Manufacturer boosts vessel hygiene with CIP optimised equipment
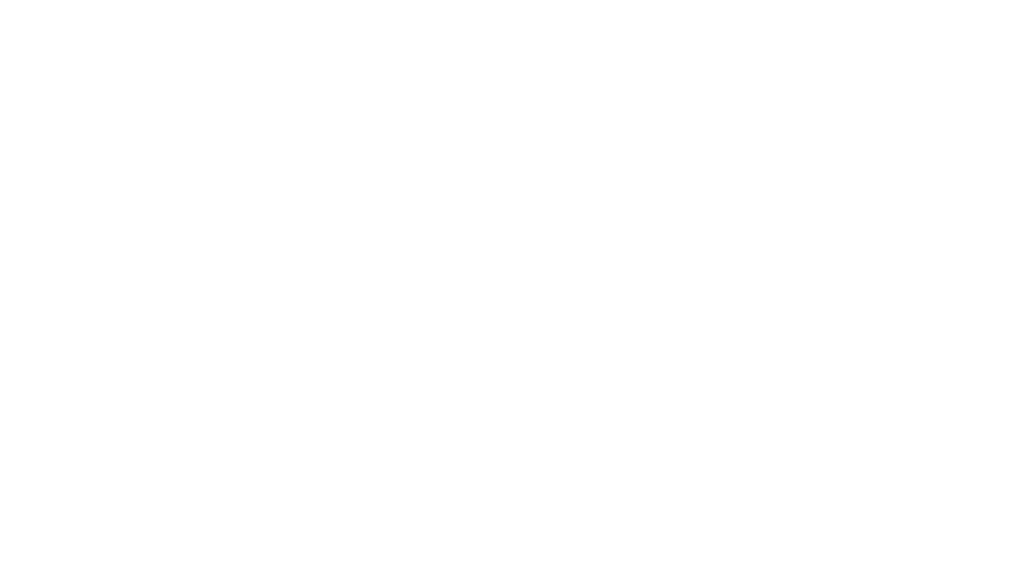
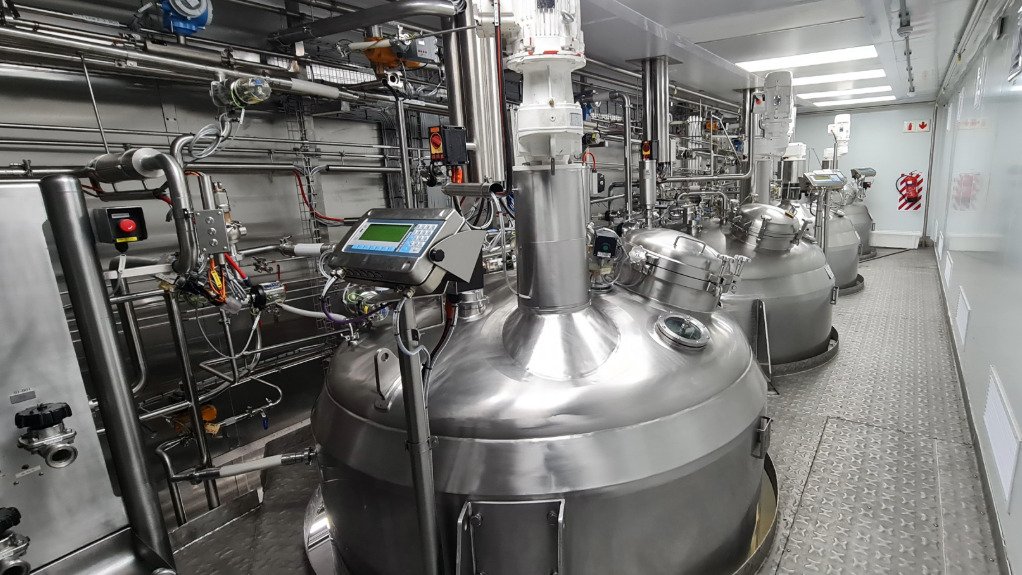
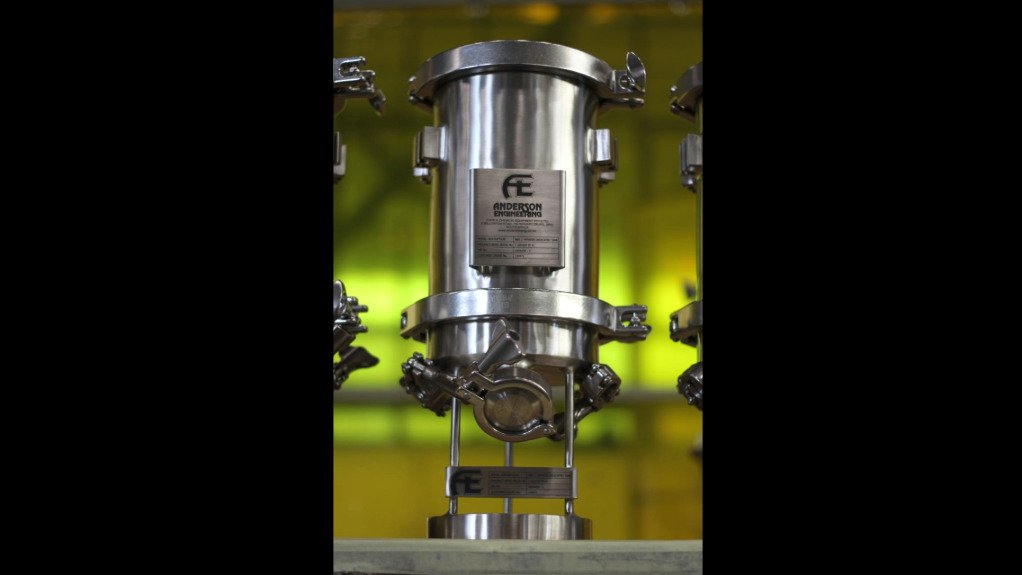
DEAD LEG PREVENTION To avoid stagnation, the pipework and vessels are sloped, facilitating complete drainage following processing or cleaning to prevent microbial growth
Photo by Anderson Engineering
DECREASING HUMAN ERROR The clean-in-place process design by Anderson Engineering is automated to reduce human error while ensuring that there is a consistent, repeatable cleaning
Photo by Anderson Engineering
Processing equipment manufacturer Anderson Engineering emphasises a holistic approach to system design and component selection, as well as attention to detail during fabrication and installation, in support of clean-in-place (CIP) and hygiene requirements for food and pharmaceutical applications.
The first consideration is the selection of materials that will meet industry standards for hygiene and corrosion resistance, says Anderson Engineering MD Hennie de Jager.
Stainless steel – 316 L in particular – is often chosen for its durability, chemical resistance and suitability for high-sterility environments. The choice of other materials in the process, like elastomers, is also influenced by their compatibility with CIP chemicals to ensure long-term durability and cleanliness.
Following the selection of materials, Anderson Engineering considers the surface finish requirements, owing to the quality of these finishes being a vital component in hygienic design.
“Our products for food and pharmaceutical applications are designed with a high- quality polished finish for product contact areas, typically surface roughness average RA≤ 0.4 µm. This smooth finish minimises microbial adhesion and makes residue removal easier during CIP cycles,” explains De Jager.
