Time to get PDS-ready is now
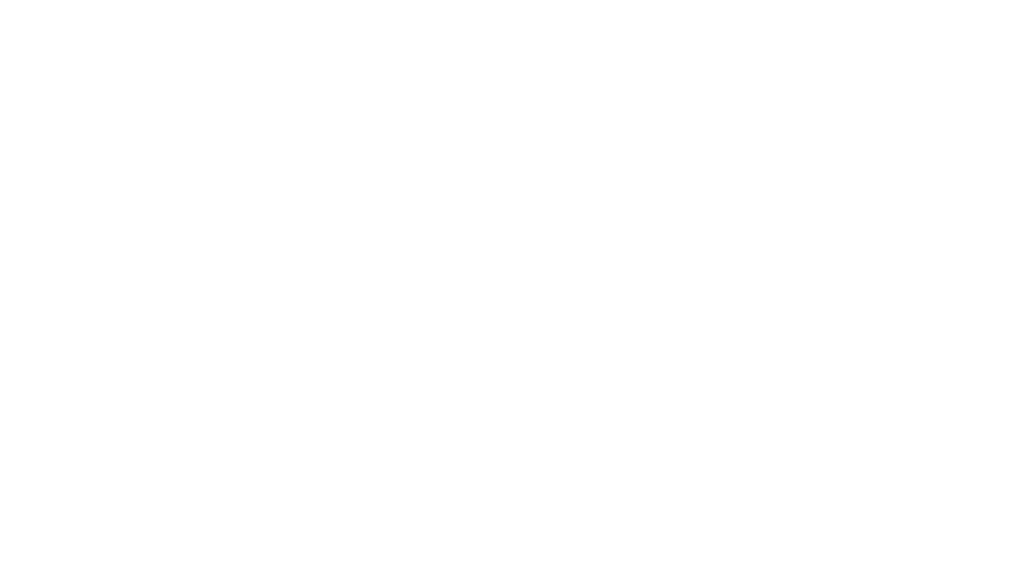
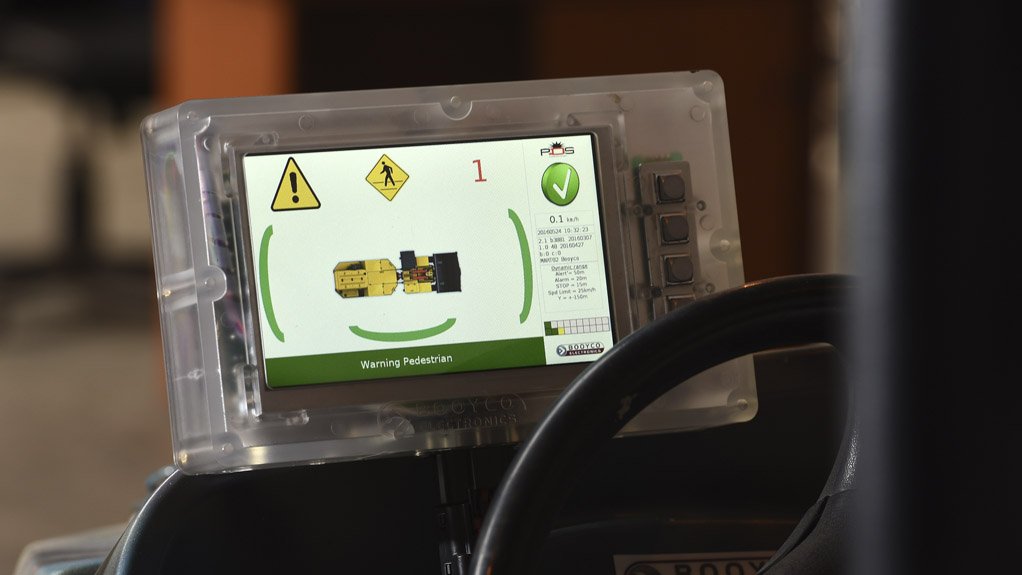
PROXIMITY DETECTION SYSTEMS The Booyco PDS warns when pedestrians enter the area around a machine
As of June, all new original-equipment manufacturer (OEM) trackless mobile machines (TMMs) bought by mining houses need to be proximity detection system- (PDS-) ready.
“This is my understanding from the last feedback we received from the Department of Mineral Resources (DMR),” says mine safety equipment supplier Booyco Electronics MD Anton Lourens, adding that a grandfather clause states that all TMMs should be fitted with PDSes by June 2019.
