New wear-resistant coating for pump components
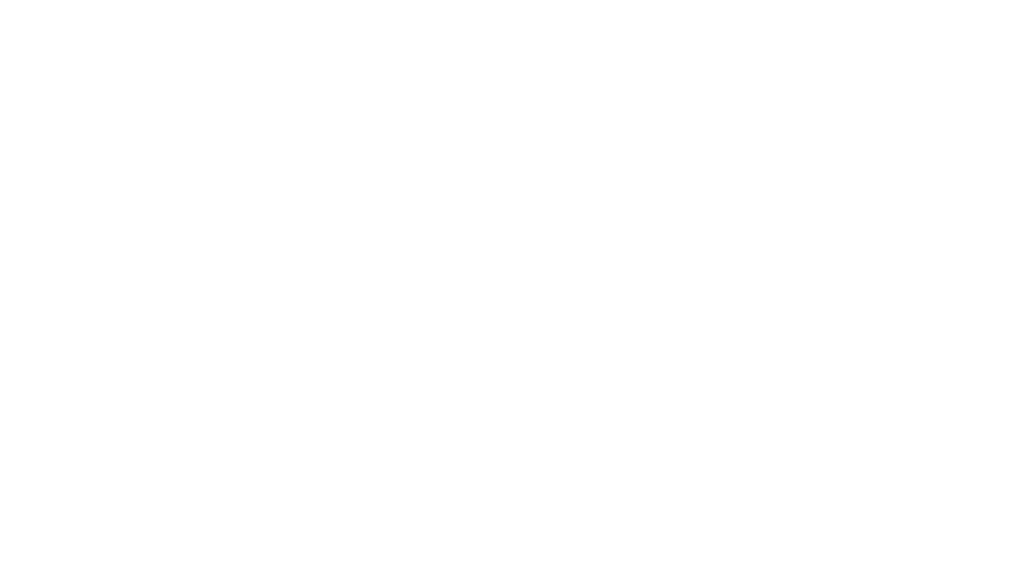
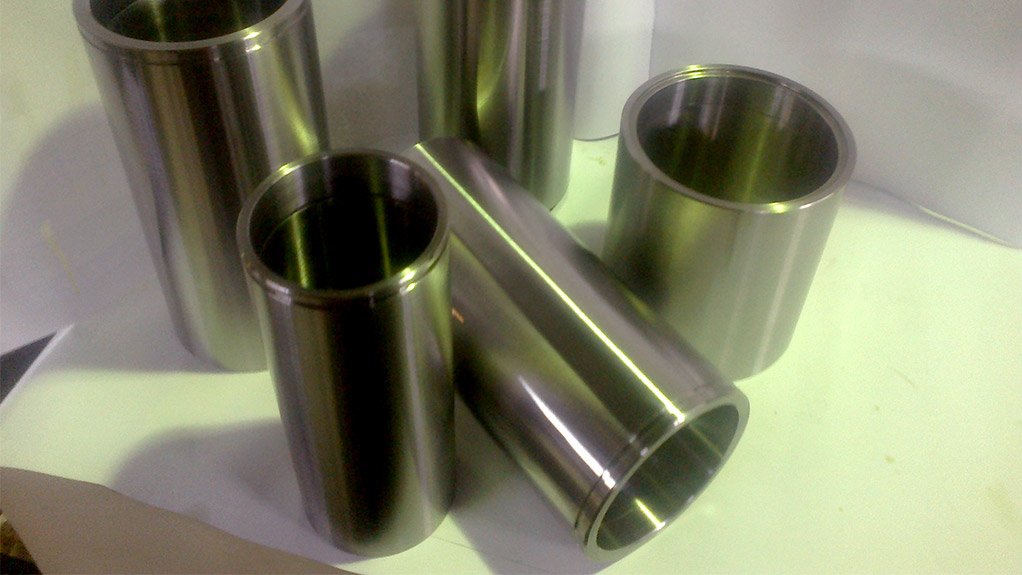
NEW COATING The hardness of the new coating ensures no brittleness, flaking or distortions
Local components manufacturer Carlmach Engineering has introduced a new wear- and impact-resistant (WAIR) coating, specifically designed for use in abrasive and slurry applications for pump components.
“The new coating can triple or quadruple a pump’s life cycle,” states Carlmach Engineering director Carlos Caeiro, adding that the company designed and developed the coating over the past two years with manufacturing company Kingbat Empire Trading.
“The coating can be applied onto most components made of ferrous materials such as mild steel, stainless steel, tool steel and cast iron,” he says, adding that the coating was developed to improve the operational efficiency and life cycle of pumps, reduce downtime and protect the pumps.