Correct nozzle design is essential to effective CIP, which relies on precise nozzle placement and minimum nozzle length on the tanks to ensure thorough coverage and impact of cleaning solutions (typically Caustic Soda) from the spray balls.
Proper positioning allows the solution to reach all surfaces and dislodge residues with adequate force, and promotes efficient flow and drainage, minimising areas where contaminants might remain.
This strategic nozzle design maximises cleaning efficiency, and reduces time and cleaning chemical quantities needed, helping prevent cross-contamination, thereby making it essential in meeting high standards in industries such as food, pharmaceutical, and chemical processing.
To avoid “dead legs” – the sections of piping where fluids can stagnate – and ensure a thorough cleaning, Anderson Engineering’s equipment allows for full line drainage and optimal cleaning velocity during CIP of these lines.
The pipework and vessels are sloped to avoid build-up and stagnation while facilitating complete drainage after processing or cleaning. This is important to prevent microbial growth, as “pooled residues or cleaning solutions could become contamination points”, explains De Jager.
The company also ensures that the spray balls or rotating spray heads are positioned and selected based on the size and geometry of every vessel.
The effectiveness of the coverage from these spray balls will ensure that surfaces are thoroughly cleaned without leaving any blind spots. Computer-aided design allows for the creation of simulations and thorough three- dimensional (3D) evaluations of vessels and components during design, prior to fabrication.
