Reducing corrosion in waste heat boilers
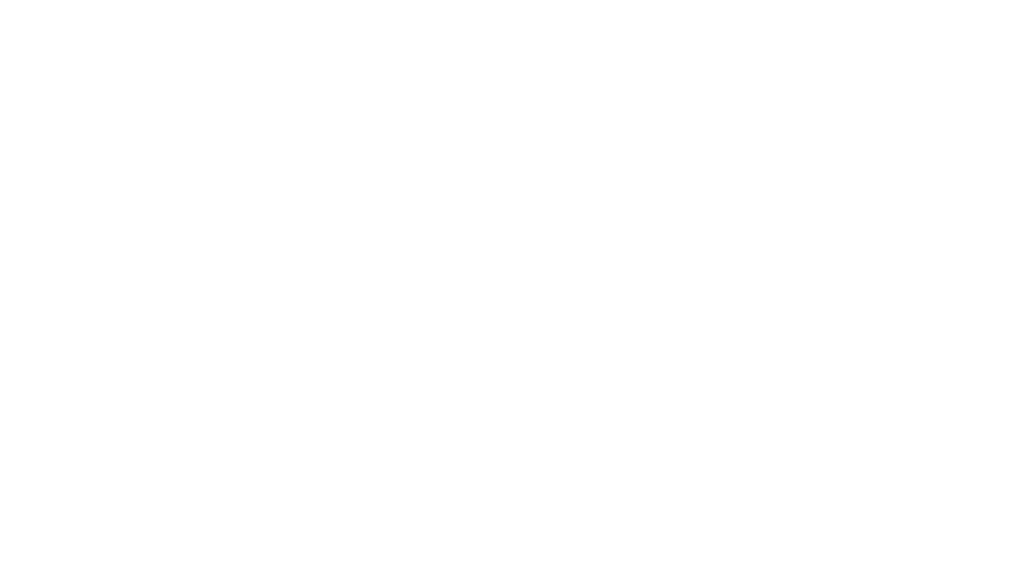
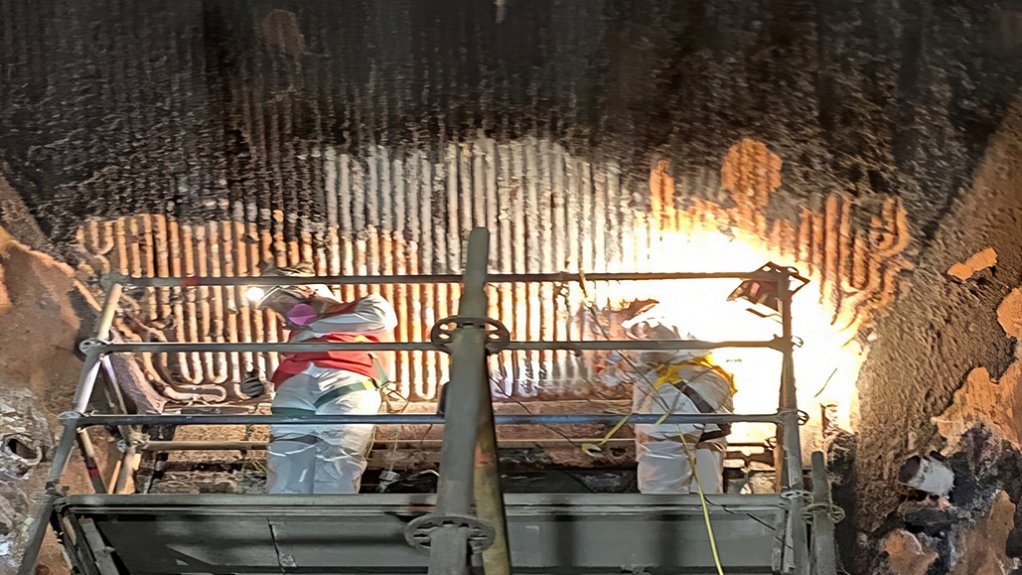
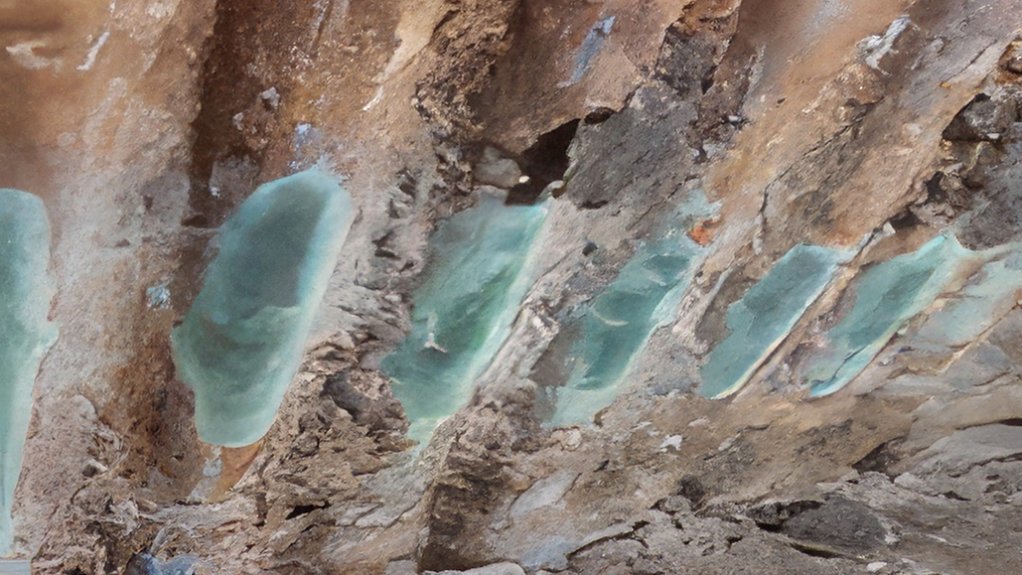
APPLICATION OF HVTS With HVTS being engineered for the mining and mineral processing industry, it provides a better bond strength with excellent corrosion and wear resistance
Photo by IGS
CORROSION OF WASTE HEAT BOILERS The extremely high temperatures circulating within boilers start to affect waterwalls, often resulting in areas of the boiler wall becoming completely depleted
Photo by IGS
The corrosion of waste heat boilers (WHBs) – which are crucial in the recovery and use of heat generated as a by-product by non-ferrous pyrometallurgical plants globally – has a detrimental impact on asset life and overall performance, according to international surface protection solutions provider Integrated Global Services (IGS).
The flue gas stream within a smelting furnace WHB has comparatively high dust content, that may either slag on the surface depending on its melting point temperature or erode waterwalls. In general, metal oxides are present in the dust and are characterised as very erosive media.
Flue gas originating from sulphur-containing fuel becomes corrosive below a temperature of about 150 °C. Local cold spots in metal air preheaters lead to rapid breakdown and corrosion of tubes and plates.
This type of corrosion is one of the key factors that negatively affect the energy efficiency of WHBs.
Further, the extremely high temperatures – which may reach around 1 350 °C – circulating within the boiler start to affect waterwalls. This ongoing process will result in areas of the boiler wall becoming completely depleted and require costly shutdowns and urgent repair to operate efficiently.
The high velocity thermal spray (HVTS) by IGS offers a potential solution for extending the lifespan of existing smelting equipment by acting as an erosion barrier in critical apparatus.
Developed for safe on-site application, HVTS is a nonpermeable thermal-spray-applied alloy cladding material specifically designed for corrosion and erosion resistance in high-temperature smelting and mineral refining environments.
With HVTS being engineered for the mining and mineral processing industry, it provides a better bond strength with excellent corrosion and wear resistance. The solution is designed for fast on-site application, facilitating a quick return to service. Its ability to withstand challenging environments makes it a suitable choice in instances where other coatings fall short.