“The coatings are applied onto pump shaft sleeves and wear rings used in the pumps and mining industries, as the life cycles of these products can be problematic in these industries,” says marketing and sales manager Stan van Rooyen.
He adds that the coating will compete against the vanacarb, stelite, tungsten, hard chrome and ceramic coatings that are currently available on the market.
The coating is produced from a mixture of chrome, nickel and other chemical components, and comprises a hardness of 60 and 65 Rockwell. This hardness ensures no chipping, flaking, brittleness or distortion, Caeiro notes, adding that the coating can be applied to an entire component, whereas other coatings, such as chrome, have to be applied in such a way that the coating does not cover the ends of the components. This process for other coatings is necessary, as the coating tends to chip first at the end of the component, which can expose it to abrasion and corrosion.
The coating has also passed extreme in-house testing with high-concentration salts and extreme acids, which indicates that it is subject to little corrosion, he says, adding that the coating can be applied in thicknesses of 3 mm to 6 mm, as testing has shown that a 3 mm coating is adequate for most applications.
While the coating does not affect the components’ weight, components can be remachined to their original dimensions once the coating has been applied. Components can also be customised according to customer specifications, says Van Rooyen.
The coating process is undertaken on computer-controlled machines at the company’s facility in Springs, Gauteng. Two machines were designed and constructed by the company for the coating process and a third is being developed. The “unique” and undisclosed process of coating, as well as the associated machines, is in the process of being patented, says Van Rooyen.
He comments that the company has not received any adverse reports from clients using the components covered with the coating, nor any reports of microwelding, where metal particles of the different components can weld to each other spontaneously.
Caeiro explains that a company ordered a C5 sleeve with the WAIR coating for an extreme slurry application, where the pump never lasted more than 14 days. The sleeve was added to the pump and lasted more than 21 days before an impeller broke and the components had to be replaced.
“They replaced the components, but the same C5 sleeve was used again and the pump has been running for more than four weeks to date, which illustrates the increased life cycle of pumps when WAIR-coated components are used, ” he says.
Other advantages of the coating process include a faster lead time than other coating processes, such as stelites or vanacarb coating processes, as the company can process the coating faster than most other applications, Caeiro notes.
Other Coatings
While ongoing strikes and insecurity in the mining sector do affect business, orders for components, covered with the new coating, have increased by about 40% over the past year, with expectations of a steady growth increase, Caeiro notes.
The company plans to include the application of the WAIR coating in other pump components and general industry components.
In addition, the company is developing other coatings, such as a high chrome content coating and a tungsten coating for other applications and for the reconditioning of components.
Comments
Press Office
Announcements
What's On
Subscribe to improve your user experience...
Option 1 (equivalent of R125 a month):
Receive a weekly copy of Creamer Media's Engineering News & Mining Weekly magazine
(print copy for those in South Africa and e-magazine for those outside of South Africa)
Receive daily email newsletters
Access to full search results
Access archive of magazine back copies
Access to Projects in Progress
Access to ONE Research Report of your choice in PDF format
Option 2 (equivalent of R375 a month):
All benefits from Option 1
PLUS
Access to Creamer Media's Research Channel Africa for ALL Research Reports, in PDF format, on various industrial and mining sectors
including Electricity; Water; Energy Transition; Hydrogen; Roads, Rail and Ports; Coal; Gold; Platinum; Battery Metals; etc.
Already a subscriber?
Forgotten your password?
Receive weekly copy of Creamer Media's Engineering News & Mining Weekly magazine (print copy for those in South Africa and e-magazine for those outside of South Africa)
➕
Recieve daily email newsletters
➕
Access to full search results
➕
Access archive of magazine back copies
➕
Access to Projects in Progress
➕
Access to ONE Research Report of your choice in PDF format
RESEARCH CHANNEL AFRICA
R4500 (equivalent of R375 a month)
SUBSCRIBEAll benefits from Option 1
➕
Access to Creamer Media's Research Channel Africa for ALL Research Reports on various industrial and mining sectors, in PDF format, including on:
Electricity
➕
Water
➕
Energy Transition
➕
Hydrogen
➕
Roads, Rail and Ports
➕
Coal
➕
Gold
➕
Platinum
➕
Battery Metals
➕
etc.
Receive all benefits from Option 1 or Option 2 delivered to numerous people at your company
➕
Multiple User names and Passwords for simultaneous log-ins
➕
Intranet integration access to all in your organisation