“This allows us to design for maximum coverage with the spray balls and minimise unwanted design features like crevasses in the vessel assembly and shadow areas that would not be easily observable without the 3D models.”
Anderson Engineering recommends that hygienic pumps and instruments comply with nonprofit consortium of food processors the European Hygienic Engineering and Design Group and the US’ 3-A Sanitary Standards to ensure ease of cleaning and minimise crevices.
These designs include the diaphragm and centrifugal pumps with cleanable seals, as well as flow meters, temperature sensors and valves that are suited to environments where hygiene must be maintained.
“Our CIP systems are customised with optimised cycles to achieve efficient cleaning. These procedures include the use of validated cleaning agents at appropriate concentrations, flow rates and temperatures,” states De Jager.
He adds that this effectively removes residues while decreasing the possibility of microbial contamination. Additionally, the CIP process is automated as much as possible to reduce human error and ensure there is consistent, repeatable cleaning.
The company has also incorporated and adopted validation tools – such as Riboflavin testing to evaluate spray ball coverage – to test and validate its designs against hygiene requirements and expectations for the food and pharmaceutical industries.
De Jager states that “each piece of equipment is carefully evaluated to ensure it complies with stringent cleanliness standards, helping clients maintain hygienic and sterile production environments”.
Project Integration
Anderson Engineering’s commitment to ensuring its solutions can be seamlessly integrated into existing, new or standalone processes is supported and underscored by its ISO 3834 and ISO 9001:2015 accreditations, which form the backbone of the company’s fabrication, installation and on-site procedures.
De Jager says that, before beginning any project, the company’s sales and process engineers will conduct thorough site visits and review the existing and proposed processes by capturing and comparing them using piping and instrumentation diagrams to ensure full understanding of integration requirements.
“This careful planning enables us to fabricate, install and commission vessels and processes that align with site specifications and are primed for successful incorporation with minimal disruptions.”
The company’s experienced process and installation engineers collaborate closely with clients to achieve general assembly approval and its in-house process engineers ensure that each vessel integrates smoothly with the existing automation systems on customers’ sites.
The company manages the full validation process, including factory acceptance testing, design qualification, installation qualification, operational qualification and performance qualification.
De Jager concludes that this comprehensive approach ensures that Anderson Engineering’s solutions meet rigorous requirements and provide reliable, optimised performance.
Comments
Press Office
Announcements
What's On
Subscribe to improve your user experience...
Option 1 (equivalent of R125 a month):
Receive a weekly copy of Creamer Media's Engineering News & Mining Weekly magazine
(print copy for those in South Africa and e-magazine for those outside of South Africa)
Receive daily email newsletters
Access to full search results
Access archive of magazine back copies
Access to Projects in Progress
Access to ONE Research Report of your choice in PDF format
Option 2 (equivalent of R375 a month):
All benefits from Option 1
PLUS
Access to Creamer Media's Research Channel Africa for ALL Research Reports, in PDF format, on various industrial and mining sectors
including Electricity; Water; Energy Transition; Hydrogen; Roads, Rail and Ports; Coal; Gold; Platinum; Battery Metals; etc.
Already a subscriber?
Forgotten your password?
Receive weekly copy of Creamer Media's Engineering News & Mining Weekly magazine (print copy for those in South Africa and e-magazine for those outside of South Africa)
➕
Recieve daily email newsletters
➕
Access to full search results
➕
Access archive of magazine back copies
➕
Access to Projects in Progress
➕
Access to ONE Research Report of your choice in PDF format
RESEARCH CHANNEL AFRICA
R4500 (equivalent of R375 a month)
SUBSCRIBEAll benefits from Option 1
➕
Access to Creamer Media's Research Channel Africa for ALL Research Reports on various industrial and mining sectors, in PDF format, including on:
Electricity
➕
Water
➕
Energy Transition
➕
Hydrogen
➕
Roads, Rail and Ports
➕
Coal
➕
Gold
➕
Platinum
➕
Battery Metals
➕
etc.
Receive all benefits from Option 1 or Option 2 delivered to numerous people at your company
➕
Multiple User names and Passwords for simultaneous log-ins
➕
Intranet integration access to all in your organisation