zone when small tear-outs and repairs are required in the upper transition zone.
The most common safety inspection cage is made with lightweight, high-quality aluminium and is designed for two workers to carry into the kiln. One style of cage weighs about 90 kg and features two shoulder harnesses that place the weight on the workers’ torsos rather than arms, she says.
Further, these units also feature flip-up handles for balance control and can only be used in the kilns for which they are sized. The newest style of safety inspection cages, however, offer great versatility. These newer models weigh about 56 kg and do not require safety harnesses and can be used in 4-m- to 6-m-diameter kilns.
Another area plant personnel and subcontractors should focus on to ensure employee safety is during the refractory brick removal process, Harding underscores.
She also warns that handheld breakers – often used for brick removal – cause operator fatigue, lead to repetitive strain injuries while leaving operators vulnerable to falling brick.
“Remote-controlled demolition machines offered by Brokk – of which Bricking Solutions is a subsidiary – provide safer and more effective refractory removal. The machines are designed specifically for working in confined spaces and come in a range of sizes.”
The series is compact – as small as 1.9 ft wide and 2.8 ft tall – electronically powered and is lightweight to meet all international safety standards. Operators use the machine’s remote control to move its three-part arm 360º while a breaker attachment quickly and effectively removes brick.
“The equipment provides optimal precision and does not fatigue, dramatically reducing the chances of inadvertent kiln shell damage or damage to good brickwork,” she enthuses.
Moreover, in addition to more efficient brickwork demolition, kilns using a skid steer with a curved-bottom bucket attachment can more quickly load demolished refractory. The curved bottom of the bucket matches the curvature of the kiln, allowing the operator to capture more material and leave a cleaner surface in one pass, says Harding.
The bucket typically comes with a universal quick-hitch to fit most skid steer models and features a 12.7-mm T-1 steel beveled edge for a long wear life and optimal strength.
“Kiln maintenance is inevitable, but forgoing safety, efficiency and profits does not have to be. With specialised maintenance equipment designed for each step of the process, crews have greater control of the entire project, their safety and bottom lines,” she concludes.
Comments
Press Office
Announcements
What's On
Subscribe to improve your user experience...
Option 1 (equivalent of R125 a month):
Receive a weekly copy of Creamer Media's Engineering News & Mining Weekly magazine
(print copy for those in South Africa and e-magazine for those outside of South Africa)
Receive daily email newsletters
Access to full search results
Access archive of magazine back copies
Access to Projects in Progress
Access to ONE Research Report of your choice in PDF format
Option 2 (equivalent of R375 a month):
All benefits from Option 1
PLUS
Access to Creamer Media's Research Channel Africa for ALL Research Reports, in PDF format, on various industrial and mining sectors
including Electricity; Water; Energy Transition; Hydrogen; Roads, Rail and Ports; Coal; Gold; Platinum; Battery Metals; etc.
Already a subscriber?
Forgotten your password?
Receive weekly copy of Creamer Media's Engineering News & Mining Weekly magazine (print copy for those in South Africa and e-magazine for those outside of South Africa)
➕
Recieve daily email newsletters
➕
Access to full search results
➕
Access archive of magazine back copies
➕
Access to Projects in Progress
➕
Access to ONE Research Report of your choice in PDF format
RESEARCH CHANNEL AFRICA
R4500 (equivalent of R375 a month)
SUBSCRIBEAll benefits from Option 1
➕
Access to Creamer Media's Research Channel Africa for ALL Research Reports on various industrial and mining sectors, in PDF format, including on:
Electricity
➕
Water
➕
Energy Transition
➕
Hydrogen
➕
Roads, Rail and Ports
➕
Coal
➕
Gold
➕
Platinum
➕
Battery Metals
➕
etc.
Receive all benefits from Option 1 or Option 2 delivered to numerous people at your company
➕
Multiple User names and Passwords for simultaneous log-ins
➕
Intranet integration access to all in your organisation