Reliability contract improves performance
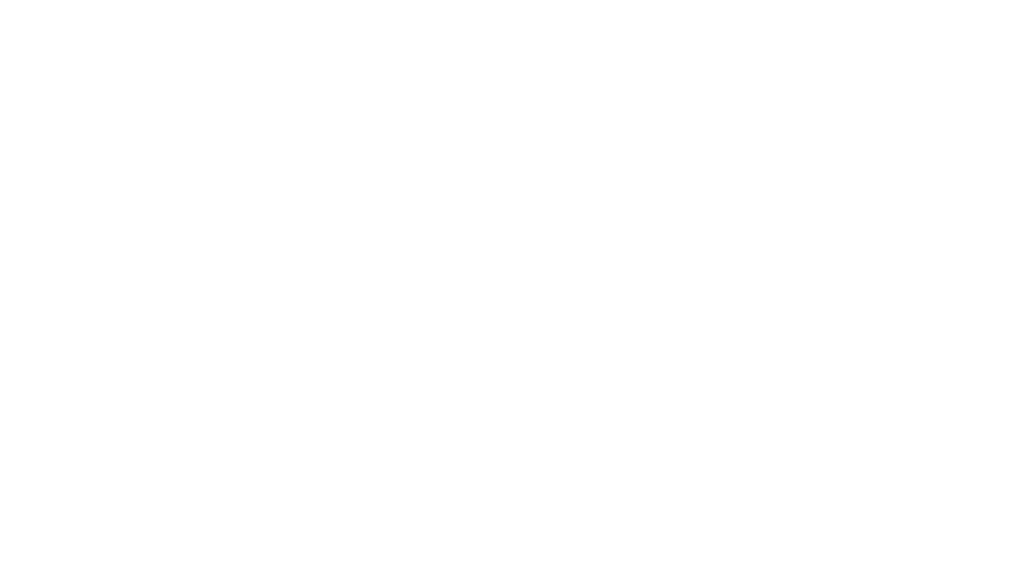
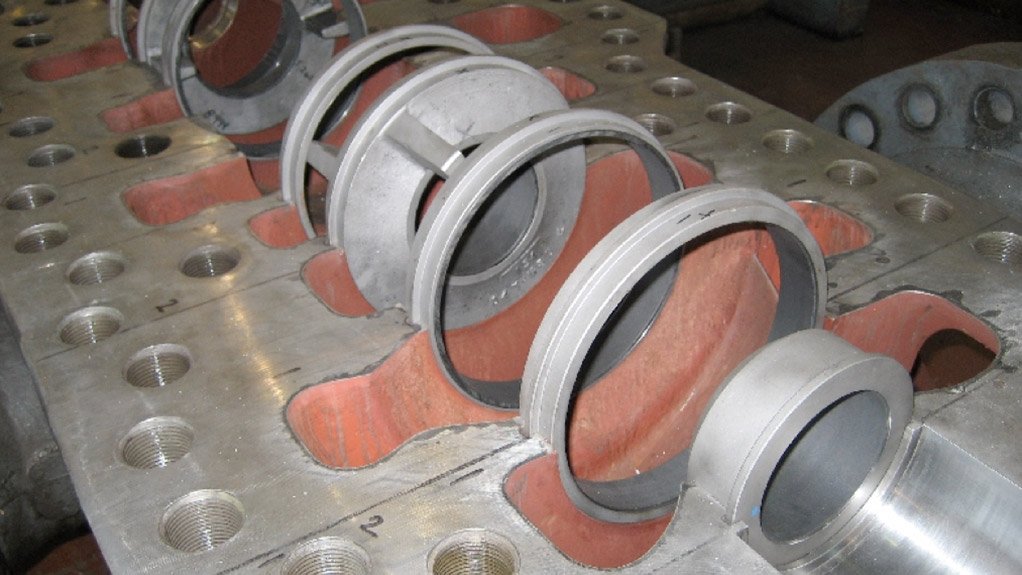
RELIABLE PUMPING The John Crane Performance Plus team ensured that standards set by the American Petroleum Institute were met at all times
A second-term contract to enhance the reliability of 565 pumps at Cape Town-based oil refinery Chevron has been improved through training the site personnel and mechanical seals manufacturer John Crane’s constantly monitoring the pumps.
John Crane reliability manager Renee Buijs tells Engineering News the contract aims to improve the reliability of the installed base of pumps over a five-year period, starting August 1.
John Crane’s previous five-year contract with Chevron ended on July 31 this year and Buijs says, with the second-term contract, the company was able to offer Chevron a 2% reduction in cost.