Divided into two parts under Chapter 8 of the Mine Health and Safety Act (MHSA), which governs the use of PDSes on TMMs by South African mines, the legislation firstly necessitates that mining companies – based on an approved risk assessment – implement an automatic detection system that audibly or visually warns TMM operators of an imminent collision.
The second part of the legislation stipulates that the operating system of OEM TMMs must comprise an automatic fail-safe to bring the equipment to a standstill to prevent a collision if an operator fails to react in time.
Chapter 8 of the MHSA was amended and gazetted in February 2015 and covers underground electrical machines, underground diesel machines, surface diesel machines and surface operations, Lourens explains.
Diesel Dilemma
“With electrical machinery, the legislation is quite clear. However, the legislation is unclear when referring to diesel equipment, as it only currently calls for these vehicles to be equipped with a collision warning system.”
Following the gazetting of the Chapter 8 amendment, he notes that the mining industry has held many workshops to understand whether the requirements for diesel equipment are practical to implement.
“These requirements constitute three parts – mine-specific requirements, which pertain to a mine’s specific operational requirements; the type of OEM machinery in operation at a mine and the suitable PDS technologies available.”
This, he adds, is where the confusion regarding legislation comes in, noting that, as it stands, no single type of technology can address each possible scenario identified through risk assessments from a PDS point of view, as different mining operations have specific operational requirements and risks that are based on their mine designs.
There are too many variables, Lourens declares; however, accountability lies with the mine owner to ensure that the significant risks that are identified, are addressed. “Ultimately it’s the mine’s responsibility to identify significant risks through a risk assessment and address these risks accordingly,” he says.
In the case of an accident, Lourens says, DMR officials will require mines to present their risk assessment, review and report on whether the risk has been adequately addressed beforehand.
He further explains that opinions vary regarding the definition of a PDS, as there are various technologies available that cater for proximity detection in the numerous and greatly varying specific scenarios.
“Some mining houses have identified sonar or radar technology, while others use radio frequency identification or cameras as PDSes. The selection of the correct PDS is based on a mine’s risk assessment and the scenarios it needs to deal with,” Lourens says, stressing that, should the wrong technology be implemented for proximity- detection purposes, all equipment may need replacing to ensure compliance.
The consequences of noncompliance can be extreme and costly, he notes.
“Noncompliance can lead to a Section 54 stoppage, which forces mines to implement a solution very quickly or face possible further prosecution,” Lourens concludes.
Comments
Press Office
Announcements
What's On
Subscribe to improve your user experience...
Option 1 (equivalent of R125 a month):
Receive a weekly copy of Creamer Media's Engineering News & Mining Weekly magazine
(print copy for those in South Africa and e-magazine for those outside of South Africa)
Receive daily email newsletters
Access to full search results
Access archive of magazine back copies
Access to Projects in Progress
Access to ONE Research Report of your choice in PDF format
Option 2 (equivalent of R375 a month):
All benefits from Option 1
PLUS
Access to Creamer Media's Research Channel Africa for ALL Research Reports, in PDF format, on various industrial and mining sectors
including Electricity; Water; Energy Transition; Hydrogen; Roads, Rail and Ports; Coal; Gold; Platinum; Battery Metals; etc.
Already a subscriber?
Forgotten your password?
Receive weekly copy of Creamer Media's Engineering News & Mining Weekly magazine (print copy for those in South Africa and e-magazine for those outside of South Africa)
➕
Recieve daily email newsletters
➕
Access to full search results
➕
Access archive of magazine back copies
➕
Access to Projects in Progress
➕
Access to ONE Research Report of your choice in PDF format
RESEARCH CHANNEL AFRICA
R4500 (equivalent of R375 a month)
SUBSCRIBEAll benefits from Option 1
➕
Access to Creamer Media's Research Channel Africa for ALL Research Reports on various industrial and mining sectors, in PDF format, including on:
Electricity
➕
Water
➕
Energy Transition
➕
Hydrogen
➕
Roads, Rail and Ports
➕
Coal
➕
Gold
➕
Platinum
➕
Battery Metals
➕
etc.
Receive all benefits from Option 1 or Option 2 delivered to numerous people at your company
➕
Multiple User names and Passwords for simultaneous log-ins
➕
Intranet integration access to all in your organisation