Practical Application
IGS recently completed a project focused on the improvement of the reliability and lifespan of a WHB in a collaborative initiative with a leading global copper smelting operation.
The copper smelter plant encountered significant challenges in relation to the WHB, with a service life of critical panels limited to only 11 to 18 months. This recurrent issue resulted in prolonged downtime, elevated replacement expenses, and logistical complications, further exacerbated by disruptions in the supply chain owing to the Covid-19 pandemic.
IGS addressed these challenges with the introduction of an HVTS alloy cladding solution, aimed at extending the intervals between turnarounds. The successful implementation of this solution mitigated downtime and replacement costs.
The copper smelter, in Chile, had been grappling with corrosion and erosion problems in its WHB, and had traditionally relied on panel and single tube replacements, as well as weld build-up strategies.
An important moment arose when a representative of the plant discovered a WHB reliability project executed by IGS and approached the company in search of alternative solutions. A comprehensive technical presentation to the plant’s maintenance and commercial teams followed.
As a result of successful presentations and in-depth discussions, IGS secured a contract for the application of its proprietary HVTS high-nobility alloy cladding over a 70 m2 area. The application took place in a laydown yard in October 2022, strategically targeting critical areas of the WHB.
The WHB operated continuously until the end of September 2023. In August, in anticipation of an outage, IGS mobilised an inspection crew, including the local representatives from Chile. Despite the tight five-hour window, the team conducted a thorough inspection using magnetic lift-off gauge testing.
The project addressing the WHB demonstrated the company’s commitment to finding effective solutions, and showed that a proactive approach and proven methods can contribute to overcoming operational challenges while potentially extending asset life and enhancing productivity.
The examination of WHB challenges in copper smelters highlights the critical role these boilers play in the efficient extraction of metals. The corrosive effects of high temperature sulfidation pose significant threats to the operational longevity and overall performance of these crucial assets.
Through collaborative efforts, and successful outcomes with prior projects as a valuable reference, the enhancement of the performance and reliability of WHBs and other critical components in similar environments is achievable for industries seeking reliable solutions.
Comments
Press Office
Announcements
What's On
Subscribe to improve your user experience...
Option 1 (equivalent of R125 a month):
Receive a weekly copy of Creamer Media's Engineering News & Mining Weekly magazine
(print copy for those in South Africa and e-magazine for those outside of South Africa)
Receive daily email newsletters
Access to full search results
Access archive of magazine back copies
Access to Projects in Progress
Access to ONE Research Report of your choice in PDF format
Option 2 (equivalent of R375 a month):
All benefits from Option 1
PLUS
Access to Creamer Media's Research Channel Africa for ALL Research Reports, in PDF format, on various industrial and mining sectors
including Electricity; Water; Energy Transition; Hydrogen; Roads, Rail and Ports; Coal; Gold; Platinum; Battery Metals; etc.
Already a subscriber?
Forgotten your password?
Receive weekly copy of Creamer Media's Engineering News & Mining Weekly magazine (print copy for those in South Africa and e-magazine for those outside of South Africa)
➕
Recieve daily email newsletters
➕
Access to full search results
➕
Access archive of magazine back copies
➕
Access to Projects in Progress
➕
Access to ONE Research Report of your choice in PDF format
RESEARCH CHANNEL AFRICA
R4500 (equivalent of R375 a month)
SUBSCRIBEAll benefits from Option 1
➕
Access to Creamer Media's Research Channel Africa for ALL Research Reports on various industrial and mining sectors, in PDF format, including on:
Electricity
➕
Water
➕
Energy Transition
➕
Hydrogen
➕
Roads, Rail and Ports
➕
Coal
➕
Gold
➕
Platinum
➕
Battery Metals
➕
etc.
Receive all benefits from Option 1 or Option 2 delivered to numerous people at your company
➕
Multiple User names and Passwords for simultaneous log-ins
➕
Intranet integration access to all in your organisation