In addition to maintaining the hundreds of pumps and their seals, the Performance Plus (PP) team, a division of John Crane, was also tasked with increasing safety at the plant regarding the many pumps at the plant. “Safety is a crucial aspect at refineries and we needed to ensure that standards set by the American Petroleum Institute (API) were met at all times on the 610 eleventh edition and API 682 third edition pumps at the plant,” he says.
Further, the PP team assisted in reducing Chevron’s on-site stockholding of seals, and the management of seals and pumps for the refinery.
The reliability of a pump and seal is measured according to the mean time between component failures, regardless of the mode of failure, which can vary, owing to different components failing at different stages, says Buijs. “We are striving to extend the mean time between failure by several months compared with when we began the contract.”
Therefore, pumps are constantly monitored in terms of operating pressure, temperature, vibration and their mechanical seals. PP team on-site engineer Marius Burger, who works in conjunction with Chevron’s reliability team, analyses the pumps through daily inspections while they are in operation.
“By analysing the seal, you can determine the failure mode of the pump,” says Buijs, adding that John Crane technicians can then follow a strategy to mitigate the failure mode of the pump and keep it running for longer.
“Technicians can make changes to the pump, recondition the seal or replace it, or replace other faulty components in the pump, such as bearings, to resolve the issue,” he says.
However, if there is a process-related issue, technicians will consult with the process department and advise them on how to better deal with the situation in future, notes Buijs.
Further, monitoring the pumps while they are operating assists with preventative maintenance. “If discrepancies are observed, the pump can be removed so that a technician can conduct an in-depth analysis and sort out the issue before it results in a catastrophic failure,” he says.
The starting of pumps is the most crucial stage of the plant operation, Buijs tells Engineering News, as “start-up is when 80% of pump failures occur or originate from”.
During the start-up of the pumps, the PP team and Chevron technicians closely observe the pumps and rotating equipment to prevent possible damage from occurring, says Buijs.
“The technicians ensure all the checks and balances are put in place before the system or individual pieces of equipment are started, which includes ensuring that all valves are open, the system is correctly primed, seals are vented and pressures are correct,” he adds.
Training
About 60% of the refinery’s pumps require component seals, which are significantly difficult to install, subsequently complicating maintenance processes.
A component seal has to be assembled while it is on the pump. Technicians are trained to ensure they do not mistakenly cause a failure, known as an installation failure, while they are installing the seal,” says Buijs.
The remaining 40% of the pumps require cartridge seals, “which are much easier to install and require less training”, he adds.
Further, John Crane conducts the on-site training of Chevron personnel, which is an ongoing operation. “Over the last five years, several hundred staff members have been trained by us,” boasts Buijs.
The training has assisted in preventing start-up and installation failures when the seals or the pump itself have been maintained or installed incorrectly.
The major savings are reflected in the number of pumps that have to be removed, as fewer pumps need to be taken off line at any time, reducing the overall risk of downtime at a refinery, he concludes.
Comments
Press Office
Announcements
What's On
Subscribe to improve your user experience...
Option 1 (equivalent of R125 a month):
Receive a weekly copy of Creamer Media's Engineering News & Mining Weekly magazine
(print copy for those in South Africa and e-magazine for those outside of South Africa)
Receive daily email newsletters
Access to full search results
Access archive of magazine back copies
Access to Projects in Progress
Access to ONE Research Report of your choice in PDF format
Option 2 (equivalent of R375 a month):
All benefits from Option 1
PLUS
Access to Creamer Media's Research Channel Africa for ALL Research Reports, in PDF format, on various industrial and mining sectors
including Electricity; Water; Energy Transition; Hydrogen; Roads, Rail and Ports; Coal; Gold; Platinum; Battery Metals; etc.
Already a subscriber?
Forgotten your password?
Receive weekly copy of Creamer Media's Engineering News & Mining Weekly magazine (print copy for those in South Africa and e-magazine for those outside of South Africa)
➕
Recieve daily email newsletters
➕
Access to full search results
➕
Access archive of magazine back copies
➕
Access to Projects in Progress
➕
Access to ONE Research Report of your choice in PDF format
RESEARCH CHANNEL AFRICA
R4500 (equivalent of R375 a month)
SUBSCRIBEAll benefits from Option 1
➕
Access to Creamer Media's Research Channel Africa for ALL Research Reports on various industrial and mining sectors, in PDF format, including on:
Electricity
➕
Water
➕
Energy Transition
➕
Hydrogen
➕
Roads, Rail and Ports
➕
Coal
➕
Gold
➕
Platinum
➕
Battery Metals
➕
etc.
Receive all benefits from Option 1 or Option 2 delivered to numerous people at your company
➕
Multiple User names and Passwords for simultaneous log-ins
➕
Intranet integration access to all in your organisation